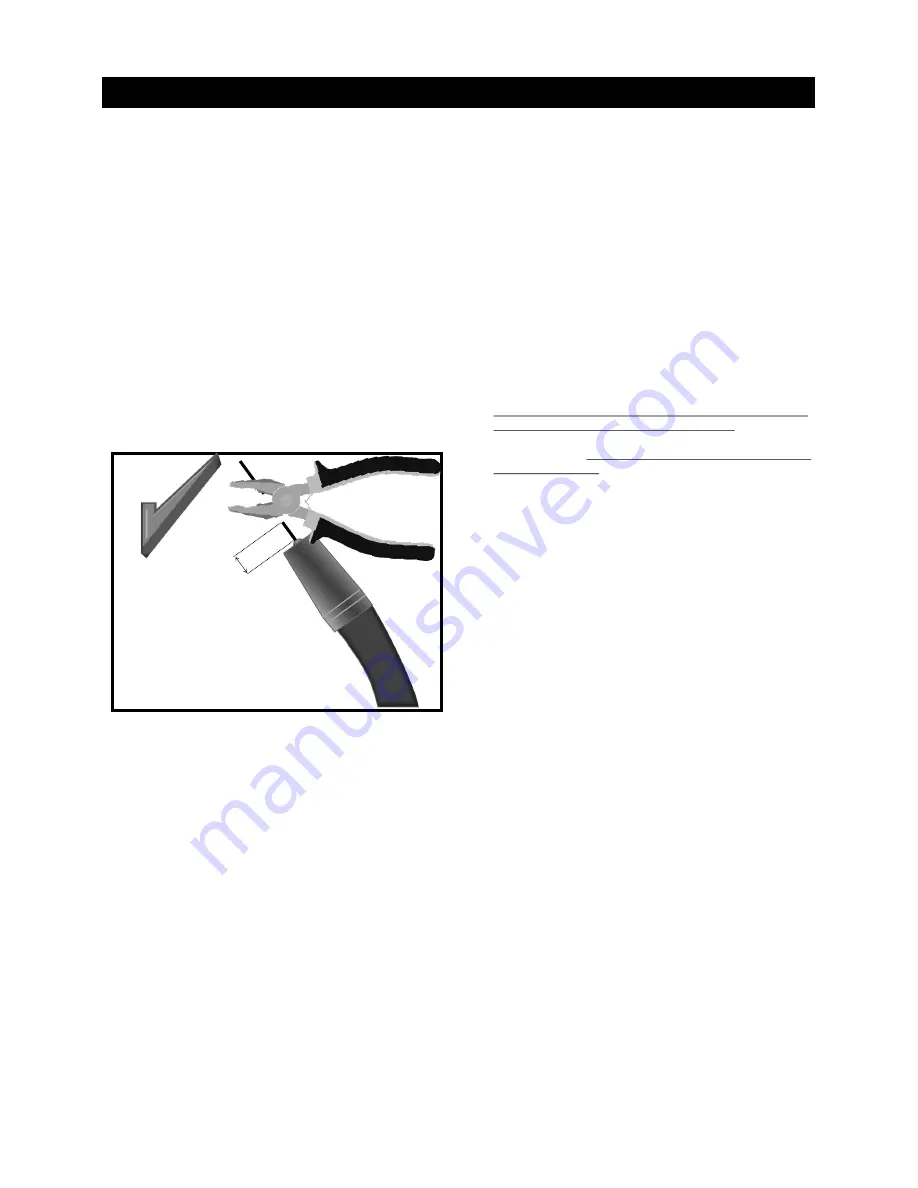
29
BASIC MIG OPERATION
If the burn back control is set too long it can cause the wire to burn
back into the tip itself and welding of the wire to the tip. Begin with
setting the unit for a little less than a quarter second. If the burn
back control is set correctly, it will leave about
1/4”
-
3/8”
wire stick-
ing out beyond the contact tip. If a large ball develops on the end
of the wire, reduce the burn back time so that it creates a balance
between ball size and stick
-
out. The short amount of post flow that
is built into the programming of the Power i
-
MIG helps shield while
the wire is burning back. This helps control balling and prevents
oxidation during burn back. This is a unique feature that is not
found in many welders with burn back control. Burnback control
without post flow can cause erratic restarts due to the oxidized or
over
-
balled wire tip.
Even with the burn back control properly adjusted, due to operator
error, an occasional quick trim of the wire may be necessary for
best arc starts. But overall, when used in a production setting or in
a fabrication shop, the burn back control can save on labor and
aggravation.
Starting the Arc and Welding.
Starting the arc is a relatively simple process. Before beginning,
the wire should initially be trimmed to between 1/4 to
3/8”.
Once
the wire is trimmed, the gun should be firmly grasped to prevent a
phenomenon often referred to as
“
machine gunning
”.
A light
grasp, especially at start, can cause the arc to stutter as the wire
pushes back on the gun, lengthening the wire stick
-
out and creating
an irregular start and porous weld.
The end of the wire should be positioned just barely above the
metal when the trigger is pulled for the cleanest start. This will
position the end of the contact tip about
1/2”
above the weld. The
gun should be in the vertical position, with no more than 5 degrees
lean in either side to side direction. Holding the wire too far off
from the metal will result in rough starting and too long of wire stick
out.
Once the arc has been established, the gun can then either be
pushed or pulled in the direction of the weld. In either case, the
gun nozzle should be positioned directly over the weld without
angling the wire to one side or the other of the weld as already
mentioned. The gun should have no more than 15 degrees lean
pointed into (push) or pointed away from (pull) the direction of
travel. In most cases a push motion is desired. However, a lot of
texts offer conflicting information on whether to push or to pull the
gun. In reality, both are correct if used correctly and with each
having particular strength and weakness. Either one done with too
much gun angle will result in undesirable results. Most open
-
minded people who are well versed in MIG quickly develop a
sense of when to push and when to pull the gun. Even for novic-
es, a sense of when to push and pull the gun comes quickly with a
little practice. Pushing can result in shallower penetration but the
molten puddle is easier to see and the arc sits easily on the leading
edge. It will usually leave a aesthetically pleasing bead. However,
be careful to prevent the gun from leaning toward or away from the
direction of travel too much as spatter will increase and shielding
gas flow may become turbulent, creating porosity in the weld.
Pulling will result in deeper penetration, but can result in a narrow
bead without much side fusion. It also can leave an undesirable
humped appearance if not done correctly or if travel is too slow.
Whenever MIG welding with Aluminum, whether with the standard
MIG gun or the Spool gun ALWAYS push the gun.
During Pulse
Welding, a Push angle is recommended wherever possible, regard-
less of metal type.
If using Flux Core, a dragging motion is almost
always recommended.
Weaving (oscillating the torch from side to side in one pattern or
the other), particularly a MIG bead, is a topic of controversy as
much as whether to push or pull the MIG gun. Stringer beads are
often best for novice welders. Stringers are simply straight beads
that move forward with little or no side to side travel or oscillation.
These will offer the soundest welds for a beginner. Stringer welds
leave little or no room for contaminates to enter the weld and are
the fastest to produce without creating an opportunity for cold lap.
Moving too quickly however with a stringer can create undercut
which will weaken the weld. The best policy is to move a slow
steady speed, making sure the sides of the weld are filled. If under-
cut is present, it is either from too much voltage or moving before
the wire has time to fill the area the arc has melted.
Think of weaving as a method of
“
sewing
”
the metal together. If
weaving is of interest to you, start with the basic weave pattern.
Simple weaves using one variation or the other of a cursive
“
e
”
motion are best to begin with. Other weave patterns can be used
of course. C
’
s, V
’
S, U
’
s , Triangles and many more weave patterns
can be used depending upon the application. Weaves are em-
ployed for a number of reasons. Weaves are often considered to
have a more pleasing appearance and can help bridge gaps where
fit up is a problem. A weave is also frequently used to manage heat
build up. For example: when welding vertically weaves are almost
always used to prevent the molten metal from sagging due to the
force of gravity. The major drawback of weaving is that it introduc-
es a greater possibility of getting inclusions and other forms of
contamination in the weld. Properly done weaving is a valuable
tool, but it must be practiced before employing it in any structural
or critical application.
Metal Cleaning.
MIG welding requires a well prepped surface to obtain a sound
weld. The removal of paint, rust mill scale, or other contaminate
such as grease should be done before welding. Stick welding is
more forgiving of rust and mill scale, but when MIG welding, con-
taminates will result in porosity and inclusions in the weld, weaken-
ing it. A grinder will usually prep the metal sufficiently to remove
oxidation and paint. However, to remove grease, a degreaser such
as acetone should be used. Do not use any degreaser such a brake
Section 2 Setup Guide
1/4”
-
3/8”
(6mm–
9mm)
Содержание Power i-MIG 353DPi
Страница 47: ...47...