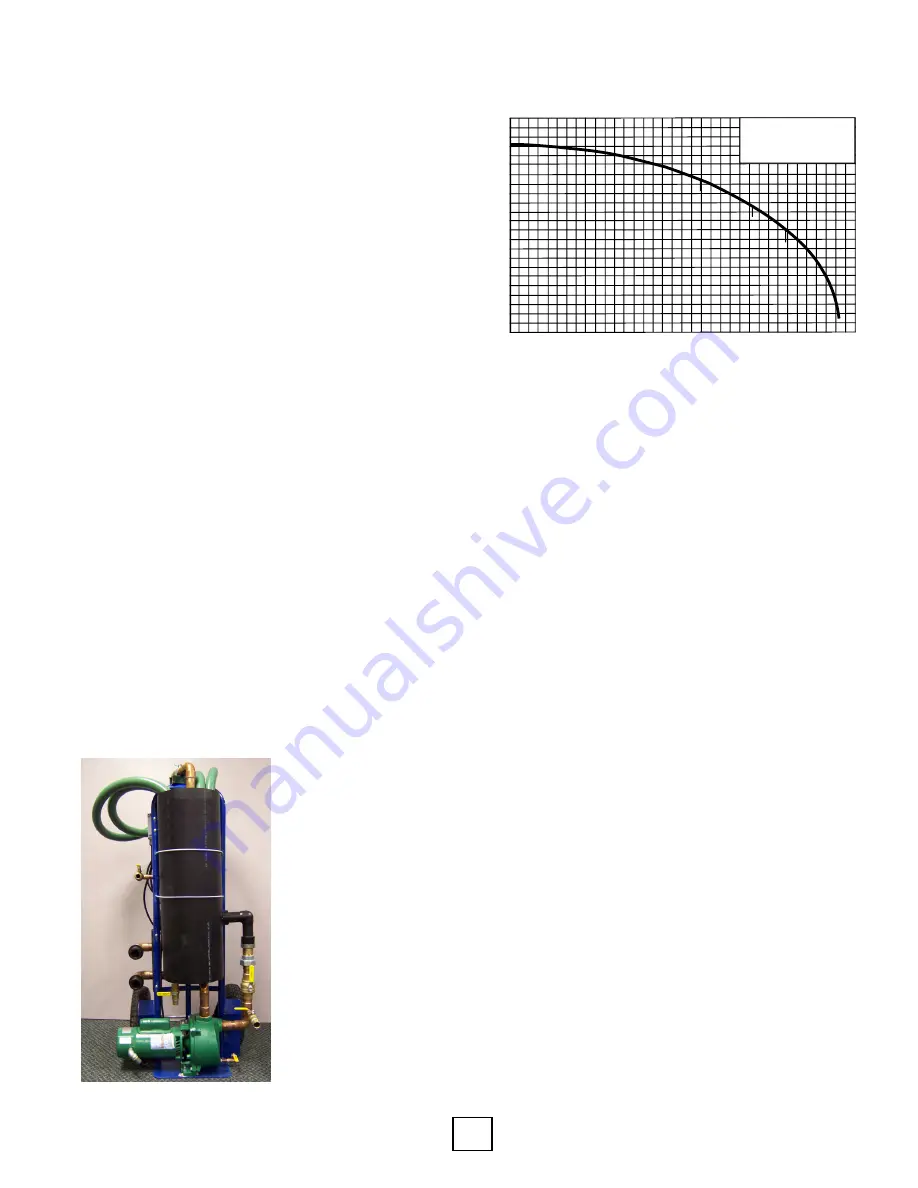
31
IOM, ZS/ZT Models
Enertech Global
Figure 10: Flush Cart Pump Curve
0 10 20 30 40 50 60 70 80 90
CAPACITY - U.S. GPM
120
110
100
90
80
70
60
50
40
30
20
10
Total H
ead in F
eet
SUCTION LIFT
25’
20’
15’
Meyers QP-15
1-1/2 HP Self-Priming
Centrifugal Pump
Step 1: Flushing the Earth Loop
• Connect flush cart hoses to flow center flush
ports using proper adapters #AGAFP.
• Connect water supply to hose connection
on return line of flush cart.
• Turn both 3-way valves on flow center to
flush ports and loop position.
• Turn on water supply (make sure water is of
proper quality).
• As the reservoir fills up, turn the pump on
and off, sucking the water level down. Do
not allow the water level to drop below
intake fitting to the pump.
• Once the water level remains above the
water outlet in the reservoir leave the pump
running continuously.
• Once the water level stays above the “T” in
the reservoir, turn off the water supply (this
also allows observation of air bubbles).
• 8. Run the pump for a minimum of 2 hours for
proper flushing and purging (depending on
system size it may take longer).
• “Dead head” the pump every so often and
watch the water level in the reservoir. Once
all the air is removed there should not be
more than a 1” to 2” drop in water level
in the reservoir. If there is more than a 2”
drop, air is still trapped in the system. This is
the only way to tell if air is still trapped in the
system.
• To dead head the pump, shut off the return
side ball valve on the flush cart. This will
provide a surge in pressure to the system
SECTION 5: UNIT PIPING INSTALLATION
Flushing & Charging a Pressurized Flow Center
The Enertech Manufacturing flush cart has been
designed to effectively and efficiently flush the
earth loop and to facilitate injecting and mixing
of the antifreeze. The single most important
element in flow center reliability is the ability to
remove all the air and debris from the loop and
to provide the proper working pressure.
Removing Debris During Flushing
Most flow center or pump failures are a result of
poor water quality or debris. Debris entering the
loop during fusion and installation can cause
noise and premature pump failure. Enertech
recommends a double flush filtering method
during purging. When purging, use a 100 mi-
cron bag filter until air bubbles are removed.
Remove the 100 micron bag, replace it with a 1
micron bag and restart the flushing.
Features of the flush cart:
Cylinder: HDPE, SDR15.5, 10” dia. (10 Gallons)
Pump: Myers High Head QP15, 1.5hp, 115V
Hose connections: Cam Lock quick connects -
1-1/2” hoses
Hand Truck: 600lb rating with pneumatic tires
Wiring: Liquid Tight metal on/off switch
Tubing: SDR11 HDPE
Connections: 2 - 3/4” connections for antifreeze
and discharge
Drain: one on the pump and the tank
Figure 9: Enertech Flush Cart
Содержание ZS.
Страница 24: ...24 Enertech Global IOM ZS ZT Models Unit Electrical Data ZS 018 042 ECM Models SECTION 4 UNIT DATA INFORMATION...
Страница 25: ...25 IOM ZS ZT Models Enertech Global Unit Electrical Data ZS 048 072 ECM Models SECTION 4 UNIT DATA INFORMATION...
Страница 26: ...26 Enertech Global IOM ZS ZT Models Unit Electrical Data ZS 018 042 PSC Models SECTION 4 UNIT DATA INFORMATION...
Страница 27: ...27 IOM ZS ZT Models Enertech Global Unit Electrical Data ZS 048 072 PSC Models SECTION 4 UNIT DATA INFORMATION...