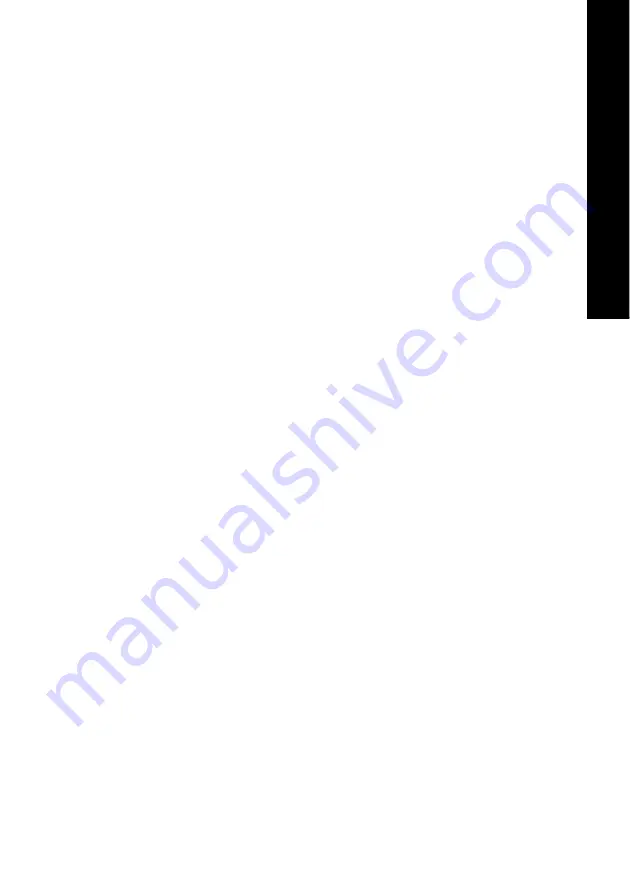
17
the optical sensor can overheat and stop de-
tecting light. Backpressure in the boiler itself
will cause soot to form on the optical sensor;
this will not have been allowed to exist at
boiler commissioning, but can occur after the
fact, if, for example, the boiler is not cleaned
internally (soot building up at the mouth of
the chimney).
CHECK: Start the burner and check that both
drive motors are operating and that the
sluice shaft and the auger shaft are rotating
in the combustion bowl.
ACTION: If there is a fault, contact the instal-
lation engineer.
CHECK: That the burner is taking fuel from
the external store.
ACTION: If the burner does not attempt to
take fuel from the external store, this may be
because it thinks there is fuel in the internal
store. Contact your distributor to have the
level sensor (receiver) replaced.
Alarm message: * Ignition error *
The burner has received a signal to stop,
because the optical sensor is not detecting
light in the combustion chamber during the
ignition sequence.
The burner makes three ignition attempts.
ACTION: The maintenance burn function is
enabled, see pages 9-11.
Contact the installation engineer for help.
During a manual start, check the optical sen-
sor. Also see * Fire burned out * description.
Alarm message: * Combustian fan *
The burner does not run, due that the
combustion fan which is equipped with a
tachometer has stopped during operation.
CONTROL: The fanwheel spins properly and
runs without obstacles.
ACTION: Adjust the wheel, if it does not spin
freely.
CHECK: That the cable with its pins are con-
nected.
ACTION: Connected the loose pins, other-
wise call the installer.
Alarm message: * Pellets failure *
This fault is caused by a lack of fuel in the
burner's internal store.
CHECK: That there are pellets in the exter-
nal store.
ACTION: Add pellets. CHECK: That the angle
of the auger is not too steep (maximum
45°) or that the fl ow has not stopped be-
cause an airlock has formed in the base of
the external store.
ACTION: Adjust the auger to a shallower
angle and turn it to and for a few times.
It must be positioned in the centre of the
external store.
CHECK: That the drive motor of the external
auger is working and that the motor shaft
is turning the auger.
ACTION: Test the external motor sepa-
rately using the parameters on pages 9-11.
Tighten the Allen bolt on the bevelled part
of the motor shaft. If the motor is faulty,
contact the installation engineer.
CHECK: That the hose to the burner is not
at too shallow an angle.
ACTION: Adjust the angle so that the pel-
lets do not block the hose.
CHECK: That an airlock (cone) has not
formed in the internal or external store.
ACTION: Airlocks (cones) can form in the
store if the angle of the base of the store is
to fl at or as a result of damp pellets, dust
or overfi lling. Tap on the store. Replace the
damp pellets immediately. Damp pellets
can bring the system to a complete stop
and cause damage. If the store has been
overfi lled, contact the installation engineer.
Airlocks (cones) could also form if there has
build up dust in the store. If airlocks (cones)
form in external store then, when possile,
the store should be cleaned from dust, e.g.
before external store is refi lled.
TR
OUBLESHOO
TING
Содержание BioLine 20
Страница 23: ...23 WIRING TABLE CONTROL CABINET...
Страница 24: ...24 OPERATING NOTES OPERATING NOTES Date Measure...
Страница 25: ...25 OPERATING NOTES OPERATING NOTES Date Measure...
Страница 26: ...26 OPERATING NOTES OPERATING NOTES Date Measure...
Страница 27: ...27 OPERATING NOTES OPERATING NOTES Date Measure...