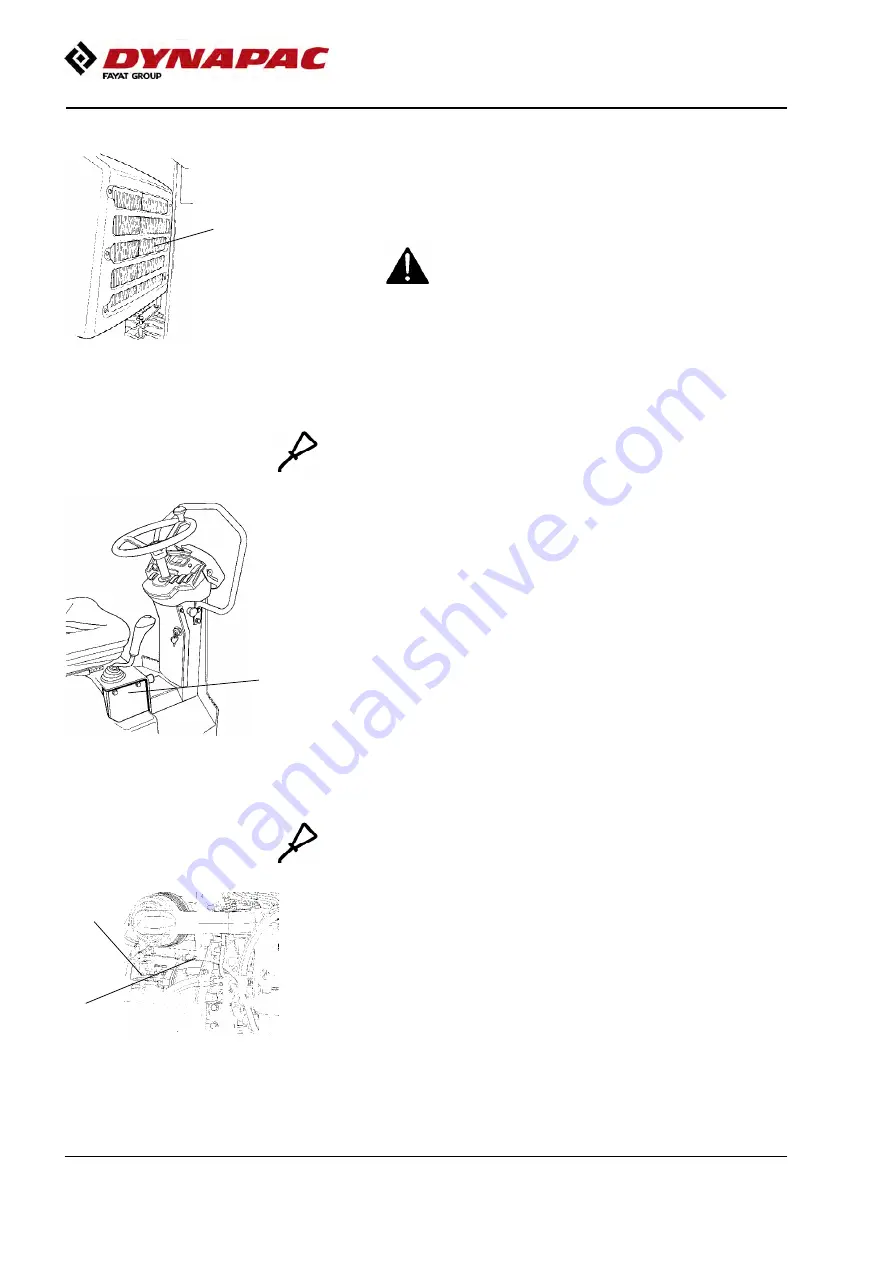
Maintenance measures - 250 h
4812160801_D.pdf
2018-12-17
Hydraulic fluid cooler - Cleaning
Fig. Engine compartment
1. Hydraulic fluid cooler
1
Clean the hydraulic fluid cooler’s cooling flanges,
ideally with compressed air. Blow the cooler clean by
blowing air from the inside outwards.
Wear gloves and eye protectors when working
with compressed air.
Wear gloves and eye protectors when working
with compressed air.
Forward/Reverse controls and joints - Check
and lubrication
Fig. Forward/Reverse lever
1. Plate
1
Remove the plate (1). Check the friction of the
forward/reverse controls. The friction screws should be
set so that the forward/reverse lever remains in the
position in which it is set whilst the machine is
operated. The control’s ‘0 position’ is determined by a
screw which engages with the groove on the shaft
between the controls.
If the control begins to be stiff after a longer period of
use, lubricate the controls by the bearings and the
control cable with a few drops of oil.
Fig. Engine compartment
1. F/R-control cable
2. Propulsion pump
1
2
If the forward/reverse lever still is stiff after the above
adjustments, lubricate the other end of the control
cable with a few drops of oil. The cable is located on
the top of the propulsion pump.
82
Содержание CC1000
Страница 2: ......
Страница 12: ...Introduction 4812160801_D pdf 2018 12 17 4 ...
Страница 20: ...Special instructions 4812160801_D pdf 2018 12 17 12 ...
Страница 28: ...Technical specifications 4812160801_D pdf 2018 12 17 20 ...
Страница 54: ...Operation 4812160801_D pdf 2018 12 17 46 ...
Страница 64: ...Operating instructions Summary 4812160801_D pdf 2018 12 17 56 ...
Страница 66: ...Preventive maintenance 4812160801_D pdf 2018 12 17 58 ...
Страница 70: ...Maintenance Lubricants and symbols 4812160801_D pdf 2018 12 17 62 ...
Страница 77: ...Maintenance Maintenance schedule 4812160801_D pdf 2018 12 17 Service Checklist 69 ...
Страница 78: ...Maintenance Maintenance schedule 4812160801_D pdf 2018 12 17 70 ...
Страница 86: ...Maintenance 10h 4812160801_D pdf 2018 12 17 78 ...
Страница 116: ...Dynapac Compaction Equipment AB Box 504 SE 371 23 Karlskrona Sweden www dynapac com ...