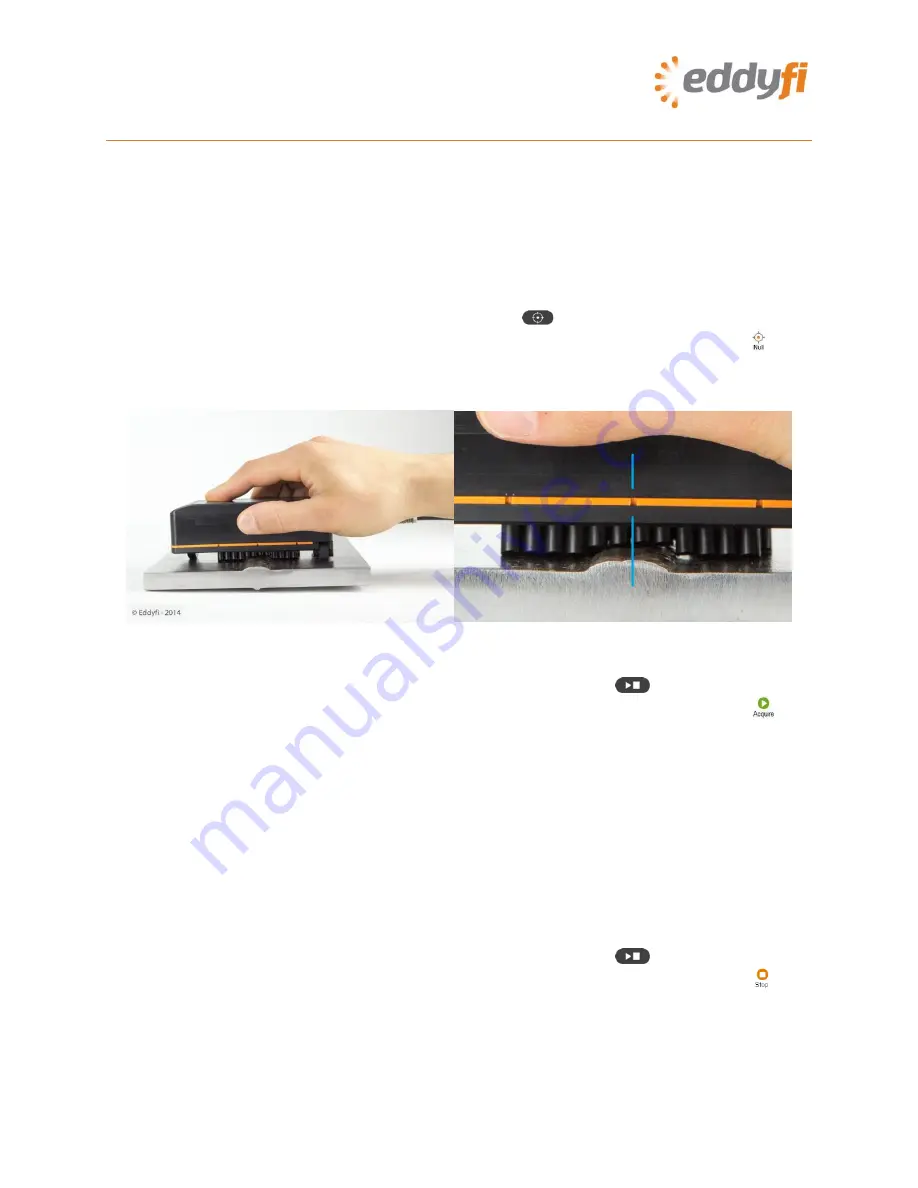
21 |
P a g e
7.
Collecting Data
1.
Position the Sharck probe on the plastic portion of Eddyfi’s normalization plate (REFPL-CAL-
SHARCK-AAL-LG).
Note
The normalization plate should be on a steady, flat surface and shall be at least 10 cm (4 in)
from any ferritic surface.
2.
Apply even pressure on the probe.
3.
On Reddy’s keypad, press the
Probe nulling
button (
).
Alternately, in the front stage view, on the
Home
or
Calibration
ribbon, tap
Null
( ).
4.
Position the probe on the part to be inspected across the weld, as illustrated. It is
recommended to have the coverage center reference mark at the weld centerline.
Figure 29 Sharck probe on carbon steel weld
5.
On Reddy’s keypad, press the
Start/Stop acquisition
button (
).
Alternately, in the front stage view, on the
Home
or
Calibration
ribbon, tap
Acquire (
)
.
Note
To ensure that the entire weld cap is covered by the probe’s fingers, whenever possible,
position the center of the probe’s active area on the weld’s centerline. Depending on the width
of the weld’s crown and the welding process, the probe may also cover all or part of the heat-
affected zone (HAZ).
6.
Placing appropriate pressure on the probe, move it longitudinally along the weld.
Note
The maximum speed is 200 mm/s (8 in/s) for the small (-W028) and medium (-W053) Sharck
probes.
7.
When scanning is done, press the
Start/Stop acquisition
button (
) on Reddy’s keypad.
Alternately, in the front stage view, on the
Home
or
Calibration
ribbon, tap
Stop (
)
.
Notes
•
To keep data files at a reasonable size and facilitate analysis, when inspecting very long
welds, we recommend that you divide your inspection into several appropriately short
acquisitions (e.g. less than 3 meters (10 ft)).