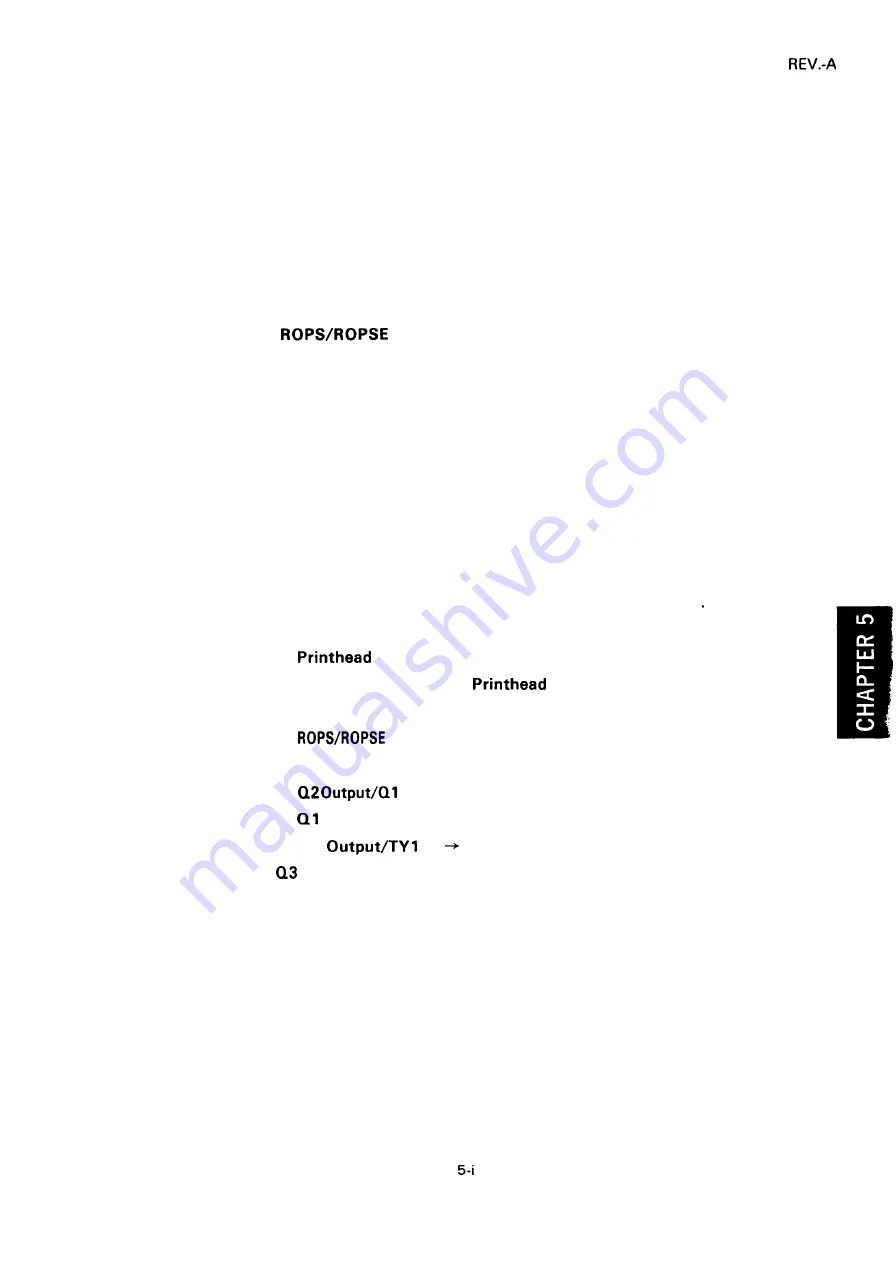
CHAPTER 5
TROUBLESHOOTING
5 . 1 G E N E R A L . . . . . . . . . . . . . . . . . . . . . . . . . . . . . . . . . . . . . . . . . . . . . . . . . . . . . . . . . . . . . . . . . . . . . . . . . . . . . . . . . . . . . . . . . . . . . . . .
5-1
5.1.1 Diagnostic Tools . . . . . . . . . . . . . . . . . . . . . . . . . . . . . . . . . . . . . . . . . . . . . . . . . . . . . . . . . . . . . . . . . . . . . . .5 4
5.1.1.1 System Outline . . . . . . . . . . . . . . . . . . . . . . . . . . . . . . . . . . . . . . . . . . . . . . . . . . . . . . . . . .5 4
5.2 UNIT REPLACEMENT . . . . . . . . . . . . . . . . . . . . . . . . . . . . . . . . . . . . . . . . . . . . . . . . . . . . . . . . . . . . . . . . . . . . . . . . .5-6
5.3 UNIT REPAIR . . . . . . . . . . . . . . . . . . . . . . . . . . . . . . . . . . . . . . . . . . . . . . . . . . . . . . . . . . . . . . . . . . . . . . . . . . . . . . . . . . . . . . . . .
5-17
5.3.1
Board . . . . . . . . . . . . . . . . . . . . . . . . . . . . . . . . . . . . . . . . . . . . . . . . . . . . . . . . . . . . . . .5-17
5.3.2 ROMA Board . . . . . . . . . . . . . . . . . . . . . . . . . . . . . . . . . . . . . . . . . . . . . . . . . . . . . . . . . . . . . . . . . . . . . . . . . . . . . .
5-23
5.3.3 Model-5560 Printer Mechanism . . . . . . . . . . . . . . . . . . . . . . . . . . . . . . . . . . . . . . . . .5-24
LIST OF FIGURES
Figure 5-1.
Troubleshooting Procedure . . . . . . . . . . . . . . . . . . . . . . . . . . . . . . . . . . . . . . . . . . . . . . . .5-1
Figure 5-2.
Extension Cable Connections . . . . . . . . . . . . . . . . . . . . . . . . . . . . . . . . . . . . . . . . . . .5-3
Figure 5-3.
Printer Diagnostic System . . . . . . . . . . . . . . . . . . . . . . . . . . . . . . . . . . . . . . . . . . . . . . . . 5-4
Figure 5-4.
RS-232C l/F Cable Circuit . . . . . . . . . . . . . . . . . . . . . . . . . . . . . . . . . . . . . . . . . . . . . . . . .5-5
Figure 5-5.
Connectors F and R Wiring . . . . . . . . . . . . . . . . . . . . . . . . . . 5-16
Figure 5-6.
Relationship Between
Temperature and
Thermistor Resistance . . . . . . . . . . . . . . . . . . . . . . . . . . . . . . . . . . . . . . . . . . . . . . . . . . . . . . . .5-16
Figure 5-7.
Board Block Diagram . . . . . . . . . . . . . . . . . . . . . . . . . . . . . . 5-17
Figure 5-8.
AC Connector for Measuring Instruments .................. 5-1 7
Figure 5-9.
Input Voltage Waveforms . . . . . . . . . . . . . . . . . . . 5-20
Figure 5-10.
Input/Output Voltage Waveforms . . . . . . . . . . . . . . . . . . . . . . . . . . 5-20
Figure 5-11. DB1
off
On Voltage Waveforms . . . . . . . 5-20
Figure 5-12.
Input/Output Voltage Waveforms . . . . . . . . . . . . . . . . . . . . . . . . . . 5-21
Figure 5-13. IC2 Oscillation/Output Voltage Waveforms . . . . . . . . . . . . . . . 5-21
Содержание LQ-2550
Страница 1: ...L Q 2 5 5 0 TECHNICAL MANUAL EPSON ...
Страница 215: ...REV A EEEl n R O M A B O A R D m CJ P R I N T E R MECHAN SM Figure 5 2 Extension Cable Connections 5 3 ...
Страница 240: ...REV A P r cl Figure 6 3 LQ 2550 Lubrication and Adhesive Application Points Diagram 2 6 3 ...
Страница 241: ...REV A 7 i_ Figure 6 4 LQ 2550 Lubrication and Adhesive Application Points Diagram 3 6 4 ...
Страница 252: ...REV A I 1 I 7 v m o m x b Figure A 6 PPD781OHG Block Diagram A 7 ...
Страница 294: ...REV A I A 3 D r a w i n g s UNIT Y4S620200000 FI 6 3A 2SV rJl 1 T T 1 T I n b 0 e l ml Component Layout A 49 ...
Страница 296: ...REV A A h 0s am 1 I I I I 1 I I 1 1 It m I I r u n 1 1 5 Q Lo O 6xm Figure A 49 ROPS Board A 5 1 Circuit Diagram ...
Страница 297: ...REV A 1 L I Irl N I i t 1 I I x Figure A 50 ROPSE Board Circuit Diagram A 52 ...
Страница 301: ...Figure A 57 Model 5560 Exploded Diagram 2 2 Figure A 58 Model 5560 Push Tractor Unit Exploded Diagram REV A A 59 ...