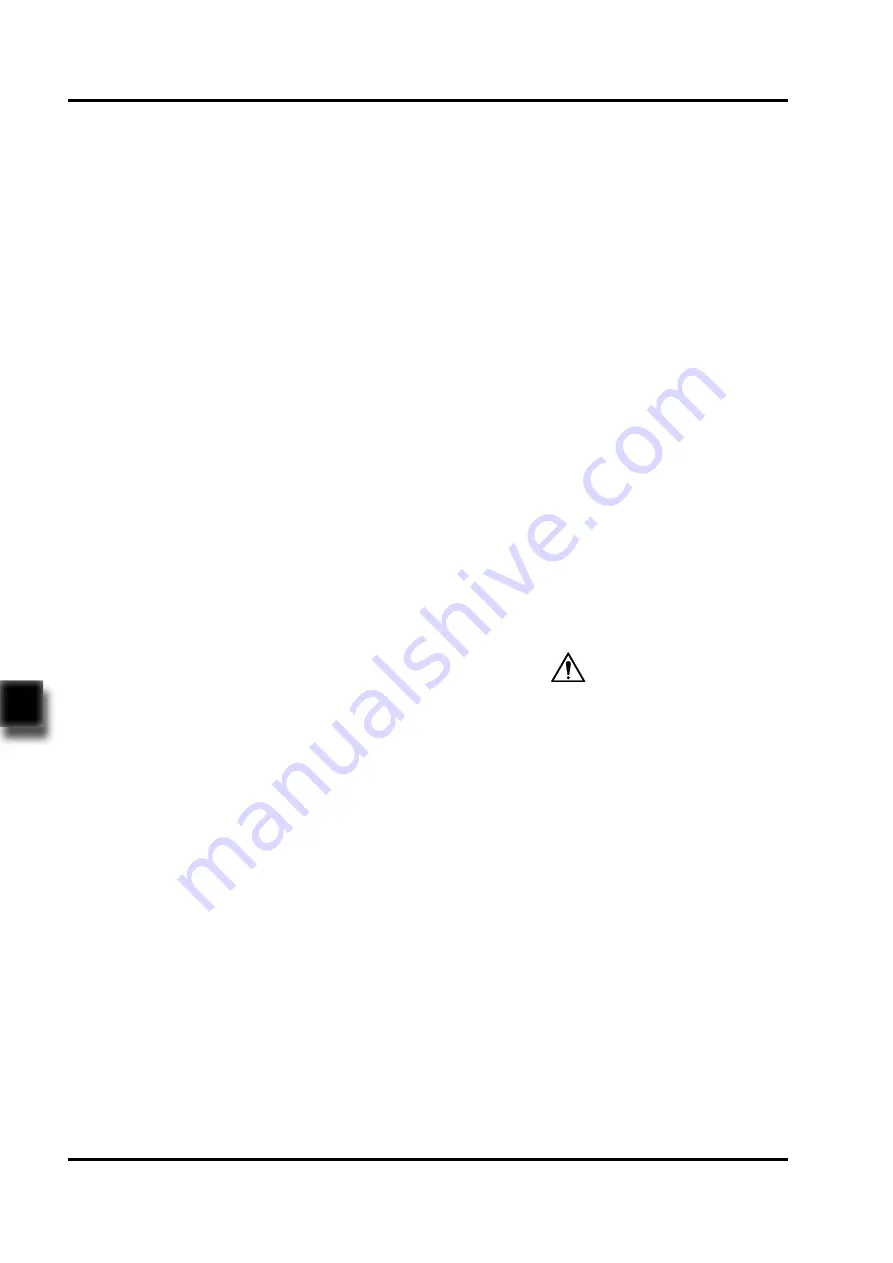
82
REV. 05/2020
HYDRAULIC SYSTEM
7
-
-
-
-
-
7.7 Tilt Cylinder
7.7.1 Cylinder Removal Precautions
Before removing the cylinder, be sure to reli-
eve the hydraulic circuit first, which is to lower
the lifting mast to the bottom. Otherwise,
when removing the tubing connected with the
cylinder, the pressured hydraulic oil within
the circuit may be sprayed out at high speed
along with the tubing, and there is risk of
causing personal injury.
Turn off the power source, so that the entire
hydraulic system will stop functioning, then
the connecting tubing can be loosened; in
order to avoid the residual pressure within the
circuit, the tubing joint should be loosened
slowly, loosen the joint by half and shake the
tubing to see if there is overflow of pressured
oil, and then go on with the removal;
Cylinder is the powered actuator in hydraulic
system. Therefore, before removing the
cylinder from the equipment, the connection
part must be supported with appropriate
supporting to avoid personal injury or damage
to the equipment;
Cylinder is the powered actuator in hydraulic
system. Therefore, before removing the
cylinder from the equipment, the connection
part must be supported with appropriate
supporting to avoid personal injury or damage
to the equipment;
Upon disassembly of the cylinder, you should
know the main structure of the cylinder to
avoid sightless removal. Due to the different
size, structure, purpose of use of the
cylinders, the sequences and methods used
for removal are also different;
When removing each part, do not hammer
forcefully, it such case cannot be avoided,
please lay a copper rod to avoid damage
to the parts; special tools must be used for
the parts having such requirements, do not
hammer forcefully or pry. Fine pitch threaded
cylinder cap, after being shaken loose,
loosen it with cylinder wrench with even force,
copper rod can be used to hammer the part
that cannot easily deform, do avoid violent
shocks.
-
-
-
Upon removal, the damage to cylinder
threads, oil port threads, cylinder cap threads,
piston rod surface and inner cylinder wall
should be prevented.
In order to prevent piston rod from bending or
deformation, support it wooden block when
placing.
When removing seals, the use of sharp
tools should be avoided, so as not to stab
the seals. For the seals that are difficult to
remove, soak them with boiled water, remove
them when getting softened.
Before removing, try to create conditions
to prevent the cylinder parts from being
contaminated by the surrounding dust and
impurities. For example, try to disassemble
the equipment in a clean environment; after
the disassembly, all parts should be covered
with plastic, do not cover with cotton cloth or
other cloth used during operation;
For the cylinder which is found with internal
or external leakage during use, if the piston
rod or cylinder tube is not scratched, such
case may be due to wear or aged seals.
When the seals need to be replaced, replace
with the complete set of seals in the cylinder
repair kit.
-
Pay special attention to the cylinder tube,
piston rod and other moving parts for bumps
and scratches. If only minor damage, sand
the edge point around the damaged part with
fine stone and then polish the part smooth
with metallographic sandpaper.
CAUTION
Содержание CPD30L1-B
Страница 1: ...Service Manual Electric Forklift Truck CPD30 35L1 B CPD30 35L1 S ...
Страница 2: ...Service Manual Electric Forklift Truck CPD30 35L1 B CPD30 35L1 S ...
Страница 13: ...1 1 1 INFORMATION SPECIFICATIONS ...
Страница 14: ...2 NOTE ...
Страница 20: ...REV 05 2020 INFORMATION SPECIFICATIONS 1 8 ...
Страница 21: ...9 2 2 MAINTENANCE ...
Страница 22: ...10 NOTE ...
Страница 31: ...19 3 3 STRUCTURE FUNCTIONS ...
Страница 32: ...20 NOTE ...
Страница 39: ...27 4 4 CHASSIS SYSTEM ...
Страница 40: ...28 NOTE ...
Страница 46: ...34 REV 05 2020 CHASSIS SYSTEM 4 ...
Страница 47: ...35 5 5 DRIVE SYSTEM ...
Страница 48: ...36 NOTE ...
Страница 49: ...37 REV 05 2020 DRIVE SYSTEM 5 Drive System No Name 1 Drive Wheel 2 Gearbox 3 Drive Motor ...
Страница 55: ...43 REV 05 2020 DRIVE SYSTEM 5 For CPD30 35L1 S see Fig3131 20012SM ...
Страница 61: ...49 6 6 OPERATING SYSTEM ...
Страница 62: ...50 NOTE ...
Страница 68: ...56 REV 05 2020 OPERATING SYSTEM 6 For CPD30 35L1 S Fig3131 30008SM ...
Страница 80: ...68 REV 05 2020 OPERATING SYSTEM 6 ...
Страница 81: ...69 7 7 HYDRAULIC SYSTEM ...
Страница 82: ...70 NOTE ...
Страница 84: ...72 REV 05 2020 HYDRAULIC SYSTEM 7 7 1 1 Hydraulic Schematic Diagram ...
Страница 89: ...77 REV 05 2020 HYDRAULIC SYSTEM 7 ...
Страница 101: ...89 8 8 STEERING SYSTEM ...
Страница 102: ...90 NOTE ...
Страница 103: ...REV 05 2020 STEERING SYSYTEM 8 91 Steering System No Name 1 Steering Wheel 2 Displacement Sensor 3 Steering Bridge ...
Страница 107: ...REV 05 2020 STEERING SYSYTEM 8 95 ...
Страница 109: ...97 9 9 ELECTRICAL SYSTEM ...
Страница 110: ...98 NOTE ...
Страница 183: ...REV 05 2020 ELECTRICAL SYSTEM 9 171 9 13 Electrical Schematic Diagrams CPD30 35L1 B ...
Страница 185: ...REV 05 2020 ELECTRICAL SYSTEM 9 173 9 15 Wiring Harness and Connectors CPD30 35L1 B ...
Страница 186: ...REV 05 2020 ELECTRICAL SYSTEM 9 174 9 16 Wiring Harness and Connectors CPD30 35L1 S ...
Страница 187: ...175 10 10 TROUBLESHOOTING ...
Страница 188: ...176 NOTE ...
Страница 194: ...REV 05 2020 TROUBLESHOOTING 10 182 ...
Страница 195: ...183 APPENDIX ...
Страница 196: ...184 NOTE ...
Страница 197: ...185 A A SERVICE MANUAL MAST ...
Страница 198: ...186 NOTE ...
Страница 210: ...198 REV 05 2020 SERVICE MANUAL MAST A A2 3 Mast Tubing Code Description A1 Lifting Lowering Mast Tubing ...
Страница 211: ...199 REV 05 2020 SERVICE MANUAL MAST A Code Description A3 Right Shift Mast Tubing B1 Left Shift Mast Tubing ...
Страница 213: ...201 REV 05 2020 SERVICE MANUAL MAST A ...
Страница 220: ...208 REV 05 2020 SERVICE MANUAL MAST A ...
Страница 221: ...209 REV 05 2020 SERVICE MANUAL MAST A A3 3 Mast Tubing Code Description A1 Lifting Lowering Mast Tubing ...
Страница 222: ...210 REV 05 2020 SERVICE MANUAL MAST A Code Description A3 Right Shift Mast Tubing B1 Left Shift Mast Tubing ...
Страница 226: ...214 REV 05 2020 SERVICE MANUAL MAST A ...
Страница 227: ...215 B B SERVICE MANUAL BATTERY ...
Страница 228: ...216 NOTE ...
Страница 232: ...220 C C SCHEDULE ...
Страница 233: ...221 ...
Страница 235: ......