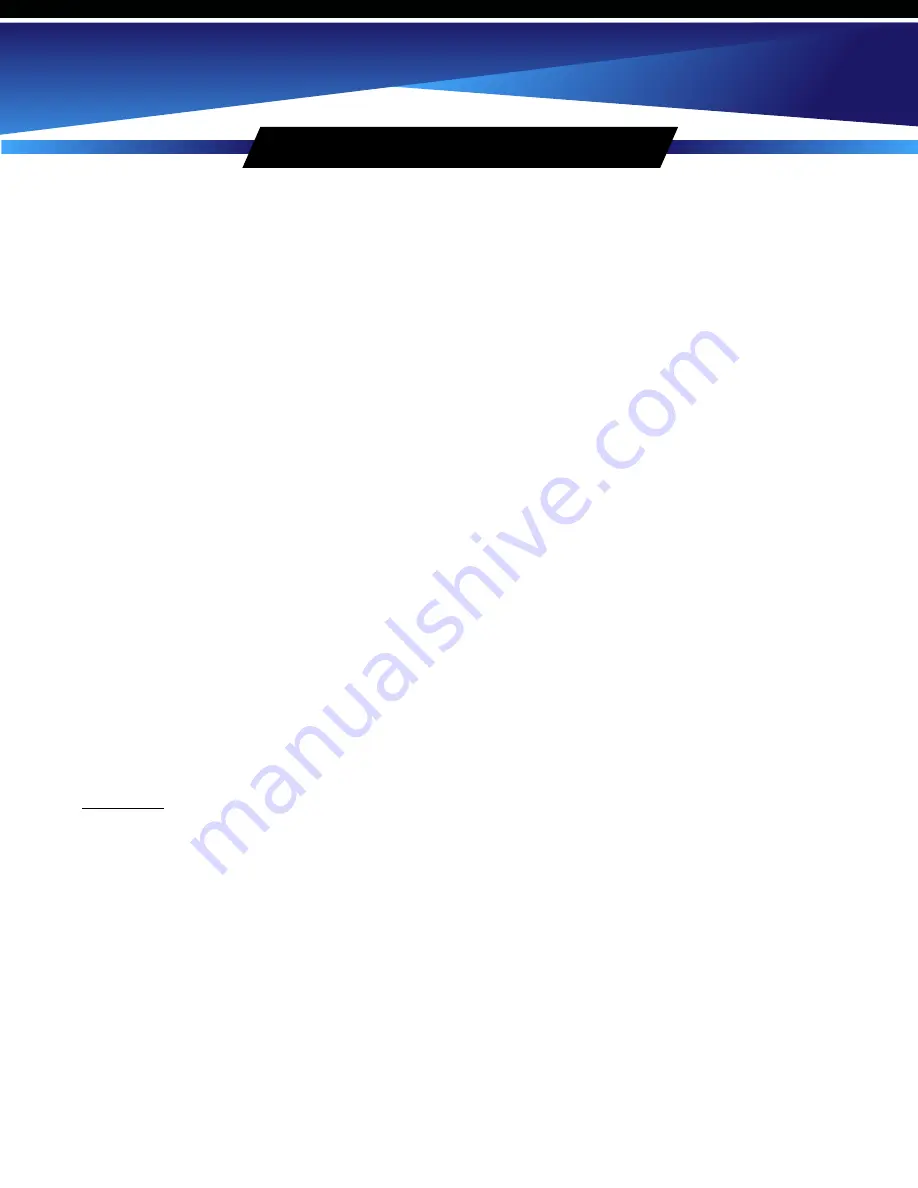
Operating Instructions
43
Parts used for warranty purposes must be supplied by Eaton Compressor and Fabrication Co., Inc. Warranty work will be performed by an approved Eaton Compressor and
Fabrication Co., Inc. Technician. If any maintenance (other than routine maintenance) is performed by a non-approved Eaton Compressor and Fabrication Co., Inc. Technician,
written pre-approval must be obtained from Eaton Compressor and Fabrication Co., Inc. to prevent voiding this Warranty. Failure to fully comply with this warranty and fully
comply with the manual herein will void this warranty.
All warranties are nontransferable.
The Oil Purchase Program is effective as of January 1, 2011.
EATON COMPRESSOR AND FABRICATION CO., INC. (and each of its subsidiaries, including Eaton Compressor, INC.) makes the following Warranties:
2.
3.
4.
5.
1. THAT EACH
ROTARY SCREW AIR COMPRESSOR PUMP
TO BE FREE FROM DEFECTS IN MATERIAL, WORKMANSHIP, AND PARTS FOR 10 YEARS ON THE ROTARY SCREW AIR
COMPRESSOR PUMP FROM THE DATE OF PURCHASE. Eaton Compressor and Fabrication Co., Inc. (and each of its subsidiaries) is not responsible for downtime during warranty
service. If downtime is necessary, it is the Purchaser’s discretion and obligation (at Purchaser’s expense) to have a redundant UNIT. This warranty applies to rotary screw rotors and
bearings. The electric motor carries a five year warranty and a 2 year warranty on the rest of the compressor unit. The screw compressor MUST have Eaton Compressor and Fabrication
Co., Inc. Lubricant Synthetic exclusively, the same which must be purchased from Eaton Compressor and Fabrication Co., Inc. (Mixing different brands of oil will void this
warranty and cause the rotors to varnish). All air filters, oil filters, and oil separator filters must be purchased from Eaton Compressor and Fabrication Co., Inc. and the screw
compressor must have Eaton Compressor and Fabrication Co., Inc. Synthetic Rotary Screw oil, purchased exclusively from Eaton Compressor and Fabrication Co., Inc., for this
warranty to apply.
Annual participation in all oil programs are required by original purchaser of the unit outlined by the following:
Failure of original purchaser to comply with any of the above conditions pertaining to oil analysis with void the complete unit warranty.
A full detailed maintenance schedule must be sent to Eaton Compressor and Fabrication Co., Inc. once a year with the total service completed quarterly, outlining each air filter,
oil filter and oil change with the total hours on the unit after each maintenance was performed.
Failure to fully comply with this warranty and fully comply with the manual herein will void this warranty.
Exclusions to this warranty also include all normal wear and tear items, including, but not limited to the bearings, rotors, valves, belts, shaft seal and load/unload solenoids.
THAT EACH
BARE COMPRESSOR PUMP UNIT
TO BE FREE FROM DEFECTS IN MATERIAL, WORKMANSHIP, AND PARTS FOR 5 YEARS FOR THE UNIT FROM THE DATE OF
PURCHASE. Eaton Compressor and Fabrication Co., Inc. (and each of its subsidiaries) is not responsible for downtime during warranty service. If downtime is necessary, it is the
Purchaser’s discretion and obligation (at Purchaser’s expense) to have a redundant UNIT. Warranty repairs shall not include freight costs. Purchaser is responsible for returning
unit to Eaton Compressor and Fabrication Co., Inc. This pump must have Eaton Compressor and Fabrication Co., Inc. lubricant Synthetic exclusively, the same which must be
purchased from Eaton Compressor and Fabrication Co., Inc. (Mixing different brands of oils will void the pump warranty). A service kit must be purchased from Eaton Compressor
and Fabrication Co., Inc. for this warranty to apply. Service kits contain an air filter and synthetic oil that must be changed annually. Annual proof of purchase of all oil
programs must be maintained by the original purchaser of the compressor pump. If the unit runs out of oil, this warranty is void. Failure to fully comply with this warranty
and fully comply with the manual herein will void this warranty.
Exclusions include: service such as OIL CHANGES, FILTER REPLACEMENTS, GASKET TIGHTENING TO CORRECT OIL SEEPAGE or DRIVE BELT TIGHTENING and VALVE CLEANING and
are not covered under warranty.
Warranty shall be void under the following conditions: Failure to routinely change oil and to maintain a clean filter, or
exceeding 70% duty cycle resulting in overheating and
excessive wear and tear,
or exposing electrical components to rain or water, or installing the unit in a hostile environment such as acid vapors or any caustic or abrasive matter that
may be ingested into the pump, or installing the unit in an enclosed area where lack of cooling ventilation is present, such as in boiler or equipment rooms where the ambient air
exceeds 100°F.
THAT EACH
COMPRESSOR UNIT
TO BE FREE FROM DEFECTS IN MATERIAL, WORKMANSHIP, AND PARTS FOR 5 YEARS FOR THE COMPRESSOR PUMP AND 2 YEARS ON THE
REMAINDER OF THE UNIT FROM THE DATE OF PURCHASE. The UNIT also carries a 1-year labor warranty. Eaton Compressor and Fabrication Co., Inc. (and each of its
subsidiaries) is not responsible for downtime during warranty service. If downtime is necessary, it is the Purchaser’s discretion and obligation (at Purchaser’s expense) to have a
redundant compressor. Warranty repairs shall not include freight costs. Purchaser is responsible for returning unit to Eaton Compressor and Fabrication Co., Inc. This pump MUST
have Eaton Compressor and Fabrication Co., Inc. Lubricant Synthetic exclusively, the same which must be purchased from Eaton Compressor and Fabrication Co., Inc. (Mixing
different brands of oil will void this warranty). A service kit must be purchased from Eaton Compressor and Fabrication Co., Inc. for this warranty to apply. Service kits contain
an air filter and synthetic oil that must be changed annually. Annual proof of purchase of all oil programs must be maintained by the original purchaser of the compressor unit. If
the unit runs out of oil, this warranty is void. Failure to fully comply with this warranty and fully comply with the manual herein will void this warranty.
Exclusions include: service such as OIL CHANGES, FILTER REPLACEMENTS, GASKET TIGHTENING TO CORRECT OIL SEEPAGE or DRIVE BELT TIGHTENING and VALVE CLEANING and
are not covered under warranty.
Warranty shall be void under the following conditions: Failure to routinely change oil and to maintain a clean filter, or
exceeding 70% duty cycle resulting in overheating and
excessive wear and tear,
or exposing electrical components to rain or water, or installing the unit in a hostile environment such as acid vapors or any caustic or abrasive matter that
may be ingested into the pump, or installing the unit in an enclosed area where lack of cooling ventilation is present, such as in boiler or equipment rooms where the ambient air
exceeds 100°F.
THAT EACH
DRYER UNIT
TO BE FREE FROM DEFECTS IN MATERIAL, WORKMANSHIP, AND PARTS FOR 5 YEARS on the HEAT EXCHANGER AND 2 YEARS ON THE DRYER UNIT
FROM THE DATE OF PURCHASE. Eaton Compressor and Fabrication Co., Inc. (and each of its subsidiaries) is not responsible for downtime during warranty service. If downtime is
necessary, it is the Purchaser’s discretion and obligation (at Purchaser’s expense) to have a redundant DRYER UNIT. Warranty repairs shall not include freight costs. Purchaser is
responsible for returning unit to Eaton Compressor and Fabrication Co., Inc. Each
DRYER UNIT
must have a coalescing filter attached to the intake of the dryer to remove any oil
or dirt before air enters the dryer. Failure to install coalescing filter will void the warranty.
GENERAL PROVISIONS: Eaton Compressor and Fabrication Co., Inc. (and each of its subsidiaries) is not responsible for downtime during warranty service. If downtime is necessary,
it is the Purchaser’s discretion and obligation (at Purchaser’s expense) to have a redundant compressor. Warranty repairs shall not include freight costs. If necessary, the
Purchaser is responsible for returning unit and/or applicable part(s) to Eaton Compressor and Fabrication Co., Inc.
Exclusions include: service such as OIL CHANGES, FILTER REPLACEMENTS, GASKET TIGHTENING TO CORRECT OIL SEEPAGE or DRIVE BELT TIGHTENING and VALVE CLEANING and
are not covered under warranty.
Further Exclusions include failure to fully and completely follow the guidelines set forth in the manual. Of specific note is where a product is used where granite and/or concrete
work is performed or conditions are dusty and the product is required to be housed in a separate room from the adverse conditions where the product has access to fresh air intake.
Warranty Statement
a) Purchase an oil sample kit for oil analysis by Eaton Compres sor and
Fabrication Co., Inc.
b) Oil sample kit contains 20 oil sample containers. One (1) oil sample
is to be sent for analysis by an Eaton Compressor oil analysis labora
tory every six (6) months so oil can be tested twice yearly.
c) Oil samples are obtained by draining 4 ozs. of oil into container then
mailing sample container to laboratory address provided in
oil sample kit.
d) The laboratory will perform an oil analysis then email a report
e) Provide annual proof of purchase for oil/filter service kit.
f) Maintain proper oil level in unit at all times. If the unit runs out of oil,
this warranty is void.
Содержание PRS0100001
Страница 1: ...Operating Instructions 1...
Страница 39: ...Operating Instructions 39...
Страница 40: ...Eaton Compressor Rotary Screw Compressor 40...
Страница 41: ...Operating Instructions 41...
Страница 42: ...Eaton Compressor Rotary Screw Compressor 42...