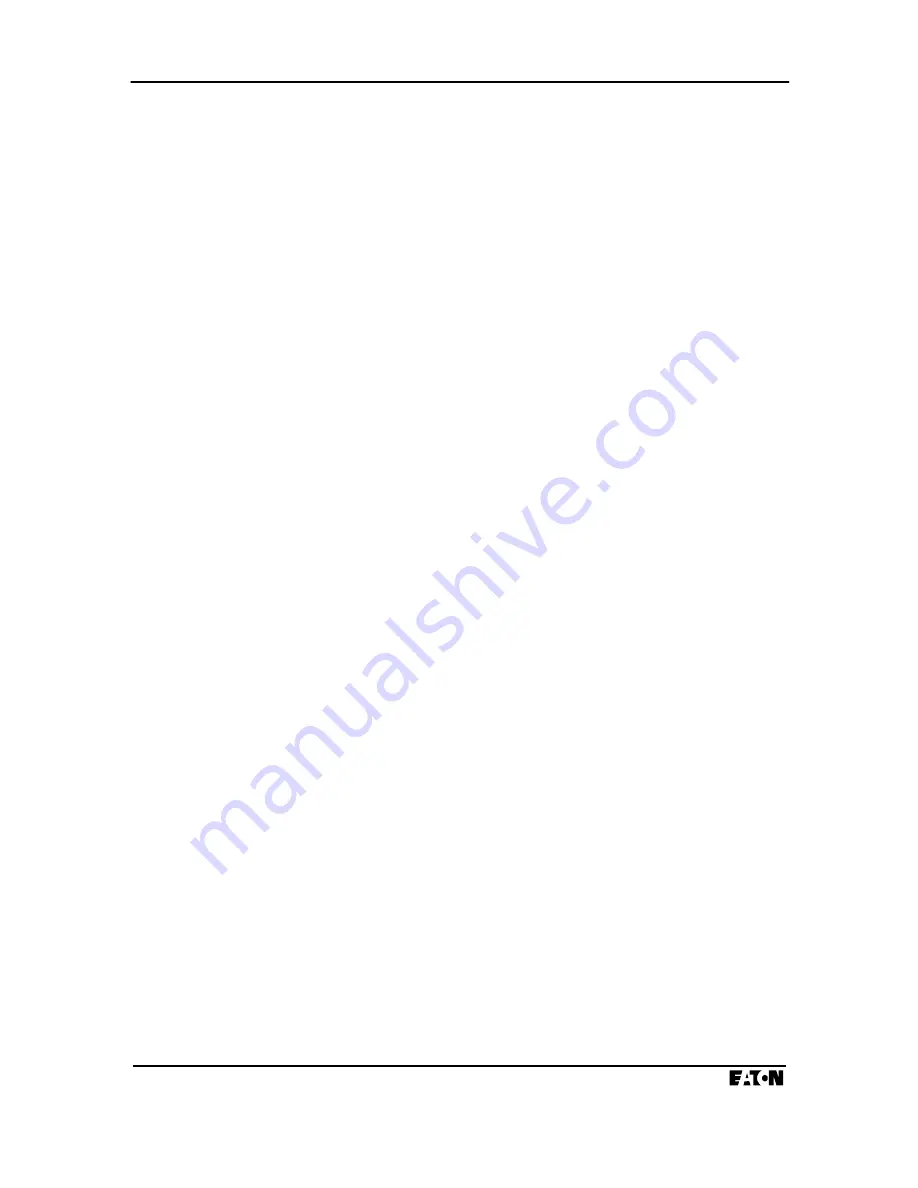
I.L. 17562
Page 85
PR 0.3 Effective 8/99
Section 8. MOTOR THERMAL PROTECTION BASICS
8.0 General
– This section describes how the MP-3000 hardware and software function together
to control, monitor, and protect the motor.
8.1 Sensing Inputs
– The MP-3000 receives motor phase currents from 3 main motor phase
current transformers. See Figure 3-1. If an optional ground fault transformer is used, the MP-
3000 monitors ground leakage or fault current as well.
The MP-3000 takes 36 samples per power cycle of the input current signals, digitizes each
sample, and stores it in the microprocessor memory. From these samples, the MP-3000
computes rms currents and average currents; plus phasor calculations leading to direct and
precise measurement of positive and negative sequence currents - see below. The high
sampling rate, plus a unique patented sample-shifting technique, allows the MP-3000 to properly
measure and account for the impact of harmonics in heating the motor.
If the optional URTD module is used, the MP-3000 gathers winding temperature data from up to
six resistance temperature detectors (RTDs) embedded in the stator windings of the motor. It
can monitor four RTDs associated with the motor bearings and load bearings. It can also monitor
one auxiliary RTD, such as motor case temperature.
8.2 Protective Functions
– Protective functions continuously monitor motor operating
conditions such as current history and temperature. When measured or derived measurements
exceed user-selected levels, an alarm condition is initiated, and then, if necessary, a trip output
opens the motor contactor or trips a breaker.
The MP-3000 can protect the motor, starter, and load in the following ways:
•
Stator and rotor thermal protection by modeling of heating and cooling effects, including
heating by negative sequence currents.
•
Stator overtemperature protection by direct measurement (with optional URTD module).
•
Instantaneous overcurrent protection for faults.
•
Ground fault protection.
•
Phase reversal protection.
•
Phase unbalance protection.
•
Motor bearing, load bearing, and auxiliary RTD temperature protection (with optional URTD
module).
•
Jam protection.
•
Underload protection.
•
Transition trip for abnormal starting time-versus-current behavior.
•
Incomplete sequence protection (missing status feedback from load or starter).
•
Trip-bypass output for failure of contactor to interrupt current after a trip command.
•
Zero-speed switch stalled-motor trip protection.
•
Process load shedding function to forestall impending jam or thermal trips.
•
Jogging protection - minimum time between starts, maximum number of starts per set time,
maximum number of consecutive cold starts, and minimum time between stop and start
(antibackspin protection).
Many of these functions also have separate alarm thresholds to warn the user, who may be able
to act before a trip occurs.
The MP-3000 has four output relays. The Trip relay is connected in series with the motor
contactor, and deenergizes the contactor or blocks starting for any MP-3000 trip condition. All
trips are steered to this relay.
Содержание MP-3000
Страница 18: ...Page 18 I L 17562 PR 0 3 Effective 8 99 Figure 4 1 MP 3000 Pushbuttons...
Страница 19: ...I L 17562 Page 19 PR 0 3 Effective 8 99 Figure 4 2 MP 3000 LED Indicators...
Страница 72: ...Page 72 I L 17562 PR 0 3 Effective 8 99 Figure 6 1 Panel Cutout Dimensions...
Страница 73: ...I L 17562 Page 73 PR 0 3 Effective 8 99 Figure 6 2 Faceplate Dimensions...
Страница 74: ...Page 74 I L 17562 PR 0 3 Effective 8 99 Figure 6 3 MP 3000 Case Depth Dimensions...
Страница 75: ...I L 17562 Page 75 PR 0 3 Effective 8 99 Figure 6 4 Universal RTD Module Mounting Dimensions...
Страница 76: ...Page 76 I L 17562 PR 0 3 Effective 8 99 Figure 6 5 Rear Panel Terminals...
Страница 77: ...I L 17562 Page 77 PR 0 3 Effective 8 99 Figure 6 6 Typical Ct Circuits and Motor Control Wiring...
Страница 78: ...Page 78 I L 17562 PR 0 3 Effective 8 99 Figure 6 7 Typical ac Supply and URTD Wiring...
Страница 79: ...I L 17562 Page 79 PR 0 3 Effective 8 99 Figure 6 8 Alternatives for Discrete Input Wiring...
Страница 80: ...Page 80 I L 17562 PR 0 3 Effective 8 99 Figure 6 9 RTD Wiring to URTD Module...
Страница 88: ...Page 88 I L 17562 PR 0 3 Effective 8 99 Figure 8 1 System Overview Figure 8 2 Torques from Sequence Currents...
Страница 100: ...Page 100 I L 17562 PR 0 3 Effective 8 99 Figure 9 1 Rotor Temperature Tracking...
Страница 101: ...I L 17562 Page 101 PR 0 3 Effective 8 99 Figure 9 2 Motor Protection Curve...
Страница 102: ...Page 102 I L 17562 PR 0 3 Effective 8 99 Figure 9 3 Underload Jam Protection Curve...
Страница 103: ...I L 17562 Page 103 PR 0 3 Effective 8 99 Figure 9 4 Motor Protection Curve Example without RTDs...
Страница 104: ...Page 104 I L 17562 PR 0 3 Effective 8 99 Figure 9 5 Motor Protection Curve Example with RTDs...
Страница 105: ...I L 17562 Page 105 PR 0 3 Effective 8 99 Figure 9 6 Motor Start and Run Cycles...
Страница 109: ...I L 17562 Page 109 PR 0 3 Effective 8 99 P5L8 40 Incomplete Sequence time 1 60s OFF 1 240s...