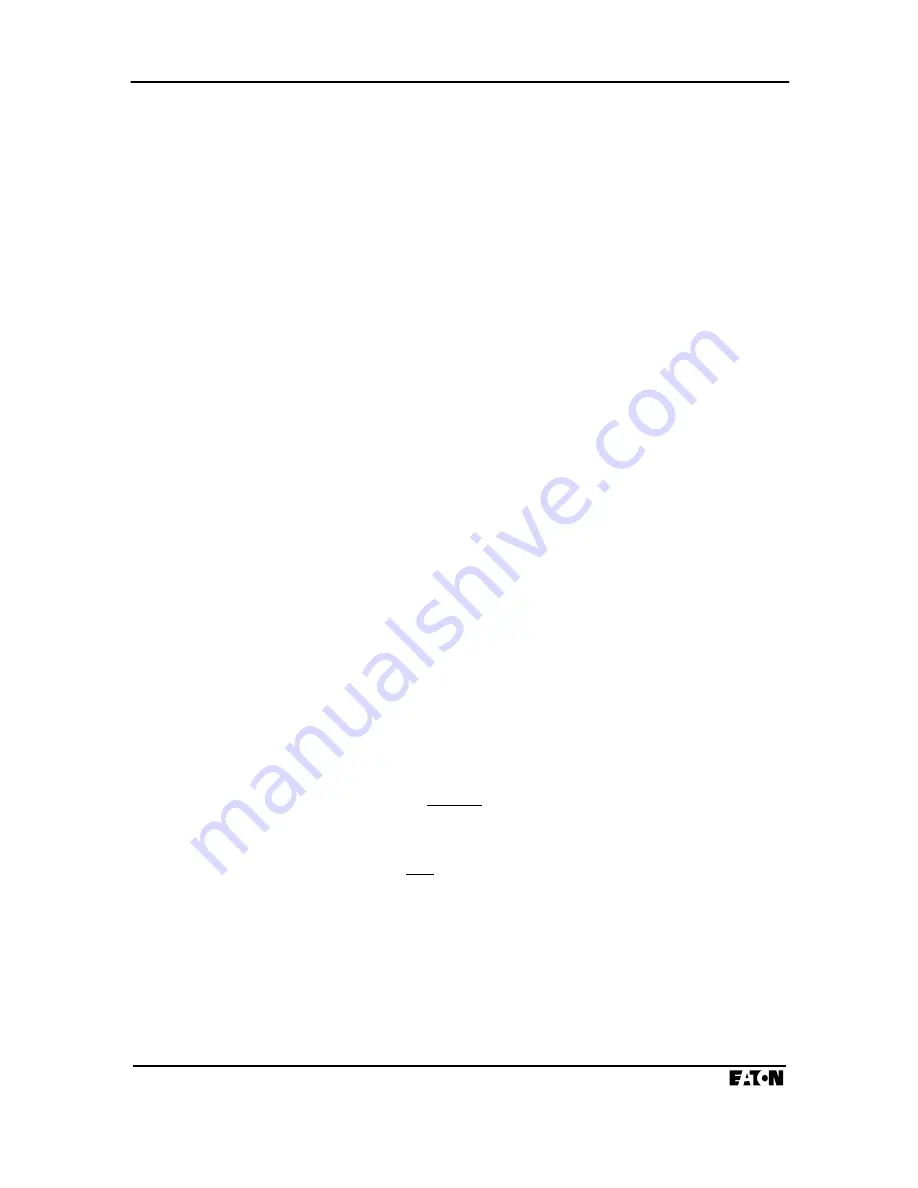
I.L. 17562
Page 69
PR 0.3 Effective 8/99
connected at one point to a non-current-carrying ground. Do not use a neutral or current-carrying
conductor for this grounding - the noise will disrupt MP-3000 measurements.
Residual connection of the phase Ct secondaries to form a ground current signal will not give
sensitivity approaching that of the flux-canceling ground Ct. See Section 9.1.10.
6.2.2 Output Contact Wiring -
See Specifications for ratings of output contacts, and check
against controlled loads.
Figure 6.6 shows a typical connection of MP-3000 output relay contacts in the motor control
circuits. However, the outputs other than the trip relay are completely programmable, so there
can be nearly infinite choice in the connection and use of these outputs for tripping, alarming,
and auxiliary control.
The installation design engineer must study Sections 5 and 9 to understand the available output
functions and programming options. This engineer must record and confirm the setpoints, and
also design a consistent connection of the form c contacts of the four output relays to the motor
control system.
Pay attention to these features of the programming and contact use:
•
Each relay can be set as Mode 1 (normally deenergized; energized to activate) or Mode 2
(normally energized; deenergize to activate). Weigh this against the use of NO versus NC
contacts in the control scheme. See Section 5.12.1.
•
All trips are steered to the trip relay (terminals 11-12-13) without choice - connect this to the
contactor or trip coil. For all other relays and functions, the user chooses what function
activates which relay.
•
It is recommended to use the alarm relay in Mode 2, and to direct all alarm conditions to it.
Connect the annunciator to terminals 17 and 18. With this connection, an alarm will be
given if the relay or its power supply fails; as well as for all other problems the MP-3000 can
actively report. However, if the MP-3000 is deenergized routinely in service, use the alarm
relay in Mode 1 and connect the annunciator to terminals 18 and 19 to avoid nuisance
alarms.
•
If the relay AUX 1 is set for the process load shedding function, it can't be used for anything
else.
•
If the relay AUX 2 is set for transition control of a reduced-voltage starter, it can't be used for
anything else.
6.2.3 Ac supply wiring -
Refer to Figure 6.7. Connect terminals 4 and 7 to a source of control
power rated at either 120 Vac or 240 Vac. The MP-3000 automatically configures its power
supply to work with one or the other value. Nominal values other than 120 Vac or 240 Vac are
not recommended. However, the MP-3000 is well able to handle depressions, dips, and limited
sustained variations in the normal course of service. See Specifications.
The optional URTD module can operate only from 120 Vac. For a 240 Vac source, use a step-
down transformer suitable for a load of 6 VA. Do not attempt to power the URTD from the MP-
3000 120 Vac discrete source - that source is for contact reading only and cannot handle the
URTD burden.
If the supply is a dc battery system, use the optional IQ DC power supply. The IQ DC supply is
able to power the MP-3000, the URTD if used, and the discrete input circuits of the MP-3000.
The total burden capability of the IQ DC module is 30 VA, and it can operate from nominal
voltages of 40 Vdc to 250 Vdc. See IQ DC Power Supply Module I.L. 17286.
6.2.4 Discrete input contact wiring -
Refer to Figures 6.7 and 6.8. The particular contacts to
Содержание MP-3000
Страница 18: ...Page 18 I L 17562 PR 0 3 Effective 8 99 Figure 4 1 MP 3000 Pushbuttons...
Страница 19: ...I L 17562 Page 19 PR 0 3 Effective 8 99 Figure 4 2 MP 3000 LED Indicators...
Страница 72: ...Page 72 I L 17562 PR 0 3 Effective 8 99 Figure 6 1 Panel Cutout Dimensions...
Страница 73: ...I L 17562 Page 73 PR 0 3 Effective 8 99 Figure 6 2 Faceplate Dimensions...
Страница 74: ...Page 74 I L 17562 PR 0 3 Effective 8 99 Figure 6 3 MP 3000 Case Depth Dimensions...
Страница 75: ...I L 17562 Page 75 PR 0 3 Effective 8 99 Figure 6 4 Universal RTD Module Mounting Dimensions...
Страница 76: ...Page 76 I L 17562 PR 0 3 Effective 8 99 Figure 6 5 Rear Panel Terminals...
Страница 77: ...I L 17562 Page 77 PR 0 3 Effective 8 99 Figure 6 6 Typical Ct Circuits and Motor Control Wiring...
Страница 78: ...Page 78 I L 17562 PR 0 3 Effective 8 99 Figure 6 7 Typical ac Supply and URTD Wiring...
Страница 79: ...I L 17562 Page 79 PR 0 3 Effective 8 99 Figure 6 8 Alternatives for Discrete Input Wiring...
Страница 80: ...Page 80 I L 17562 PR 0 3 Effective 8 99 Figure 6 9 RTD Wiring to URTD Module...
Страница 88: ...Page 88 I L 17562 PR 0 3 Effective 8 99 Figure 8 1 System Overview Figure 8 2 Torques from Sequence Currents...
Страница 100: ...Page 100 I L 17562 PR 0 3 Effective 8 99 Figure 9 1 Rotor Temperature Tracking...
Страница 101: ...I L 17562 Page 101 PR 0 3 Effective 8 99 Figure 9 2 Motor Protection Curve...
Страница 102: ...Page 102 I L 17562 PR 0 3 Effective 8 99 Figure 9 3 Underload Jam Protection Curve...
Страница 103: ...I L 17562 Page 103 PR 0 3 Effective 8 99 Figure 9 4 Motor Protection Curve Example without RTDs...
Страница 104: ...Page 104 I L 17562 PR 0 3 Effective 8 99 Figure 9 5 Motor Protection Curve Example with RTDs...
Страница 105: ...I L 17562 Page 105 PR 0 3 Effective 8 99 Figure 9 6 Motor Start and Run Cycles...
Страница 109: ...I L 17562 Page 109 PR 0 3 Effective 8 99 P5L8 40 Incomplete Sequence time 1 60s OFF 1 240s...