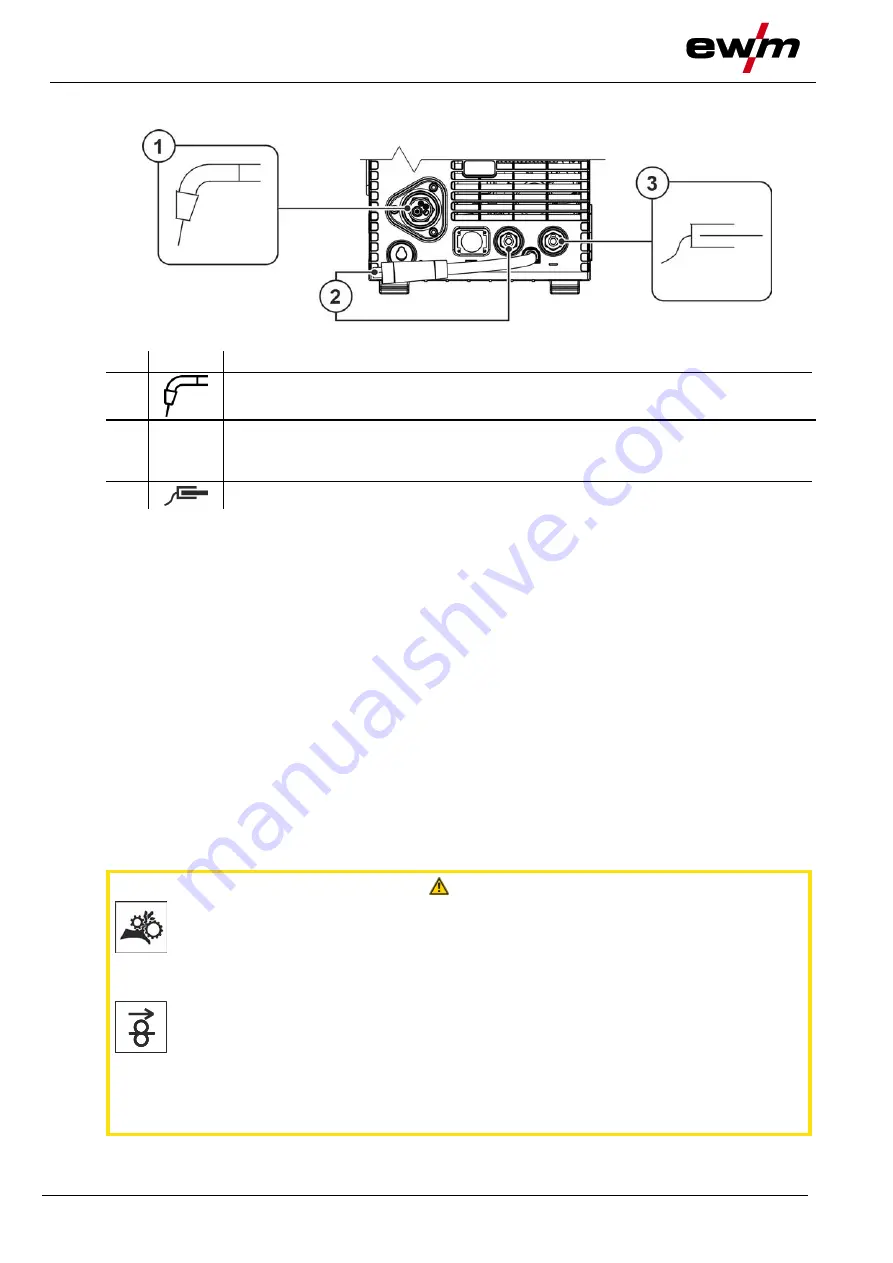
Design and function
MIG/MAG welding
36
099-005403-EW501
10.2.2022
5.3.2 Welding torch and workpiece line connection
Figure 5-15
Item Symbol Description
0
1
Welding torch
2
Polarity selector plug, welding current cable
Internal welding current cable for central connection/welding torch.
• ---------- Connection socket for “+” welding current
3
Workpiece
• Insert the polarity selection plug into the "+" welding current connection socket and lock in place by
turning to the right.
• Insert the central plug for the welding torch into the central connector and screw together with crown
nut.
• Insert cable plug on the workpiece lead into the "-" welding current socket and lock by turning to the
right.
If fitted:
• Insert the welding torch control cable into the 19-pole connection socket and lock (MIG/MAG torches
with additional control cables only).
• Lock connecting nipples of the cooling water tubes into the corresponding quick connect couplings:
Return line red to quick connect coupling, red (coolant return) and
supply line blue to quick connect coupling, blue (coolant supply).
Some wire electrodes (e.g. self-shielding cored wire) are welded using negative polarity. In this
case, the welding current lead should be connected to the "-" welding current socket, and the
workpiece lead should be connected to the "+" welding current socket. Observe the information
from the electrode manufacturer!
5.3.3 Wire feed
CAUTION
Risk of injury due to moving parts!
The wire feeders are equipped with moving parts, which can trap hands, hair, clothing
or tools and thus injure persons!
• Do not reach into rotating or moving parts or drive components!
• Keep casing covers or protective caps closed during operation!
Risk of injury due to welding wire escaping in an unpredictable manner!
Welding wire can be conveyed at very high speeds and, if conveyed incorrectly, may es-
cape in an uncontrolled manner and injure persons!
• Before mains connection, set up the complete wire guide system from the wire spool to the
welding torch!
• Check wire guide at regular intervals!
• Keep all casing covers or protective caps closed during operation!