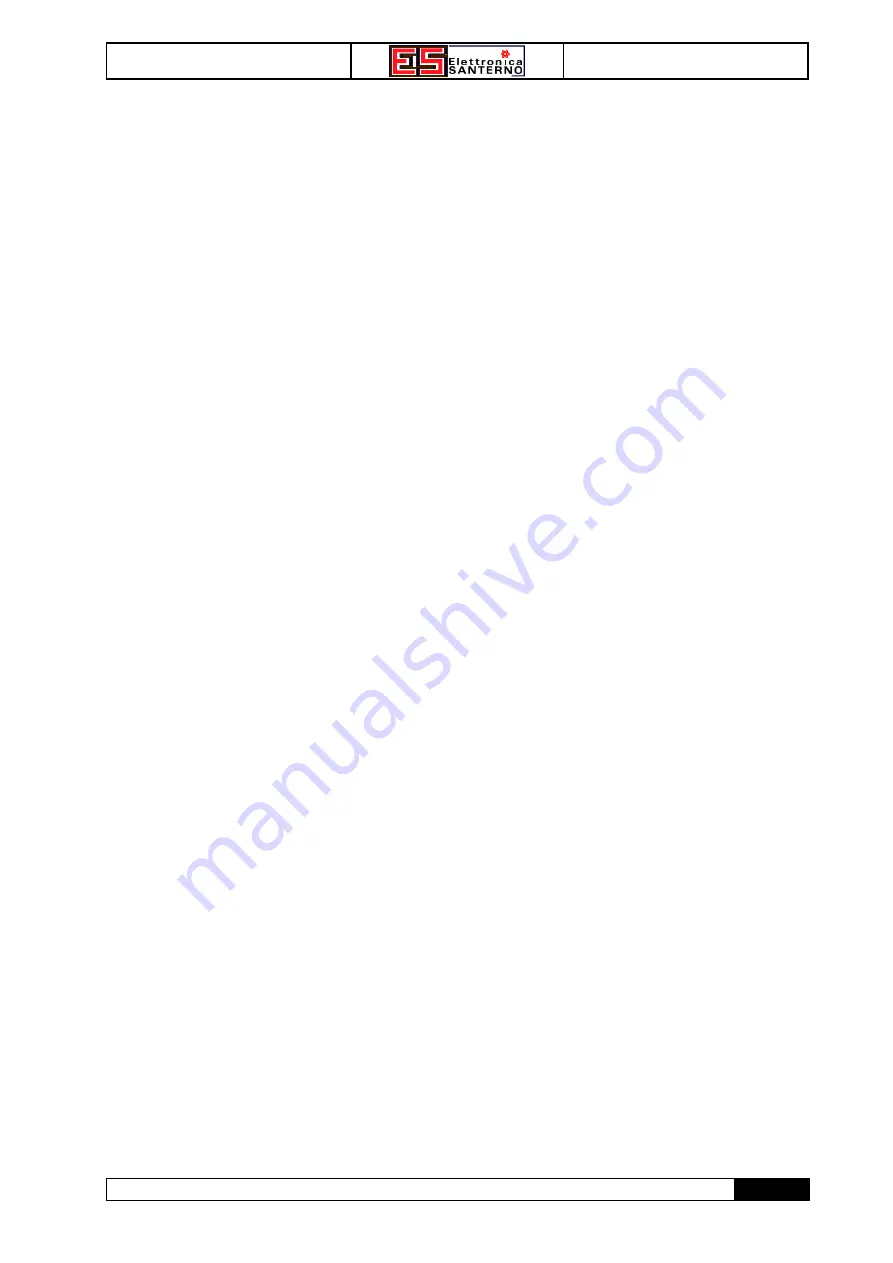
AMS90/1
APPLICATION MANUAL
15P0056B1
15/17
INSTALLATION, CALIBRATION AND MAINTENANCE
INSTALLATION, CALIBRATION AND MAINTENANCE
PRELIMINARY CONTROLS
PRELIMINARY CONTROLS
After receiving the drive, check it carefully in order to verify the presence of damages
due to transport. If so, take the necessary measures. Check that all the rating
corresponds to the application, as shown on the cover label.
If not, contact your dealer or ELETTRONICA SANTERNO.
INSTALLATION
INSTALLATION
The drive must be positioned so as to allow for air circulation in vertical direction. See
fig. 1:
External and fixing dimensions
.
When connecting the unit, comply with the following precautions:
1. Avoid positioning the wires of the tacho generator and of signals closes to the power
cables and other possible electromagnetic trouble sources. If more accuracy is
required in the control system, use shielded cables externally insulated for speed
reference and tacho generator feedback. The shield must be connected in the
shorter and more direct way to the ground, without any intermediate connection.
2. Make connections as short as possible.
3. After wiring, check if connections and solderings are correct and check the proper
positioning of jumpers and dip-switches, as regards the supply voltage and
frequency and the drive application.
4. Supply the control section at terminals 25 and 26 and check that LEDs (L1)
15V
and
(L2)
n=0
are on.
5. After supplying the field rectifier circuit at terminals 27 and 28, check the presence
of the direct voltage required for D.C. motor field supply at terminals 29 and 30.
6. Close the KM remote control switch and the KA contact (if any) connected in series
to the NO auxiliary contact of the remote control switch, and check that LED (L3)
RUN
is turned on.
7. Send the speed reference to term. 7 (or 4) and check the motor is started. If this
does not happen and the LED (L4)
LIM
turns on, check if this condition is caused by
one of the following reasons:
a)
The supply of term. 25-26 IS NOT IN PHASE with that of term. 23-24 (with closed remote control
switch, a zero alternate voltage should be present between term. 23 and 25, and term. 24 and 26).
b)
An interruption occurred in one of the extra-quick fuses FU1-2 or in the armature connection.
c)
Trimmer RV7 (
I LIM
) is fully rotated in counter-clockwise position (current limit is zero).
d)
The drive is preset for external current limit (J5
⇒
E
) and no negative voltage is applied to term. 9.
... cont.