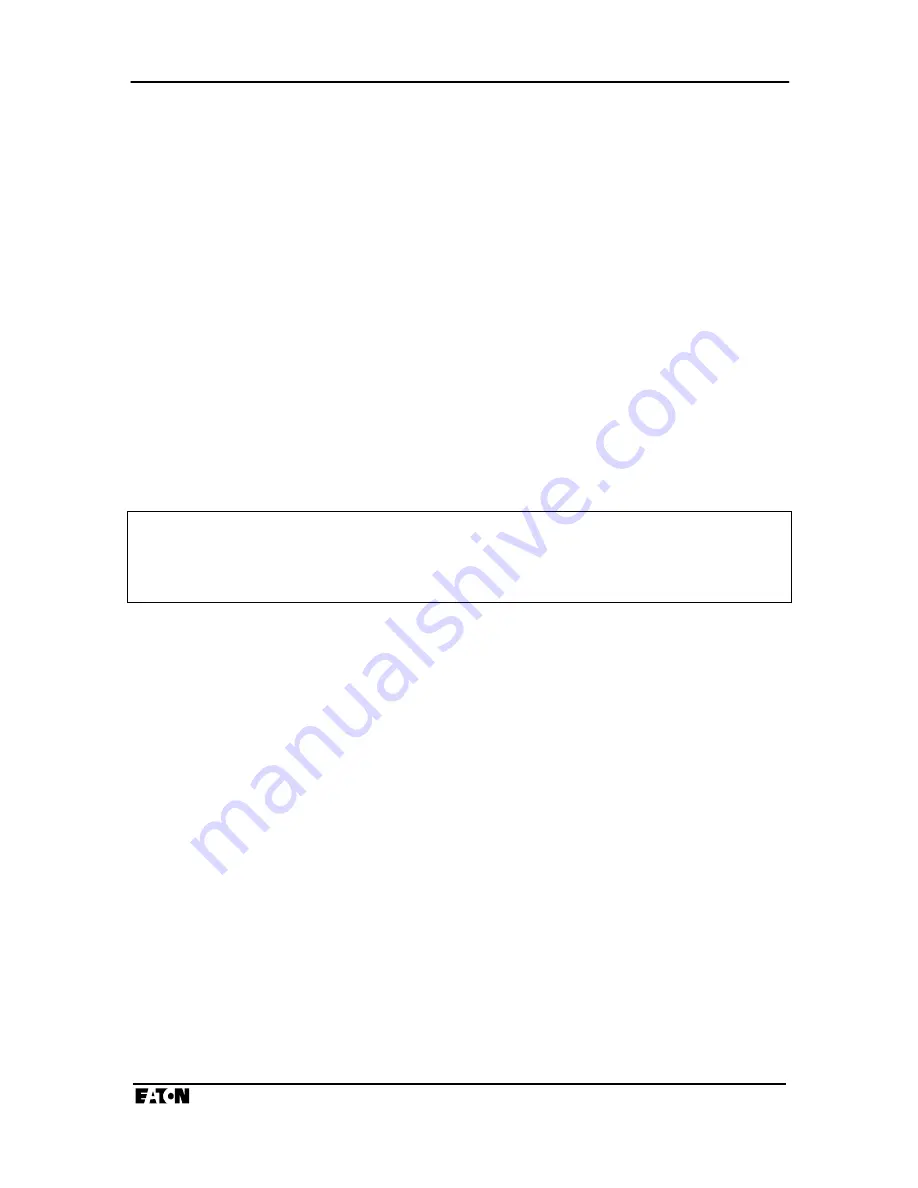
Page 68
I.L. 17562
PR 0.3 Effective 8/99
The PONI, if used, is always mounted on the back of the MP-3000. If no URTD is mounted
there, use the mounting bracket supplied with the MP-3000 as shown in Figure 6.3. The bracket
gives a convenient space to run ct wires underneath the PONI to the adjacent Ct terminal block.
If a URTD is mounted on the back of the MP-3000, the PONI piggybacks directly to the URTD
module as shown. Use the machine screws supplied with the PONI in the molded plastic
mounting holes of the URTD.
6.2 Wiring – General
— When routing wires between the starter and the associated machine or
process equipment, follow these guidelines:
•
Do not route the control or RTD wiring through the high-voltage compartment of the motor
starter. However, the starter manufacturer may be able to recommend or provide specific
measures for doing this if really necessary.
•
Separate the lower voltage (120 Vac) from the higher voltage (440 Vac or higher) conductors
as much as possible. In general, maintain a minimum distance of 1.5 feet (45 cm) between
the two types.
•
Any low-voltage control wiring routed out of the motor starter cabinet should be at least
#14 AWG stranded copper wire.
•
Communications circuits may use thinner conductors, as recommended in installation
literature for those circuits.
WARNING
Before working with the wiring, make sure power is disconnected from the motor starter, MP-
3000, and all remote connections including contact output control circuits and remote input
contacts. Otherwise, hazardous voltages could cause injury or death. Also, unexpected motor
control action could injure personnel or destroy equipment.
Figure 6.5 shows MP-3000 rear terminal connections.
Connect terminal 5 to the closest solid electrical-safety grounding point with a heavy wire or
braid (#14 AWG or larger). Do not use a current-carrying or neutral conductor for this grounding.
Do not tie terminal 5 to neutral terminal 7 at the relay. Note that terminal 5 is internally
connected to the outer case and to the conductive faceplate of the relay.
6.2.1 Ct Wiring -
Carefully read the advice in Section 5.1.5 on choice of Ct ratios for a particular
motor application. An inappropriate Ct ratio will result in poor measurement accuracy and
limited protection. More serious errors in ratio choice will make it impossible to set the relay
properly.
Connect the phase and optional ground cts as shown in Figure 6.6. Pay attention to the phase
identification and sequence, and check for consistent polarity among the three phases. The MP-
3000 may not allow the motor to run, and cannot protect properly, if two phases are swapped, or
if the polarity of any ct is reversed with respect to the other two.
Pass the motor phase conductors through the window of the flux-canceling ground Ct. The
ground ct need not have any particular polarity relationship to the phase cts.
To minimize problems with Ct saturation during faults, keep the Ct wiring as short as possible
and use very heavy wire. The total resistance of the connecting wire should not be much larger
than the secondary resistance of the Ct itself. The MP-3000 presents very low burden.
Every phase and ground ct circuit must have one and only one grounding point. Figure 6.6
shows the common neutral connection of the three phase Cts, and the ground fault Ct,
Содержание MP-3000
Страница 18: ...Page 18 I L 17562 PR 0 3 Effective 8 99 Figure 4 1 MP 3000 Pushbuttons...
Страница 19: ...I L 17562 Page 19 PR 0 3 Effective 8 99 Figure 4 2 MP 3000 LED Indicators...
Страница 72: ...Page 72 I L 17562 PR 0 3 Effective 8 99 Figure 6 1 Panel Cutout Dimensions...
Страница 73: ...I L 17562 Page 73 PR 0 3 Effective 8 99 Figure 6 2 Faceplate Dimensions...
Страница 74: ...Page 74 I L 17562 PR 0 3 Effective 8 99 Figure 6 3 MP 3000 Case Depth Dimensions...
Страница 75: ...I L 17562 Page 75 PR 0 3 Effective 8 99 Figure 6 4 Universal RTD Module Mounting Dimensions...
Страница 76: ...Page 76 I L 17562 PR 0 3 Effective 8 99 Figure 6 5 Rear Panel Terminals...
Страница 77: ...I L 17562 Page 77 PR 0 3 Effective 8 99 Figure 6 6 Typical Ct Circuits and Motor Control Wiring...
Страница 78: ...Page 78 I L 17562 PR 0 3 Effective 8 99 Figure 6 7 Typical ac Supply and URTD Wiring...
Страница 79: ...I L 17562 Page 79 PR 0 3 Effective 8 99 Figure 6 8 Alternatives for Discrete Input Wiring...
Страница 80: ...Page 80 I L 17562 PR 0 3 Effective 8 99 Figure 6 9 RTD Wiring to URTD Module...
Страница 88: ...Page 88 I L 17562 PR 0 3 Effective 8 99 Figure 8 1 System Overview Figure 8 2 Torques from Sequence Currents...
Страница 100: ...Page 100 I L 17562 PR 0 3 Effective 8 99 Figure 9 1 Rotor Temperature Tracking...
Страница 101: ...I L 17562 Page 101 PR 0 3 Effective 8 99 Figure 9 2 Motor Protection Curve...
Страница 102: ...Page 102 I L 17562 PR 0 3 Effective 8 99 Figure 9 3 Underload Jam Protection Curve...
Страница 103: ...I L 17562 Page 103 PR 0 3 Effective 8 99 Figure 9 4 Motor Protection Curve Example without RTDs...
Страница 104: ...Page 104 I L 17562 PR 0 3 Effective 8 99 Figure 9 5 Motor Protection Curve Example with RTDs...
Страница 105: ...I L 17562 Page 105 PR 0 3 Effective 8 99 Figure 9 6 Motor Start and Run Cycles...
Страница 109: ...I L 17562 Page 109 PR 0 3 Effective 8 99 P5L8 40 Incomplete Sequence time 1 60s OFF 1 240s...