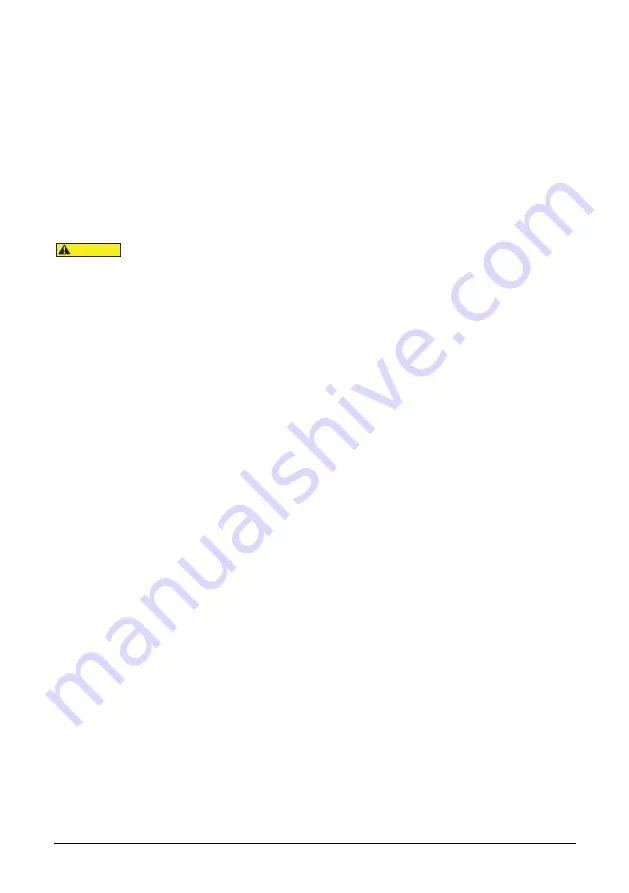
5.
Increase the hydraulic pressure
approximately
5 percent
above the “break
loose” pressure recorded in step 4. Then,
stop the pump.
6. While holding the pressure constant, turn
up (loosen) the nut at the first tensioner,
so that there is approximately a 1/8 inch
[3-4 mm] gap between the nut and the
joint surface. See Figure 17.
Note:
Dimension of gap in step 6 must not
exceed the dimension of gap in step 2.
7. Repeat step 6 at all remaining studs.
If nuts are difficult to turn, hydraulic
pressure may be increased in additional
5 percent increments. However, NEVER raise
hydraulic pressure above 21,750 psi [1500 bar].
Ensure that the load applied does not exceed
the tensile strength of the stud.
8.
Release the hydraulic pressure by
SLOWLY opening the pump pressure
release (return to tank) valve. Verify that the
oil pressure gauge indicates zero (0) psi/
bar. See Figure 18. The studs are now fully
de-tensioned.
9. Turn down the threaded pullers until the
pistons are fully retracted. Disconnect
hydraulic hoses and install a dust cap (not
shown) over each disconnected coupler.
Remove tensioners from the studs.
Note:
If the puller becomes looked on the top
face of the nut, unscrewing the nut further than
specified can cause the puller to become locked
on the top face of the nut when the tension in
the bolt is released. To release the puller the
hydraulic pressure must be re-applied and the
nut rotated via the socket until the nut seats on
the flange/joint face. Depressurise the system;
the puller should now be free to be turned, if not
repeat until it can be unscrewed.
Note:
If the puller becomes locked onto the
ram, is a situation that may only arise on studs
with fine pitches whereby unscrewing the puller
through one half turn has been insufficient and
upon releasing the hydraulic pressure (tension
in the stud) has caused the puller to become
locked on the ram.
To release the puller the hydraulic pressure
must be re-applied and the nut rotated via
the socket until the nut seats on the flange/
joint face. Depressurise the system; the puller
should now be free to be turned by hand.
CAUTION
7.4 De-tensioning Instructions - 50%
Coverage (tensioner installed on every
other stud)
IMPORTANT:
Read precautions and instructions
at beginning of Section 7.0 before beginning the
following steps. Also refer to safety information
contained in sections 2.1.
1. Assemble the tensioner(s) to the first 50%
of stud(s) to be de-tensioned and connect
the hydraulic hoses. Refer to sections 6.1
and 6.2 for additional tensioner installation
and hose connection instructions.
2. Follow steps 2 through 8 of Section 7.3 for
the first 50% of studs.
3. Move the tensioners to the second 50% of
studs.
4. Follow steps 2 through 9 of Section 7.3 for
the remaining 50% of studs. Note that the
“break loose” hydraulic pressure for the
second set of studs will likely be about the
same or slightly lower than that for the first
set.
8.0 MAINTENANCE
It is recommended that repairs and servicing
be carried out by Enerpac at intervals agreed
by Enerpac and customer. All parts will be
thoroughly inspected and replaced where
necessary, certain components (e.g. seals)
will be replaced automatically. Tensioners will
be re-assembled, pressure tested and a test
certificate issued.
Note:
All parts will have been manufactured,
inspected and tested in accordance with
Enerpac’s stringent requirements. Any parts
failing in use that are found upon Enerpac’s
inspection not to be Enerpac’s genuine spare
parts will invalidate any operative warranty or
guarantee.
The tool is of rugged construction and utilises
reliable seals. The only maintenance that may
be occasionally required is the replacement of
seals or repair of a hydraulic fitting.
14
© 2019 Enerpac, All Rights Reserved.