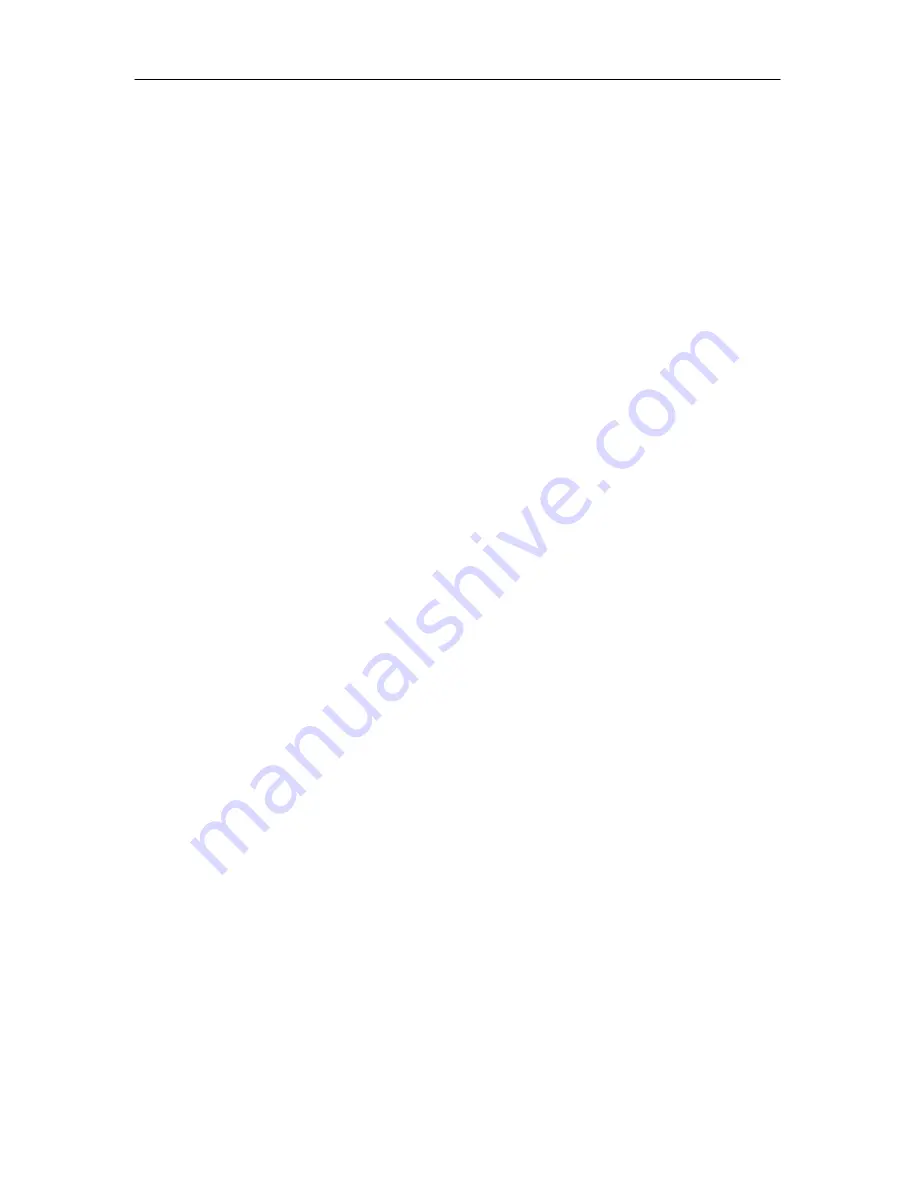
22
b)
Repeat the process for all the sensors mounted below the transfer chain. For our
example we’ll say the average distance, or ‘Bottom Preset’ value is 22”.
c)
Pass a calibration profile bar of known thickness through the scanner.
d)
For each top mounted sensor, read the spot buffers of each laser and calculate
the average range reading for the entire width of the calibration bar. Compare
the result with the ‘Top Preset’ value less the calibration bar's known thickness to
determine the range offset necessary for that spot.
d)
Repeat the same process for each spot of lower mounted sensors except that
the comparison is only between the ‘Bottom Preset’ value and the range reading.
For example using a calibration bar that is 1.875” thick, if average reading for a top
sensor laser spot is 21.00” then the range offset for that laser spot would be calculated
as:
Top ‘Preset’
-
Calibration Thickness - Average Spot Reading = Range Offset
23.000"
-
1.875”
- 21.000”
= 0.125”
If the bottom sensor laser spot’s average readings were 22.125, then it’s offset would be:
Bottom ‘Preset’ - Average Spot Reading = Range Offset
22.000"
- 22.125”
= -0.125”
6.2 Design Recommendations
A generic scanner frame design with dimensions is included for a guide to the critical
dimensions. This is the basis for a frame design and it is recommended that the OEM
individualize the design to match their application and existing equipment. Some points
to consider are:
6.2.1 Sensor Mounting
When designing the scanner frame, it is preferable that the design mounts the sensors
on the downstream side of the frame so that any debris travels away from the sensors.
Sensors are generally mounted with the first laser line 1" to 3" inside the 'zero lumber
line' to ensure that the first laser spot will always see a target.
For edger and cant optimizer applications where pins are used to skew and offset the
piece, the skew pins should be aligned as close as possible to a laser spot to measure
board/cant edges at the pin location guaranteeing skew and offset position.
If any of the lasers are detected on a chain or support structure then make note of which
laser and which sensor this occurs on. Any lasers hitting chains must be physically
blocked at the laser windows otherwise they will generate data errors.
6.2.2 Baffle Plates
It is highly recommended that a “baffle plate” design be used to limit where a laser beam
spot is projected, or the viewing area of the sensor’s cameras. This reduces the
possibility of errors in the readings.
Typically a “baffle plate” design is nothing more than a ½” slot cut in a plate and
mounted in front of the sensor with the slot running lengthwise from laser 0 through 7
(~22”, allowing for alignment and machining tolerances). To accommodate different
standoff distances, two designs of baffle plates may be required (or a single style with a
flexible mounting offset to the scanner frame).
Содержание B Series
Страница 1: ...B Series B800 Sensor Version 5 1 4 4 ...
Страница 12: ...12 3 4 Dimensions 1 ...