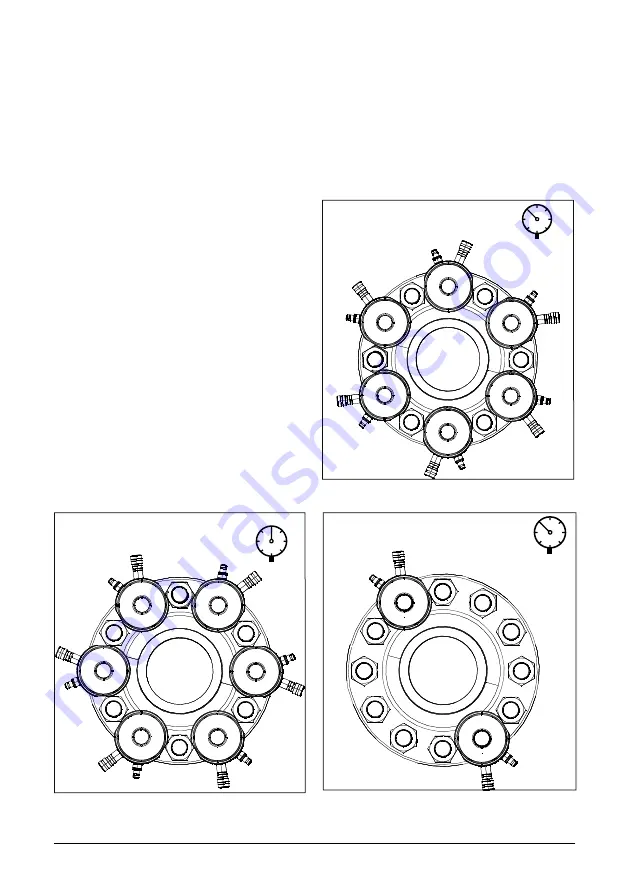
Be sure the pressure remains stable (not
increasing or decreasing). Threads may
be visible between the nut and the joint
surface at each tensioner. See Figure 7.
8. While holding the pressure constant, use
a tommy bar to turn down the first socket
and nut by hand. Continue tightening until
the nut is firmly seated against the joint
surface. See figures 8 and 9.
1
1
1
1
1
1
2
2
2
2
2
2
B
FIGURE 13, TENSIONER ARRANGEMENT, SECOND
PASS - TYPICAL (50% TENSIONER COVERAGE)
Apply Pressure “B”
(At all studs marked “2”)
FIGURE 14, RECHECKING FIRST PASS
TENSION (50% TENSIONER COVERAGE)
1
1
1
1
1
1
2
2
2
2
2
2
B
1
1
Apply Pressure “B”
(At two diametrically opposite
studs marked “1”)
1
1
1
1
1
1
2
2
2
2
2
2
A
FIGURE 12, TENSIONER ARRANGEMENT,
FIRST PASS - TYPICAL (50% TENSIONER
COVERAGE)
Apply Pressure “A”
(At all studs marked “1”)
© 2019 Enerpac, All Rights Reserved.
11
2. Alternately number each bolt “1” and “2”
for future reference.
3. Assemble the tensioner(s) to the studs
marked “1” and connect the hydraulic
hoses. See Figure 12 for typical tensioner
arrangement. Also refer to sections 6.1
and 6.2 for additional tensioner installation
and hook-up instructions.
4. Determine the “first pass” pressure “A”
value. This value must be calculated by a
qualified engineer with bolting experience.
Note:
The pressure “A” value used to tension
the bolts marked “1” is typically
higher
than
the pressure “B” value used later to tighten the
bolts marked “2”. This is to allow for additional
load losses which may occur when performing
less than 100% coverage tensioning.
5.
Operate the pump and pressurize the
tensioners up to approximately 1000 psi
[70 bar]. Check for oil leaks.
6. If no leaks are found, restart the pump
and pressurize the tensioners to the “first
pass” pressure “A” value determined in
step 4. Continually observe the tensioner
stroke and hydraulic pressure at all times
during pressurization.
7.
When the “first pass” pressure “A” is
reached, stop the pump. Recheck the oil
pressure gauge after pump has stopped.