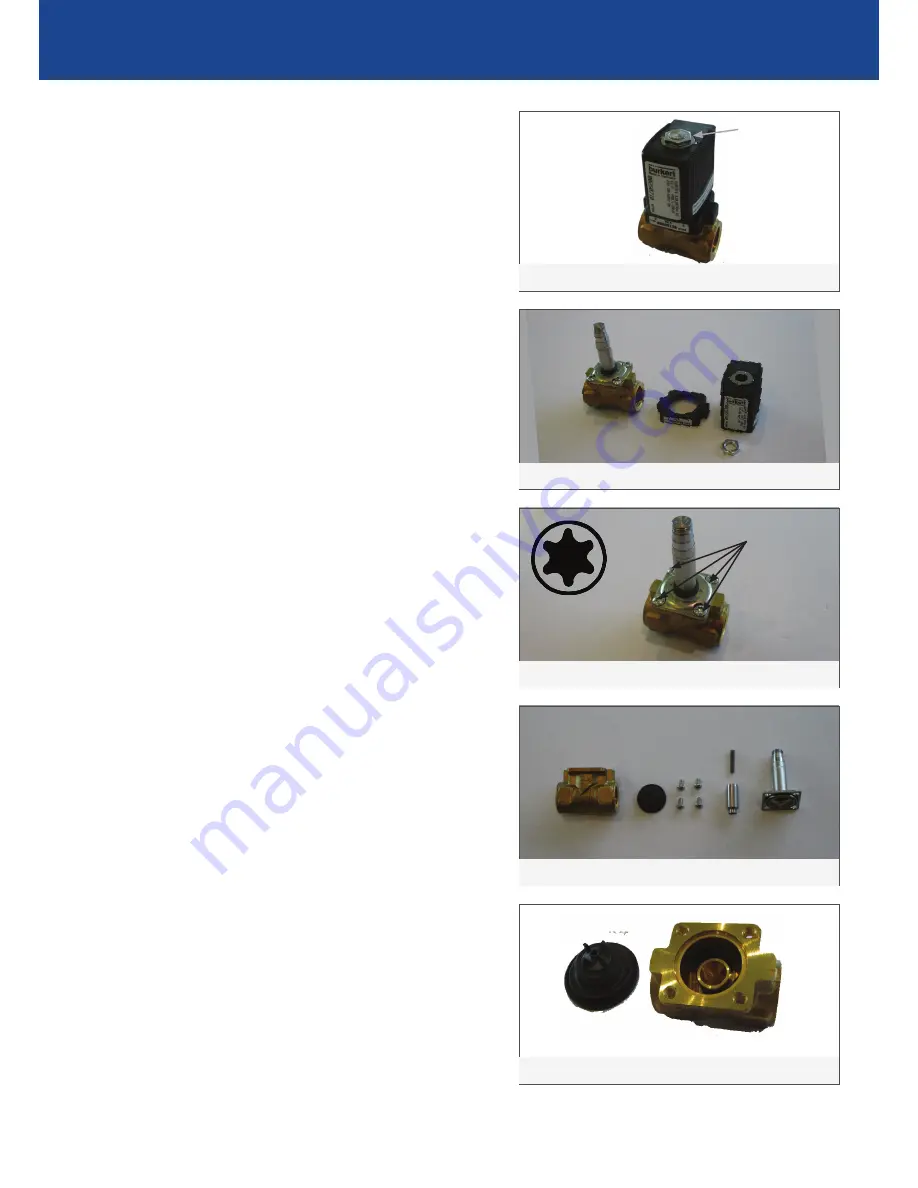
12
Call 1300 369 273
www.enware.com.au
SERVICE & MAINTENANCE
SOLENOID MAINTENANCE
For long periods of non-use, a minimum activation of
1-2 times per day is recommended.
High frequency of use and high water supply pressures
reduce the service life of a solenoid.
If the solenoid is not working correctly or leaking, go
through the following steps to service the solenoid.
The most common cause of solenoid malfunction is
debris being caught inside, in which case the solenoid
needs to be dismantled and cleaned. Service kits
including replacement diaphragms are available.
To Access the Solenoid Valve
1. Turn water supply off and activate the sensor to
drain as much water from the fitting as possible. Turn
power off to the sensor.
2. In most cases it is easier to remove the solenoid
valve completely from the installation to service it.
Remove the electrical connectors from the solenoid
terminals, undo the water connections on both the
water inlet and outlet of the solenoid, and remove
the solenoid.
3. The solenoid can be disassembled and checked for
debris or damage to the diaphragm. Refer to the
instructions below for “Servicing the Solenoid”. Take
note of the location of the components so that it can
be reassembled in the correct order.
4. Service or replace the solenoid and re-install into
the line. Push the cable connectors back onto the
solenoid terminals
5. Turn power on and test tap.
Servicing the Solenoid
Tools required: Spanner, T20 Torx Bit
1. Remove the nut located on top of the solenoid.
SEE IMAGE 8
2. Remove the black coil body and plastic cover from
the core tube. SEE IMAGE 9
3. Using a T20 Torx screw driver (star bit), remove the
4 Torx screws that are holding the core tube. Use the
correct size tool and take care not to round the screws
heads. Keeping in mind that the plunger inside the
core tube is spring loaded, dismantle the valve with
care. Take note of the order of parts assembled. SEE
IMAGES 10, 11, 12
4. Check seat and diaphragm for debris or any damage.
SEE IMAGE 12
57.5
10
100
26
130
200
180
110
85
22
33
16
55
10
5 TYP
DEPTH)
SPACE FOR
CIRCUIT BOARD
(REQUIRES 30mm
COVER PLATE
OUTLINE
IMAGE 9
57.5
10
100
26
130
200
180
110
85
22
33
16
55
10
5 TYP
DEPTH)
SPACE FOR
CIRCUIT BOARD
(REQUIRES 30mm
COVER PLATE
OUTLINE
IMAGE 8
NUT
57.5
10
100
26
130
200
180
110
85
22
33
16
55
10
5 TYP
DEPTH)
SPACE FOR
CIRCUIT BOARD
(REQUIRES 30mm
COVER PLATE
OUTLINE
IMAGE 10
T20 TORX
4 X TORX
(T20)
SCREWS
57.5
10
100
26
130
200
180
110
85
22
33
16
55
10
5 TYP
DEPTH)
SPACE FOR
CIRCUIT BOARD
(REQUIRES 30mm
COVER PLATE
OUTLINE
IMAGE 11
57.5
10
100
26
130
200
180
110
85
22
33
16
55
10
5 TYP
DEPTH)
SPACE FOR
CIRCUIT BOARD
(REQUIRES 30mm
COVER PLATE
OUTLINE
IMAGE 12