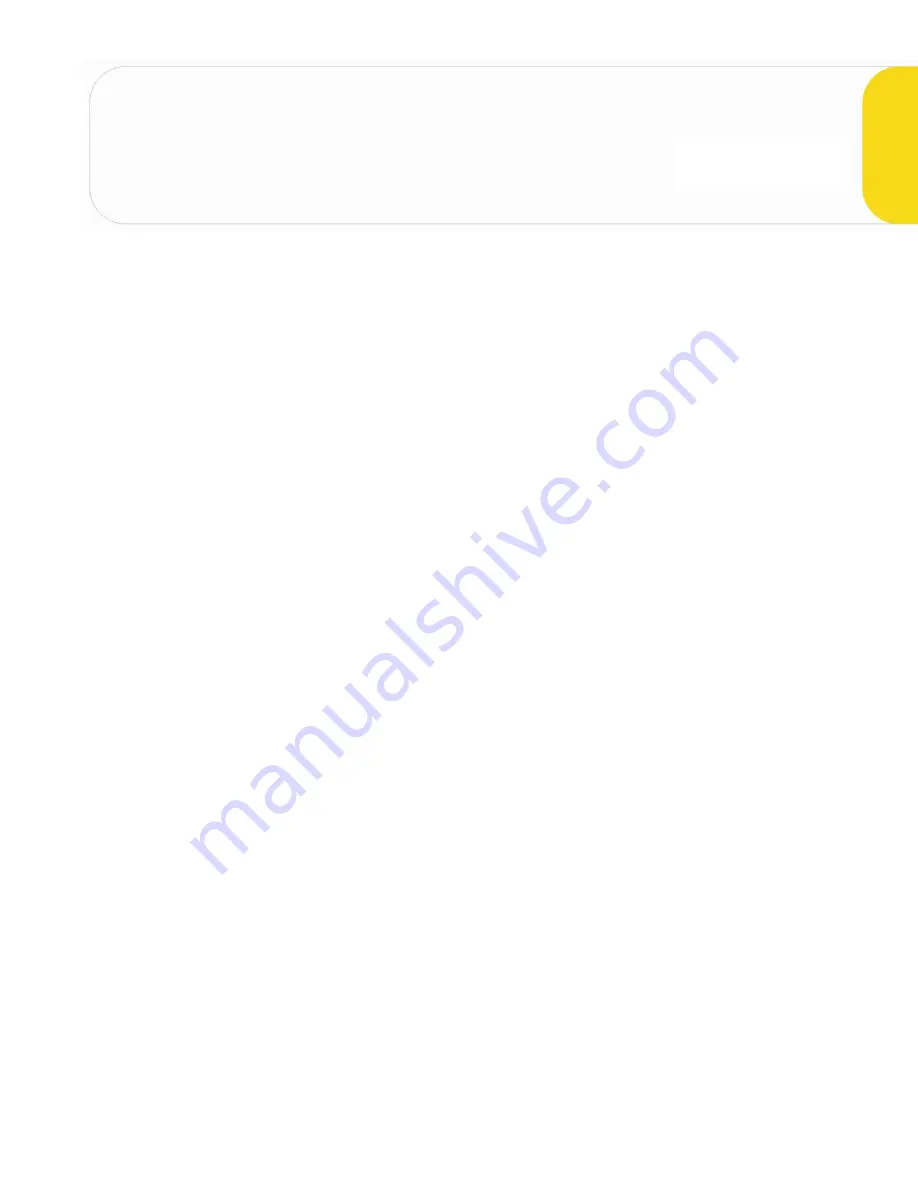
Section 6
6 OEM Design
6.1 Design Requirements
6.1.1 System Calibration
Once all the sensors have been mounted in the scanner frame, two calibration
calculations need to be performed. While the two calculations are described separately
below, the recommended procedures for each calculation are the same and may be
combined into one calibration sequence. The purpose of these calculations is to provide
the necessary data for optimizers to transform individual range readings into a global
frame of reference.
6.1.1.1 Determine Laser Alignment Offset/Delay
The first of the two calibration calculations compensates for the variations in laser
placement that result from sensor mounting and manufacturing variations of the frame in
the direction of a target transfer. These alignment variations need to be taken into
account in order to align the data obtained during a target scan in time (z – axis).
The calibration routine needs to determine the offset/delay values in encoder pulses
resolution for all the lasers on the scanner frame referenced to a common ‘zero’ plane in
the direction of travel. The recommended method, which guarantees that the readings
are taken from the same location, is to run a straight 2"x4" profile bar through the
scanner and then examine the scan buffers.
During the calibration process, an offset value of 0 is used when reading the scan
buffers. The number of blank (out of range) entries in each of the buffers corresponds to
the offset value for that buffer. It is crucial that the profile bar used for calibration is
straight; this ensures that the buffer offsets determined here will properly align the data
obtained in subsequent board scans.
Later, the application software applies these offset values while reading spot buffers
resulting in proper data alignment at every laser position.
6.1.1.2 Determine Range Offset
The second of the two calibration calculations addresses the variations in range above
or below the item being scanned. It also determines how the top and bottom halves of
the model data join together when the viewing areas of opposing sensors overlap.
The recommended method for determining range offsets requires a few steps:
a)
Measure the distances of all the top mounted sensors to the top of the transfer
chain, then average the results to determine a ‘preset’ value. For our example
we’ll say that the average distance from the face of the top mounted sensors to
the top of the transfer chain, or ‘Top Preset’ value is 23”.
Содержание B Series
Страница 1: ...B Series B800 Sensor Version 5 1 4 4 ...
Страница 12: ...12 3 4 Dimensions 1 ...