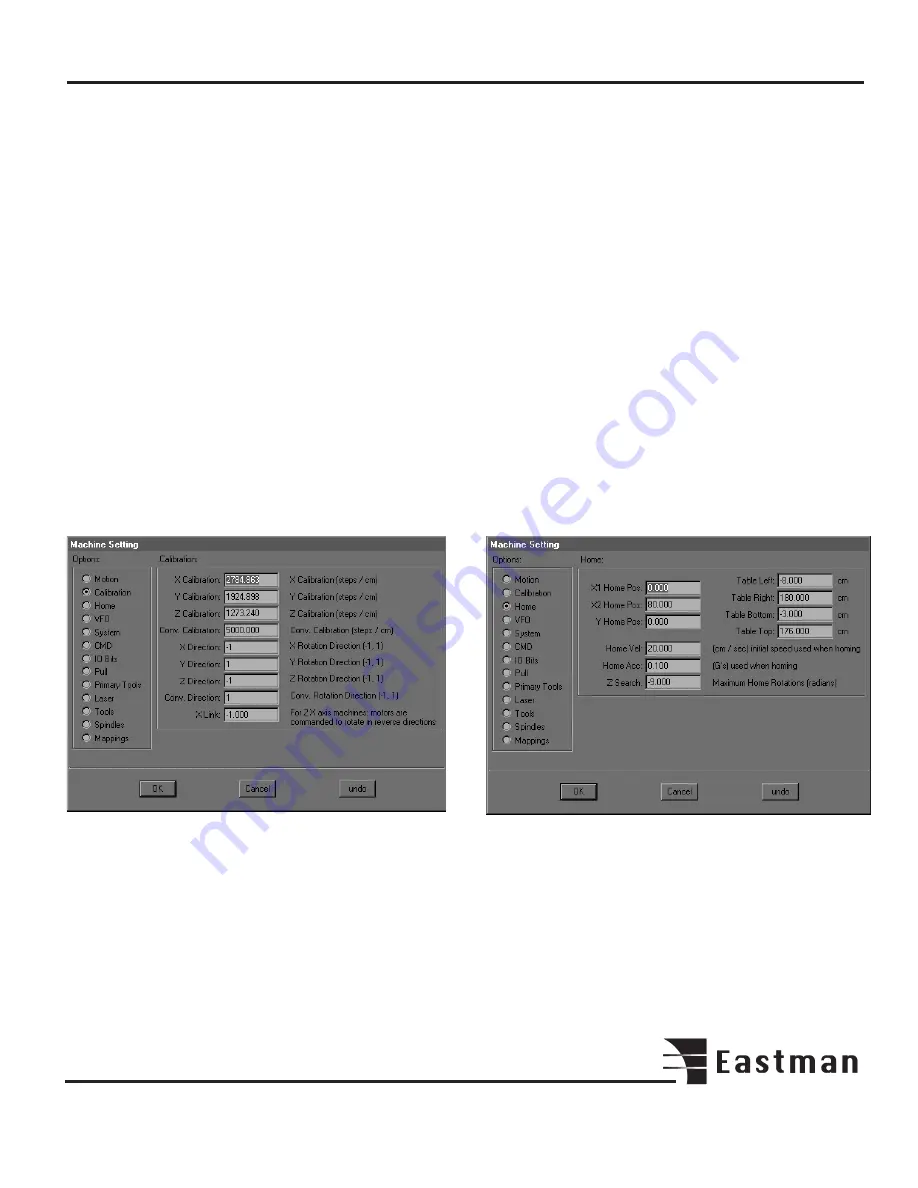
15
®
Jog Accel: Controls acceleration of the plotter while manu-
ally jogging it with the joystick or the arrows on the keypad.
This setting is a multiplier of the acceleration value in Accel
G. For example, if Accel G is .4 and Jog Accel is .8, the jog
acceleration will be .4 times .8, or .32.
Jog Decel: Similar to Jog Accel but controls motion of the
plotter after the joystick or keypad arrow is released.
Limp Velocity: This is the maximum velocity of the ma-
chine while in limp mode. Limp mode is toggled on and off
by the Jog key on the keypad.
Z Velocity: Maximum rotational velocity for the cutting (mark-
ing, notching, etc.) devices. Radians per second.
Z Accel: Rotational acceleration for cutting devices. Ex-
pressed in radians/sec/sec.
Z Home Vel: Sets the rotational velocity for the machine’s
table home, table zero, and panel zero functions. This num-
ber is normally much lower than the Z Velocity. Expressed
in radians per second.
The Machine Setting Calibration screen.
X Calibration: Controls the accuracy of the plotter in the X
axis. Expressed in steps per centimeter, this variable will
be preset from the factory and should not need adjustment.
A greater number will cause the computer to output more
steps to travel one centimeter, causing inaccuracy in the
length of cut panels. The correct number for this calibration
may be determined from the machine’s gear ratios or by
measuring the distance the machine travels compared to
the distance it was commanded to travel in a file or by jog-
ging.
Y Calibration: Operates the same way as the X calibra-
tion.
Z Calibration: Operates in the Z axis and is specified in
radians.
X Direction: Determines the rotational direction of the X
motor. This may only be set to -1 or 1. This is preset at the
factory and should not be changed.
Y Direction: Operates the same way as the X Direction.
Preset at the factory and should not be changed.
Z Direction: Operates the same way as the other axis di-
rection settings. Should not be changed.
X Link: This setting is for dual X-motor machines. When
two motors are used to drive the machine on the X axis (for
instance, in most M9000 machines), they must be com-
manded to rotate in opposite directions. Under no circum-
stances should this setting be changed.
The Machine Setting Home screen.
X1 Home Pos: Specifies an offset in cm. from the X1 home
switch. X1 Home Pos is used only on twin motor X drive
machines such as the M9000. In conjunction with X2 Home
Pos, it is used to square the machine to the table. The
machine’s position resulting from the homing sequence with
these numbers is regarded as the table’s X-axis origin (0.0)
Содержание ETS-SLS-2
Страница 1: ......
Страница 24: ...24 Notes ...
Страница 25: ...25 Notes ...
Страница 26: ...26 Notes ...
Страница 28: ......