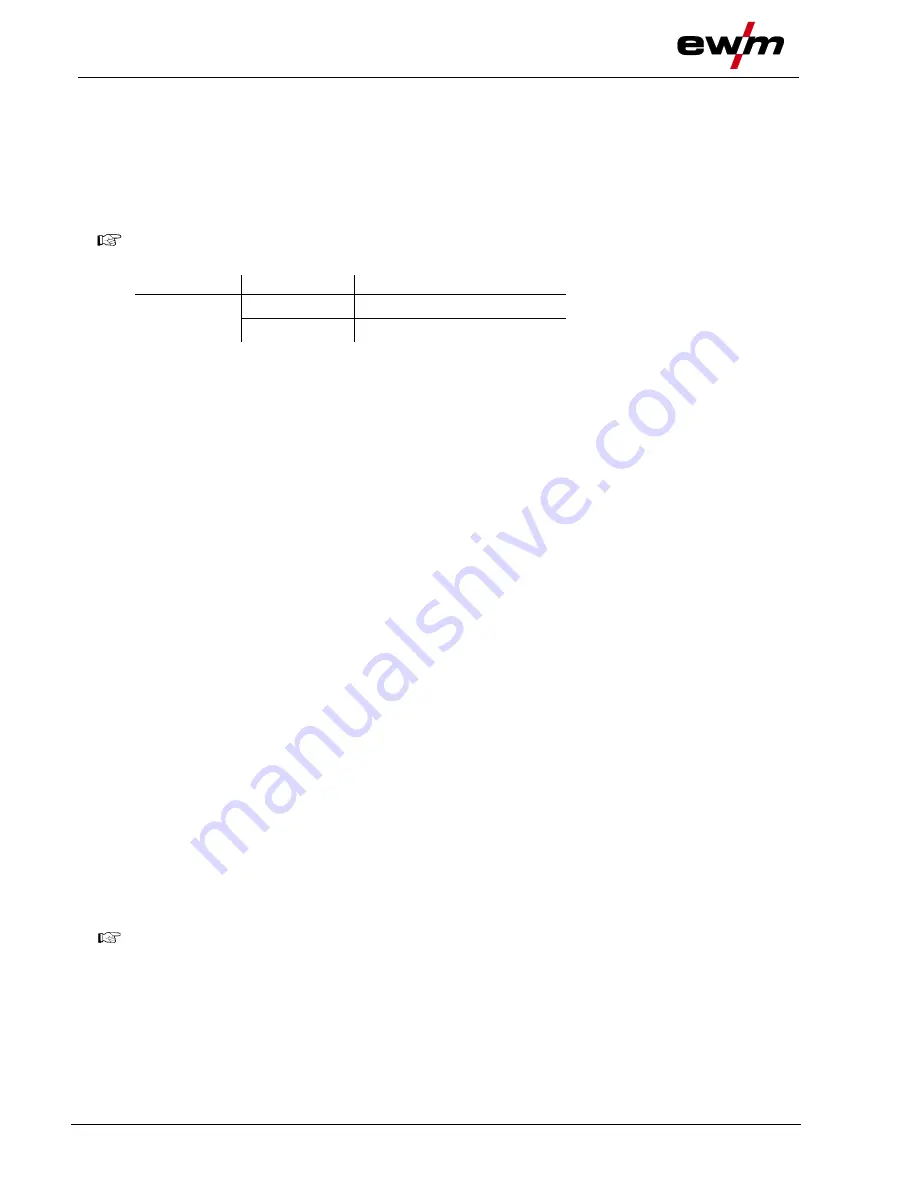
Rectifying faults
Checklist for rectifying faults
44
099-005207-EW501
18.05.2017
7
Rectifying faults
All products are subject to rigorous production checks and final checks. If, despite this, something fails to
work at any time, please check the product using the following flowchart. If none of the fault rectification
procedures described leads to the correct functioning of the product, please inform your authorised
dealer.
7.1
Checklist for rectifying faults
The correct machine equipment for the material and process gas in use is a fundamental
requirement for perfect operation!
Legend
Symbol
Description
Fault/Cause
Remedy
Wire feed problems
Contact tip blocked
Clean, spray with anti-spatter spray and replace if necessary
Setting the spool brake
> see 5.1.8.5 chapter
Check settings and correct if necessary
Setting pressure units
> see 5.1.8.4 chapter
Check settings and correct if necessary
Worn wire rolls
Check and replace if necessary
Wire feed motor without supply voltage (automatic cutout triggered by overloading)
Reset triggered fuse (rear of the power source) by pressing the key button
Kinked hose packages
Extend and lay out the torch hose package
Wire guide core or spiral is dirty or worn
Clean core or spiral; replace kinked or worn cores
Functional errors
All machine control signal lights are illuminated after switching on
No machine control signal light is illuminated after switching on
No welding power
Phase failure > check mains connection (fuses)
Several parameters cannot be set (machines with access block)
Entry level is blocked, disable access lock
Connection problems
Make control lead connections and check that they are fitted correctly.
Loose welding current connections
Tighten power connections on the torch and/or on the workpiece
Tighten contact tip correctly
7.2
Check the machine type setting
After switching on, the machine type that has been set is displayed for a short time, denoted as
"tyP".
If the machine type displayed does not match the machine, you have to correct this setting.