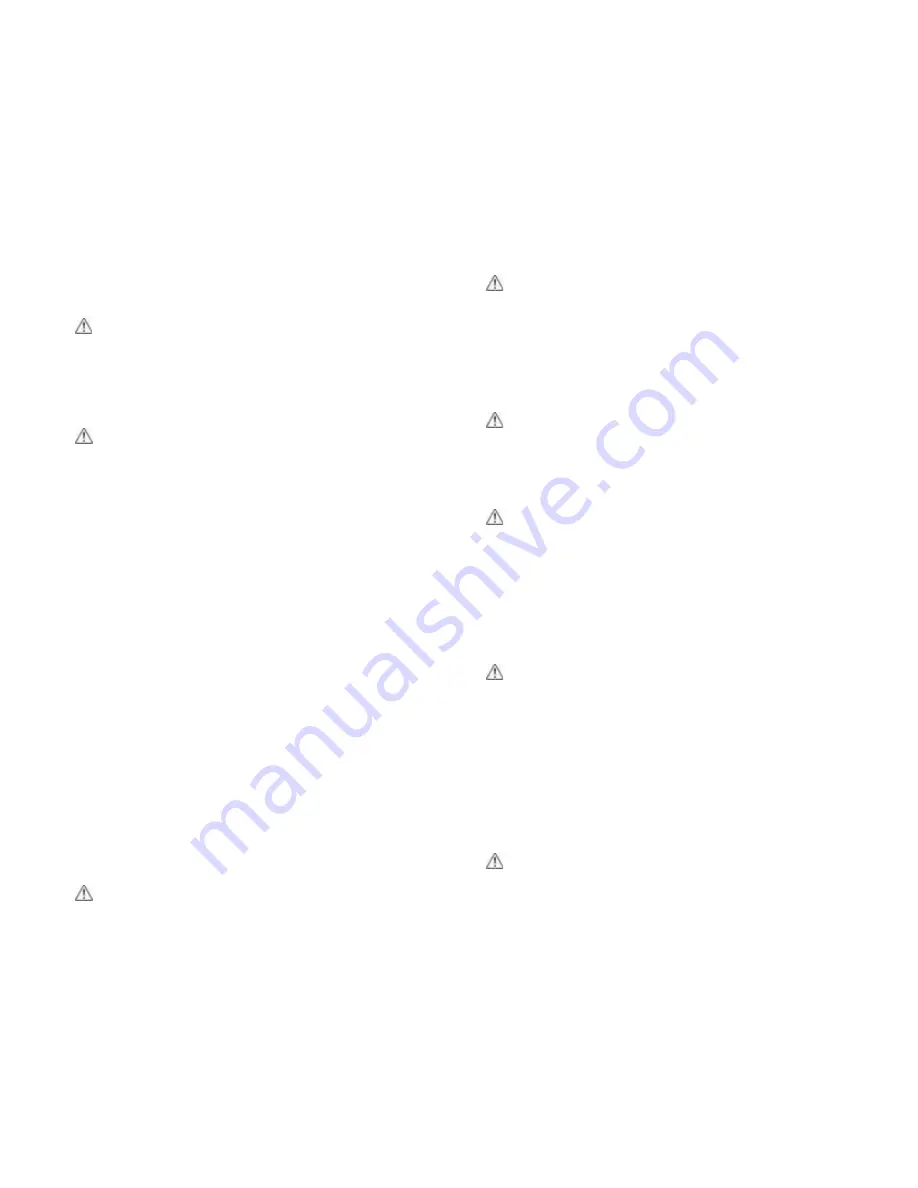
EATON Airflex WSB 11210 WCSB3 Installation Operation and Maintenance E-CLCL-11001-E October 2013
17
3.4.5 Exhausting air pressure from the cylinder (19)
of the spring set brake allows it to engage. Air
pressure within the mounting flange/cylinder (112)
can be exhausted simultaneously with that in the
cylinder (19). For more rapid brake response, exhaust
the air pressure in the mounting flange/cylinder (112)
after engaging the spring set brake.
Note: The spring set brake is intended for parking or
emergency braking only.
Warning
Dynamic braking with the air cooled, spring set brake
is not recommended except for emergency stopping
situations or during initial wear-in. High heat generat-
ed during dynamic braking can result in damage or
failure of the brake components.
Caution
Rapid engagement of a fully released tensioner/brake
could result in pressure spikes within the coolant
cavities and subsequent leakage.
3.5
Periodic Maintenance
3.5.1 As the friction material wears, adjustment of the
brake may be required to keep pistons and cylinders
within the proper stroke range. See the MAINTEN-
ANCE section for wear adjustment procedures and
component wear limits.
3.5.2 Periodically check for external air leakage in the area
of the piston seals (21) (23) in cylinder (19) and
mounting flange/cylinder (112) and internal leakage
across the dual pressure piston seals (114) in
mounting flange/cylinder (112). For replacement, refer
to procedures in Section 4.0, Maintenance.
3.5.3 Moisture that may accumulate in the brake cylinder
can be purged on size 36WCSB3 units. With air
pressure exhausted from the cylinder, remove the
pipe plug (105) at the 6 o’clock position on the
cylinder, and apply low air pressure to assist in
expelling any excess moisture. After draining the
cylinder, reinstall the pipe plug, applying a pipe thread
sealant on the threads prior to installation.
Caution
Applied air pressure greater than 10 psi (0.68 bar)
should not be used when draining the cylinder. Use
adequate shielding to avoid contact with direct spray
from moisture being purged from the cylinder.
3.5.4 Periodically observe the rotating discs while the
tensioner is fully released. Dragging discs may be
caused by wear or contamination of the gear or disc
splines, lack of spline lubrication, disc imbalance,
warped discs, or misalignment. Correct as required.
3.5.5 Pneumatic and electrical control interlocks should be
periodically checked for proper settings and
operation.
3.5.6 If leakage or blockage of any water-cooled chamber
is suspected, a static or dynamic test may be
performed as follows:
3.5.6.1 Static Pressure Test:
a)
Release the spring set brake by applying the proper
air pressure.
Warning
Ensure that the machinery will remain in a safe posi-
tion prior to releasing the brake.
b)
Bleed all air from within the coolant cavity. Air
bleeding must be accomplished by running coolant
through the cavity with the tensioner secured in its
proper operating position.
Caution
Bleeding air from each coolant cavity will require iso-
lation of the drain ports. When static test is complete,
all isolation shall be removed to maintain full
flow through the system.
Warning
Removing any hoses for isolation of the supply or
drain ports will require a compatible fitting for the
ORB porting. Failure to do so will damage the porting
and cause leakage, a loss of flow and possible dam-
age to the tensioner.
Note: Avoid contaminating the friction material with
coolant or water.
Warning
Contamination of the friction material could result in
erratic or loss of torque.
c)
After the air has been removed, install pipe plugs in
the outlets and apply maximum allowable coolant
pressure measured at the inlet to the water cavity.
Maximum allowable is 40 psig (2.8 bar) for size
36” units. Maintain this pressure for 30 minutes.
Check for leakage at all O.D. and I.D. wear plate
sealing areas.
Caution
Be sure to apply and retain air pressure to the cylin-
der (19) of the tensioner to release the spring
pressure on the tensioner / brake during static coolant
pressure testing. Engagement of the brake during
testing could develop surge pressures exceeding the
maximum allowable within the coolant cavities result-
ing in possible damage to the seals.
3.5.6.2 Dynamic Flow Test:
a)
Dynamic flow testing of the tensioner should
be conducted at the required flow rate for the rated
HP dissipation and coolant quality, as given in Table
8. Inlet and outlet pressures for the appropriate
tensioner size should not to be exceeded.
WCSB3 Brakes