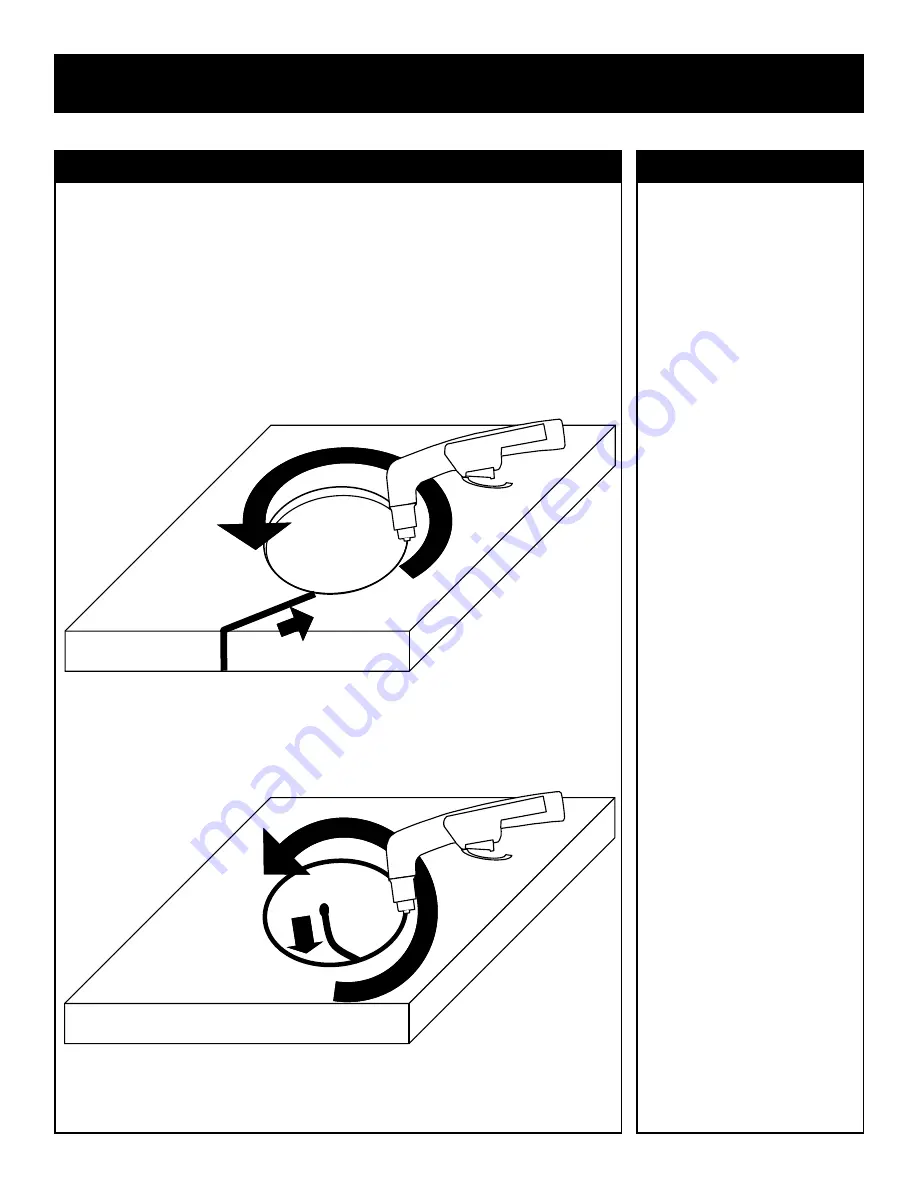
39
How Do I Use a Lead
-
in?
When cutting an object, particularly a pattern shape, where the torch must pierce or re
-
fire in
-
line at an
intersection of a cut, a lead
-
in cut should be employed. A lead
-
in is a cut that is made in the disposable
part (also known as a drop) of the object to
“
lead
”
into the main part of the cut so that the destructive
force of the arc is not directed into the desirable side of the cut itself. Also, all plasma cutters exhibit
some angularity or bevel in the cut which is greater on one side than the other. Keep this in mind (and
the direction you cut) when cutting an object to size so that too much metal is not accidentally removed
and the object can be finished to the proper size.
Component Identification and Explanation
AN EXAMPLE OF CUTTING A LEAD
-
IN WHEN CUTTING OUT A DISK SHAPED OBJECT
AN EXAMPLE OF CUTTING A LEAD
-
IN WHEN CUTTING HOLE IN AN OBJECT
What is Kerf?
When you make a cut, a certain amount
of material is removed from the cut.
This is known as the kerf. In plasma
cutting, knowing the width of the kerf is
important to making accurate cuts. A
typical kerf width from a plasma cutter
will range from
.045”
to
.090”.
The actu-
al width of the kerf is affected by the
orifice diameter in the consumable tip
and by the cut height of the torch, and to
some extent the thickness of the metal.
Of course the best way to determine kerf
width is to make a test cut and measure
it. But if you are trying to achieve a nar-
row kerf width in thick plate metal, you
will be limited by the fact that you will
need a larger orifice to support the
greater amperage needed to make a
clean cut. Of course, you should always
match the Amperage range to the orifice
diameter. Lowering Amperage too low
with a large consumable will result in arc
instability and sputtering. A higher
amperage consumable has a wider ori-
fice width to support the increase in the
Amperage. If the consumable size isn
’
t
increased, the higher Amperage arc will
quickly
“
blow
”
its way to a wider orifice,
which will lead to instability in the arc
and a decrease in cut capacity since the
hole is usually oblong instead of round
at that point. Going with a larger diame-
ter orifice on sheet metal means that
while the cut can be performed more
quickly, the kerf tolerance must be in-
creased and figured into the cut plans.
Cutting to slowly with a larger diameter
consumable on thin metals will possibly
yield an irregular kerf width, and
“
melt
back
”,
where the metal and the dross
melt back and close over the area just
cut. If you have no choice but to cut thin
material with a wider consumable,
Содержание PowerPro 164Si
Страница 46: ...46...