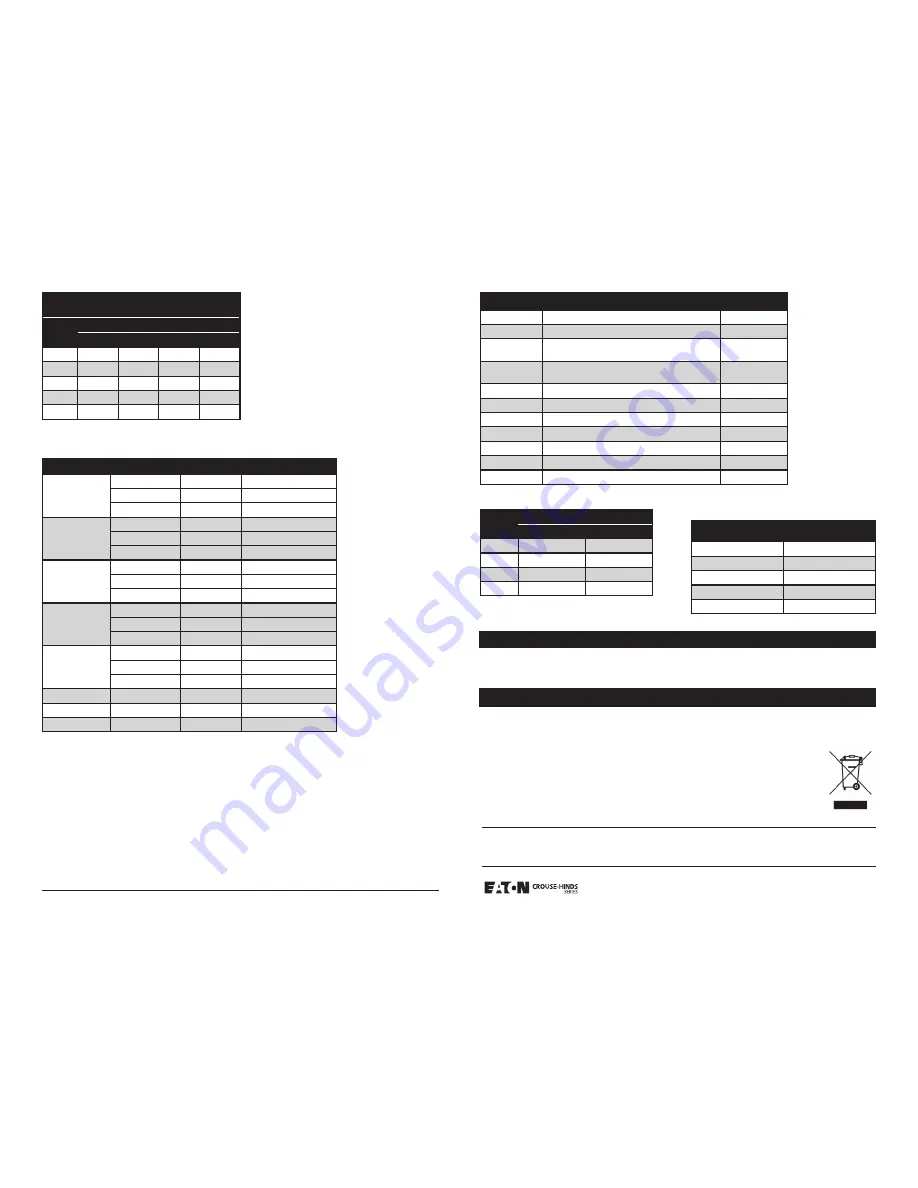
Copyright © 2018 Eaton’s Crouse-Hinds Division
Page 7
All statements, technical information and recommendations contained herein are based on information and tests we believe
to be reliable. The accuracy or completeness thereof are not guaranteed. In accordance with Eaton’s Crouse-Hinds Division’s
“Terms and Conditions of Sale,” and since conditions of use are outside our control, the purchaser should determine the
suitability of the product for his intended use and assumes all risk and liability whatsoever in connection therewith.
Eaton’s Crouse-Hinds Division
IF 1688
1201 Wolf Street, Syracuse, NY 13208
Revision 4
Copyright © 2018
Revised 08/18
Supersedes 05/15
•
cURus
•
IP68, NEMA 4X, NEMA 6P
Section 11: Certifications
Section 12: Maintenance Information
Electrical and mechanical inspection of all components must
be performed on a regularly scheduled basis, determined by
the environment and frequency of use. It is recommended
that inspection be performed a minimum of once a year.
1.
Inspect contact crimp locations for security.
2.
Clean exterior surfaces, making sure nameplates
remain legible.
3.
Check tightness of all shell parts before using.
4.
Check contacts for signs of excessive burning or arcing
and replace if necessary.
5.
Check shell parts for damage to threads and skirts and
replace if necessary.
In addition to these required maintenance procedures,
we recommend an Electrical Preventative
Maintenance Program as described in the
National Fire Protection Association Bulletin
NFPA No. 70B.
Table 5. Contact Insertion and Removal Tools
Pin
gauge
Removal
Insertion
Part no.
Part no.
8
CH 2-8250
CH 1265
10
CH 2-8250
CH 1205
12
CH 2-8250
AT 1000-12
16
CH 2-8250
AT 1000-16
IF 1688 • 08/18
Table 2. External Cable Jacket Strip Length
Jacket strip length
(culti-conductor cable)
Standard adapter
Long adapter
inches
mm
inches
mm
12 shell
1.25
31.75
3.5
89
16 shell
1.5
38
3.75
95.25
20 shell
2
51
4.25
108
24 shell
2.5
63.5
4.75
120.5
28 shell
3.4
87
5.4
138.0
Table 3. Torque Values for Shell Component Assembly
Shell size
Thread
Metric (N-m)
English values (ft.-lb.)
12
LH thread
34.0
25
Coupling nut
20.3
15
Metric gland (M25)
47.5
35
16
LH thread
40.5
30
Coupling nut
27.1
20
Metric gland (M40)
47.6
35
20
LH thread
47.5
35
Coupling nut
33.9
25
Metric gland (M50)
80.0
59
24
LH thread
54.0
40
Coupling nut
40.7
30
Metric gland (M63)
95.0
70
28
LH thread
58
43
Coupling nut
65
48
Metric gland
73
54
Panel mount
M5 panel bolt
5.4
4
Mechanical clamp
Clamp bolts
3.4
2.5
Bus bar
Clamp bolts
101
75
Table 4. Contact Crimping Tools and Dies
Contact size
Crimp Tool
Die #
23 AWG
CH300-25 A
CH682-1
16 AWG
CH300-25 A
CH682-1
13 AWG
CH300-25 A
CH684-1 – socket
CH683-1 – pin
12 AWG
CH300-25 A
CH684-1 – socket
CH683-1 – pin
10 AWG
CH300-25 A
CH684-1
8 AWG
13100A T&B 14 ton hydraulic crimper head or equivalent
15520 / 21
4 AWG
13100A T&B 14 ton hydraulic crimper head or equivalent
15527 / 29
313 MCM
13100A T&B 14 ton hydraulic crimper head or equivalent
15512 / 76
444 MCM
13100A T&B 14 ton hydraulic crimper head or equivalent
15505 / 99H
535 MCM
13100A T&B 14 ton hydraulic crimper head or equivalent
15515 / 106H
777 MCM
13100A T&B 14 ton hydraulic crimper head or equivalent
15504 / 115H
Table 6. Mod I – Pressure Contact Torque
Requirements
Contact/conductor size/
AWG (mm)
Torque req.
in./lbs. (N-m)
4/0 (120.00)
100 (11.3)
1/0 (50.00)
50 (5.7)
#4 (25.00)
20 (2.3)
#8 (10.00)
25 (2.8)
#10 (6.00)
15 (1.7)
Eaton.com/recycling