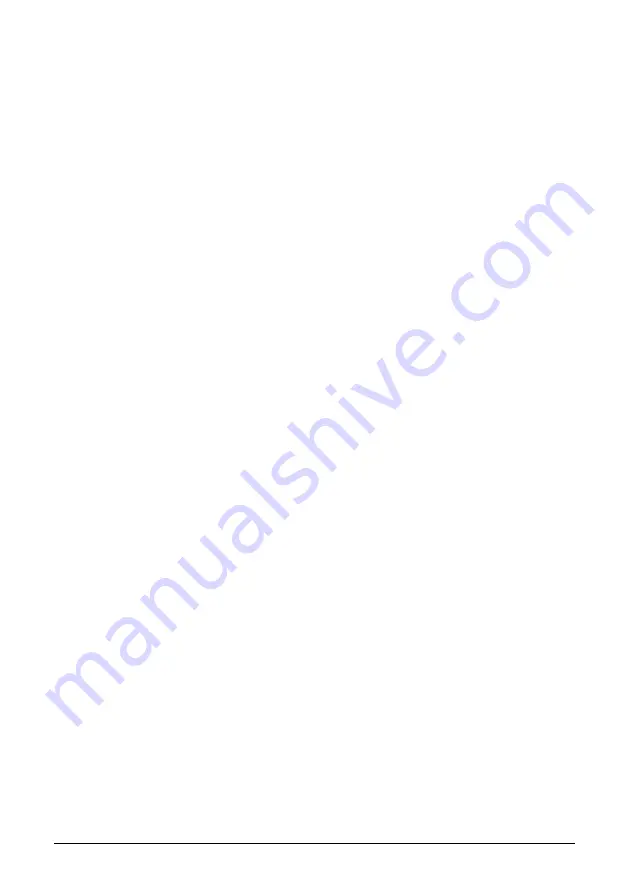
If tensioners are subject to a lot of use it is
advisable to fully strip them and clean and
inspect all components, at least once a year.
Refer to Section 8.3.
2. Bridge
Ensure that the socket is free to rotate inside
the bridge.
Ensure that the socket retaining ring is intact.
Inspect for damage and clean down with light
oil before storing.
3. Puller
Ensure that the threads are free from damage
by screwing it down a suitably sized bolt.
Clean down the puller with light oil before
storing.
4. Hoses and Ancillaries
Clean, then coat each quick disconnect coupler
in a water repellent spray such as WD40 or
similar, retracting and releasing the collars
several times. Ensure that the collars do not
seize in the retracted position. Visually inspect
the entire length of the hose for damage. Test
to maximum working pressure (ensure blanking
plugs inserted into end of coupler).
8.3 HydraMax
®
Tensioner Full Maintenance/
Servicing
It is recommended that repairs and servicing
be carried out by Enerpac at intervals agreed
by Enerpac and customer. All parts will be
thoroughly inspected, specified parts will be
non-destructively tested using MPI techniques
and replaced where necessary, certain
components (e.g. seals) will be replaced
automatically.
Tensioners will be re-assembled, pressure
tested and a test certificate issued.
Note:
All parts will have been manufactured,
inspected and tested in accordance with
Enerpac’s stringent requirements. Any parts
failing in use that are found upon Enerpac’s
inspection not to be Enerpac’s genuine spare
parts will invalidate any operative warranty or
guarantee.
Note:
It is strongly recommended that in the
event of seal failure the tensioners are returned
to Enerpac for seal replacement, however if this
is not possible then the enclosed procedure
should be followed.
8.1 Pre-Use Maintenance
Assemble the tensioner onto a suitable bolt
(see Section 6.0), check that the bolt material
is capable of taking the applied load i.e. do not
pressurise to max working pressure if the bolt
is not strong enough to withstand the full load
of the tool. Ram stroke should be minimised to
prevent the overstroke eliminator valve being
activated.
Pressurise for approximately one minute, a
pressure drop of 50 bar is acceptable during
this time.
If the tensioner passes this test, then the ram
should be reset and the tensioner is ready for
use.
If any leakage is noticed within the head
assembly, then a full strip down will be
necessary to change the seals, as described in
Section 8.4.
8.2 Post-Use Maintenance
In order to keep the equipment in good working
condition it is important that at the end of each
period of use, prior to being replaced into dry
storage, a post-use maintenance is carried out.
1. HydraMax® Tensioner
The ram should be reset and all parts should
be cleaned down, and coated with WD40 or
similar. Alternatively rinse in light oil.
Replace the dust caps on the quick disconnect
couplers to prevent the ingress of dirt.
If any leakage is noticed within the head
assembly, then a full strip down will be
necessary to change the seals, as described in
Section 8.4.
© 2019 Enerpac, All Rights Reserved.
15