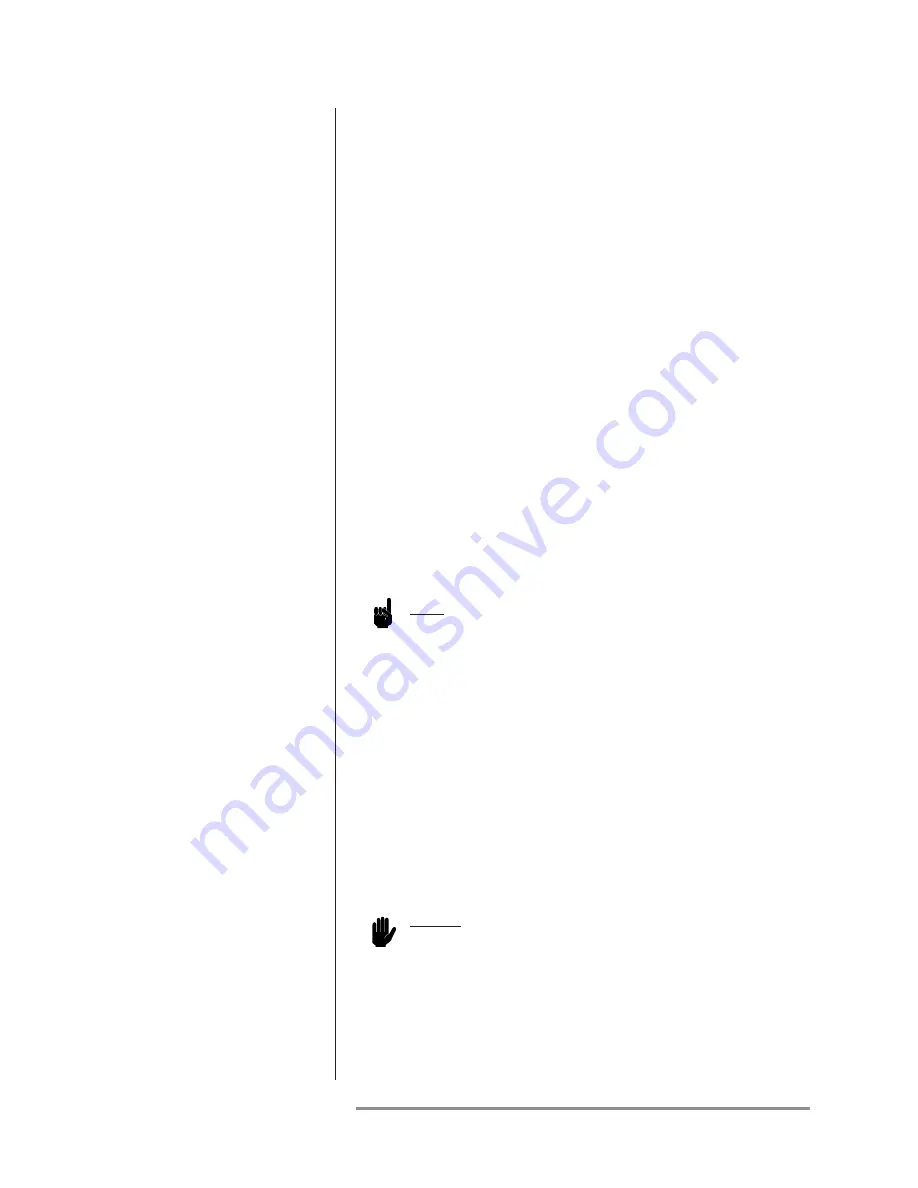
Field installed refractory
The customer is responsible for supplying all refractory materials
for field installation as follows:
1. Cover the inside surfaces of the combustor shell with an 1/8"
layer of Plibrico “Plisulate” fibrefax paper or equivalent.
2. Install alloy anchors in the combustor shell according to the
refractory supplier’s recommendations. The alloy anchors should
be coated with bitumastic wherever they protrude through the
layer of Plibric Plisulate.
3. Install the chosen refractory, realizing it is essential that:
• the combustion block dimensions are held as given on Eclipse
drawings
• the inside diameter of the combustion block be concentric
with the air cone in the burner.
Refer to Figure 3.3 for wall interface, and typical refractory
installation details and recommendations.
4. The refractory should then be pounded into place with a
pneumatic rammer, starting around the air cone. Use care in
ensuring that the specified contours and dimensions on the
aforementioned Eclipse drawing are maintained. Provide vent
holes so moisture can escape during dry-out.
Note:
The corner angle between the cone and the sidewall must be
90
°
or slightly less, but NOT MORE.
After the burner and refractory have been installed, the following
steps will ensure proper curing and maximum strength to reduce
chances of cracking or spalling:
1. Set the combustion air at its minimum input.
2. Light only the pilot and leave on for approximately three hours.
3. After three hours, light the main burner at the minimum input.
4. Increase the heat input by 100
°
F per hour.
5. Water evaporation (steam) is usually heaviest and most
prominent around 1,000
°
F. If steam is still prevalent after the
hour at 1,000
°
F, hold at that temperature for two to three
more hours or until the steam stops.
Caution:
If at anytime during the curing process visible steam rises from
the refractory, hold the temperature until it dissipates.
6. Once steam stops coming from the refractory, assume the 100
°
F
temperature rise per hour until you reach 2,000
°
F.
7. Hold at 2,000
°
F for three to four hours to ensure proper curing.
3-12
Eclipse Vortometric Burner v2.00, Installation Guide 248, 4/10/07