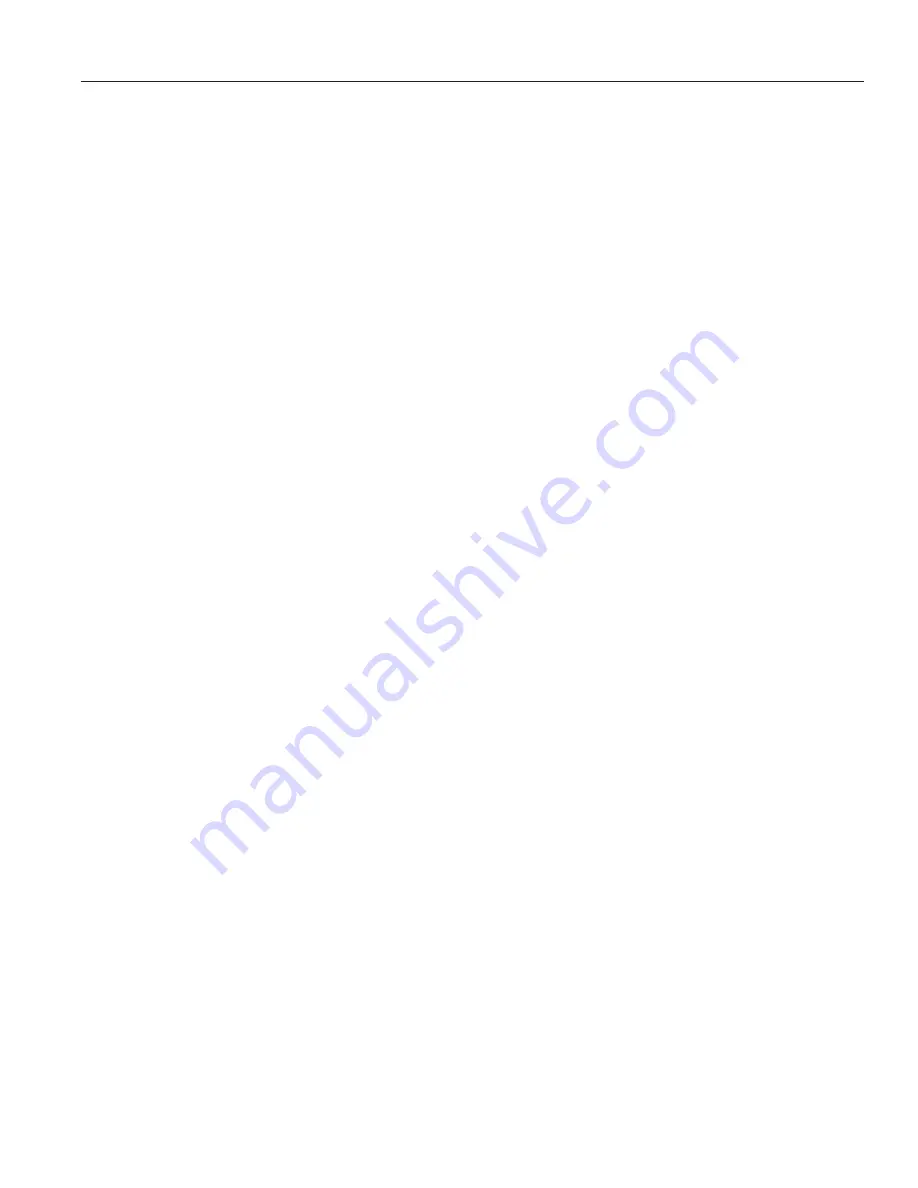
33
Hauser
Prosonic T - FMU 130, 131, 230, 231, 232
Technical Data
(Subject to change without notice)
Input Variables
Frequency
FMU 130, 230:
approx. 70 kHz;
FMU 131, 231:
approx. 55 kHz;
FMU 232: approx. 37 kHz
Pulse Frequency
0.5 to 3 Hz, depending on sensor and electronic version
Output Variables
Output Damping
0 - 255 s
(Integration time)
Load
Max. 600
W
Measuring Accuracy
Measuring Uncertainty
0.25% for max. measuring span (ideal reflection from flat surface at
68°F/20°C)
Resolution
FMU 130, 131, 230, 231 (2-wire): 0.12 in. (3 mm);
FMU 230, 231, 232 (4-wire): 0.078 in. (2 mm)
Application Conditions
Medium temperature range
-40 to +176°F (-40 to +80°C) (built-in temperature sensor)
Operating Temperature Range
-4 to +140°F (-20 to +60°C)
Storage Temperature Range
40 to +176°F (-40 to +80°C)
Operating Pressure p
abs
Sensors with process connection G 1½ and G 2: 44 psi (3 bar);
Sensor DN 100 or 4
²
: 36 psi (2.5 bar)
Climatic Class
DIN / IEC 68 T2-30 dB
Type of Protection
NEMA 6, with housing cover open; NEMA 1
Vibration Resistance
DIN IEC 68T2-6 Tab. 2.C (10 to 55 Hz)
Electromagnetic Compatibility
Interference emission according to EN 61326; apparatus of class B;
interference immunity according to EN 61326, app. A (industrial
area) and NAMUR recommendation EMV (NE 21)
Explosion Protection
FMU 130/131 (2-wire Ex): EEx ia IIC T6 (FRG: Zone 1 only)
FMU 230/231 (2-wire not Ex and 4-wire): without
FMU 232 (4-wire): Dust-Ex Zone 10 (FRG only: BVS) not with open
housing cover
Mechanical Design
Material
Housing: PBT (glass reinforced, flame-retardant)
Threaded boss and sensor: PVDF, for FMU 232: UP (unsaturated
polyester), or 1.4571 (SS316TI)
Sensor diaphragm: Stainless steel
Seals
Between threaded boss and sensor, internal: EPDM seal;
On threaded boss, external: EPDM seal
Display and Operating Elements
Display (LCD)
4-character display with segment display of current
LEDs
Red:
Indicates alarm or warning
Green:
Indicates power ON (with four-wire
versions only) and entry acknowledgment
1)
Please check with Hauser before using sensors at higher temperatures and higher pressures. When sensors are subjected
to high temperatures and pressures (with limiting conditions), it is recommended that the coupling (process connection) be tightened.