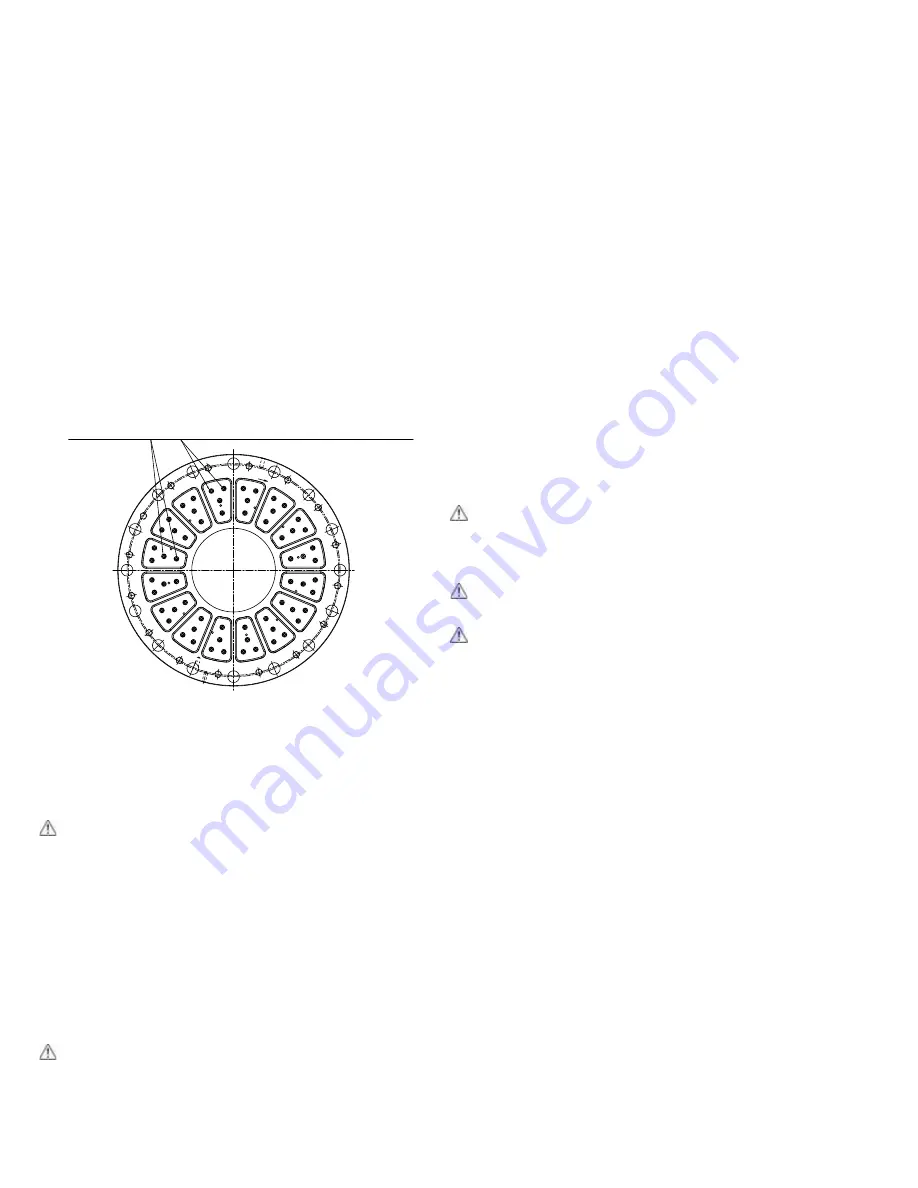
EATON Airflex WSB 11210 WCSB3 Installation Operation and Maintenance E-CLCL-11001-E October 2013
32
4.9.18 Install the remaining sixteen wear spacers (29) over
the studs. One spacer should be placed over each
stud. See Figure 1A, Section A.
4.9.19 Slide the 16 clamp tubes (124) over every stud.
4.9.20 Lower the pressure plate (13) over the clamp tubes
(124), resting the friction material face against the
disc (119).
4.9.21 Install the springs in a symmetrical pattern on the
pressure plate subassembly (13), distributing them as
evenly as possible. Locate the springs over bosses
or in the spring pockets in the pressure plate, as
shown in Figure 16. If applicable, position the spring
retainers (53) on top of the springs to hold the springs
into position.
4.9.22 Lower the spring housing (16) over the springs and
spring retainers, if applicable, aligning the match
marks made during disassembly. Be sure to not
overlap spring retainers such that they interfere with
the ribs in the spring housing (16) when assembled.
Caution
Interference of the spring retainers with the casted
ribs in the spring housing will damage the spring
retainers and may prevent proper positioning of the
springs.
4.9.23 Lubricate the ends of the studs (6) with 30 weight
oil or an anti-seize compound, and assemble the
locknuts (18) and flat washers (17) onto the studs.
Tighten the nuts in an even crosswise pattern - one
turn at a time - to evenly compress the springs.
Tighten the nuts to the final tightening torque listed
on Table 4.
Caution
The locknuts (18) must be tightened gradually to pre
vent damage to the brake components.
4.9.24 Lubricate the seals (21) (23) with Molykote 55 O-ring
lubricant, and install them into the seal grooves on
the spring housing (16). Note the orientation of the
seal lips, per Figure 13.
4.9.25 Lubricate the seal surfaces in the mounting cylinder
(19) and lower the cylinder onto the spring housing.
Orient the cylinder so that the Eaton logo is near the
“12 O’clock” position, in-line with the water outlets.
4.9.26 Position the spacer tubes (27) in-line with the bolt
holes in the cylinder, and install the hex head screws
(20) with lock-washers (17). Tighten the screws in
a crosswise pattern ONE TURN AT A TIME until the
spacer tubes are clamped between the cylinder and
pressure plate. Make sure the cylinder slides over the
seals properly to avoid damaging the seal lips.
4.9.27 Remove the screws (20) one at a time, apply Loctite
®
#262 to the screw threads, and reinstall the screw,
tightening to the value shown in Table 4. Repeat for
the remaining screws.
Warning
Loctite
®
may cure prior to properly tightening the
screw if not tightened to the proper torque value
immediately after installation.
Caution
Loctite
®
#262 must be shaken prior to application.
Caution
Loctite
®
#262 may irritate sensitive skin. Refer to the
product label for proper safety precautions.
4.9.28 After assembly, check gaps “W” and “Z-1” to ensure
that the brake will have adequate running clearances
when released. Refer to Figure 7 and Table 14.
Machining of friction discs or wear plates may be
required to achieve proper running clearances if gaps
W new and Z new are not found to be within the
ranges shown on Table 14. Correct as required.
4.9.29 Prior to installation, air test the cylinder seals for
leakage per section 4.6.3.
4.9.30 Install the WCSB3 tensioner per Section 2.0.
WCSB3 Brakes
C
SPRING LOCATIONS FOR 36WCSB3 AC PRESSURE PLATE
Four locations
per pocket X 16
pockets
Figure 16