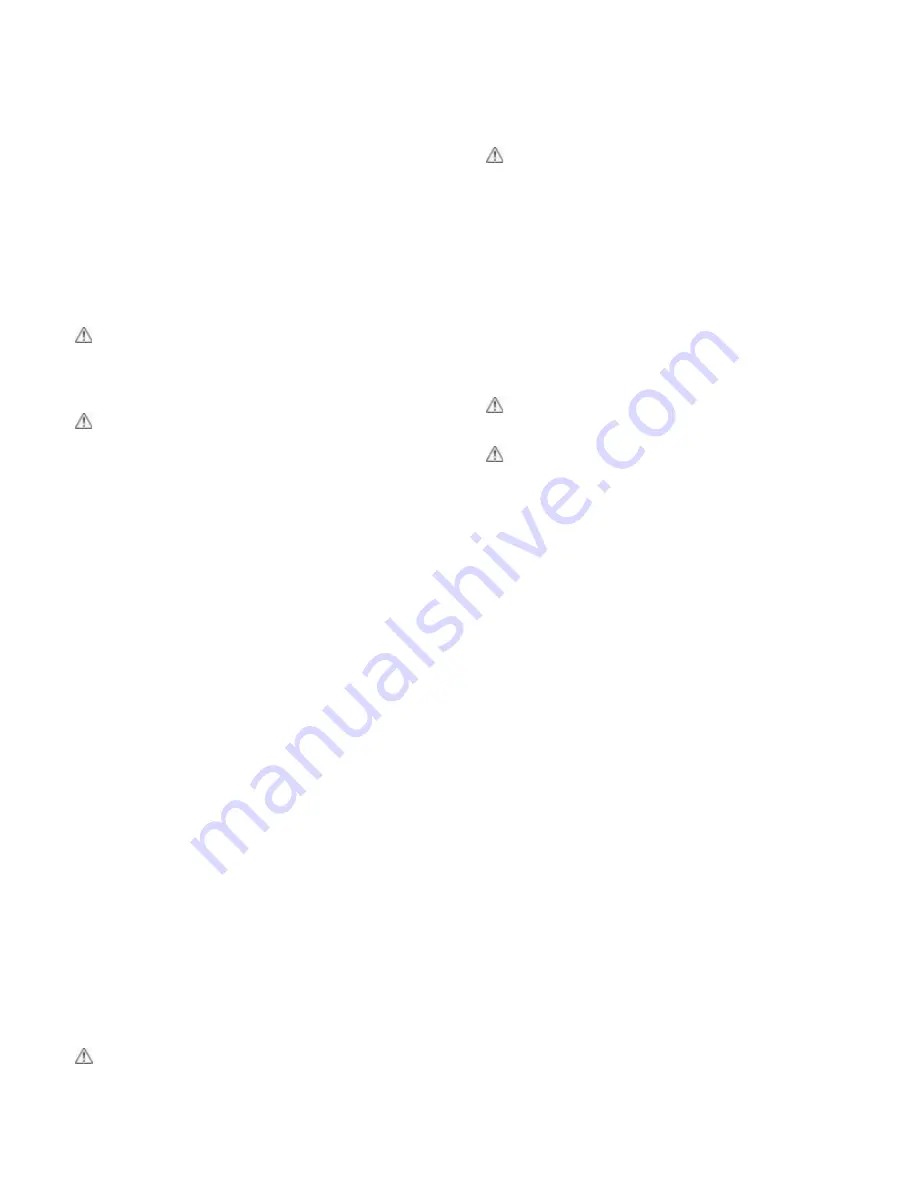
EATON Airflex WSB 11210 WCSB3 Installation Operation and Maintenance E-CLCL-11001-E October 2013
25
WCSB3 Brakes
Note: If nubs in the water cavity are severely corroded, wear
plates may not be properly supported. Replace the pressure plate
(116), reaction plate (30) or end plate (117) if necessary.
4.5.3.2 The surfaces to be painted should be sand blasted
prior to painting.
Note: Contact the paint manufacture for instructions on using
their product. Read the manufacturer’s instruction thoroughly for
proper handling, preparation, application and spray of paint
system.
Caution
Do not paint the clamp tubes (12), (124) or the
springs (34), (22), (53) as this may hinder the
engagement or disengagement of the tensioner.
Caution
Care must be taken to deal with painting in the ‘water
cavity area’ to ensure that there is full coverage of
paint with uniform thickness on the water cavity
surface. Refer to Figure 10-A to mask the inner &
outer lands that will receive the gasket tape for
sealing.
4.5.3.3 Primer: One coat of Flame Control TemperKote 1000
Primer at approximately 5.0-7.5 mils wet film
thickness to yield a dry film thickness of 2.0-3.0 mils
dry. It is permissible and recommended that the top
of the nubs and support ribs in the coolant cavity be
painted.
4.5.3.4 Topcoat: Apply coat of Flame Control TemperKote
1000 paint (Topcoat) to achieve the total topcoat
thickness of 6.0-8.0 mils dry.
4.5.4
Assemble with Gasket Tape
Note: The Pressure Plate (14), Reaction Plate(s) (30) and End Plate
(117) will be referred to as IRON in the following paragraphs.
Refer to Figure 14 for item number references shown in
parenthesis (#).
4.5.4.1 Preparation and cleaning the IRON:
Ensure that the IRON surface is smooth and free of
paint scale, burrs and corrosion. Thoroughly clean
both the inner and outer lands which will receive the
gasket. Use a solvent based cleaner such as acetone,
mineral spirits or a general-purpose wax/oil/grease
remover turning the wipe until it is free of new dark
debris. Finish the cleaning process by blowing off
lint on the sealing surface. If a paint touch-up is
required, reference Figure 10-A to mask the inner &
outer lands that will receive the gasket tape for
sealing.
Caution
Use only clean, dry air for blow-off.
Caution
Follow manufacturer’s instructions and proper safety
precautions for the use of solvent based cleaners
(acetone, mineral spirits or general-purpose) for oil/
grease remover.
4.5.4.2 Preparation and cleaning the Copper Wear Plate:
Ensure that the wear plate surface is smooth and free
of burrs and corrosion. Thoroughly clean both the
outer and inner areas which will be in contact
with the gasket tape. Use a solvent based cleaner
such as acetone, mineral spirits, or a general-purpose
wax/oil/ grease remover. Finish the cleaning process
by blowing off lint on the sealing surface.
Caution
Use only clean, dry air for blow-off.
Caution
Follow manufacturer’s instructions and proper safety
precautions for the use of solvent based cleaners
4.5.4.3 Preparation of the Gasket Tape Ends
Start with the leading end of the gasket tape and
cut the end at 45 degrees per Figure 11. This initial
step is required to insure a smooth transition of the
tape when the tape is overlapped per section 4.5.4.4
(b) below. Also, cut the trailing end of the tape at 45
degrees after it is overlapped per section 4.5.4.4 (b)
below.
4.5.4.4 Applying the Gasket Tape to the IRON
(a)
Start with the sealing area nearest to the inner
diameter on the IRON. Remove the adhesive backing
on the gasket tape a little at a time to prevent the
adhesive from picking up dirt during installation. Start
by positioning one end of the tape at the center-line
of a bolt hole as shown in Figure 9, using the edge of
the water cavity as a guide, as shown in Figure 10-B.
Proceed to apply the tape on the sealing surface
following a smooth circular path, being sure to press
the tape in place.
(b)
After the gasket tape has been placed around the
entire circumference, overlap the starting end of the
end of the tape by a minimum of 0.44” (11.2mm).
See Figure 11. Be sure to smooth the tape at the
overlap transition in order to get a good seal. No air
gaps or bubbles should be present.
(c)
Repeat steps ‘a’ and ‘b’ in Section 4.5.4.4 for the
outer sealing area nearest to the outer diameter of
the IRON, again using the edge of the water cavity as
a guide.