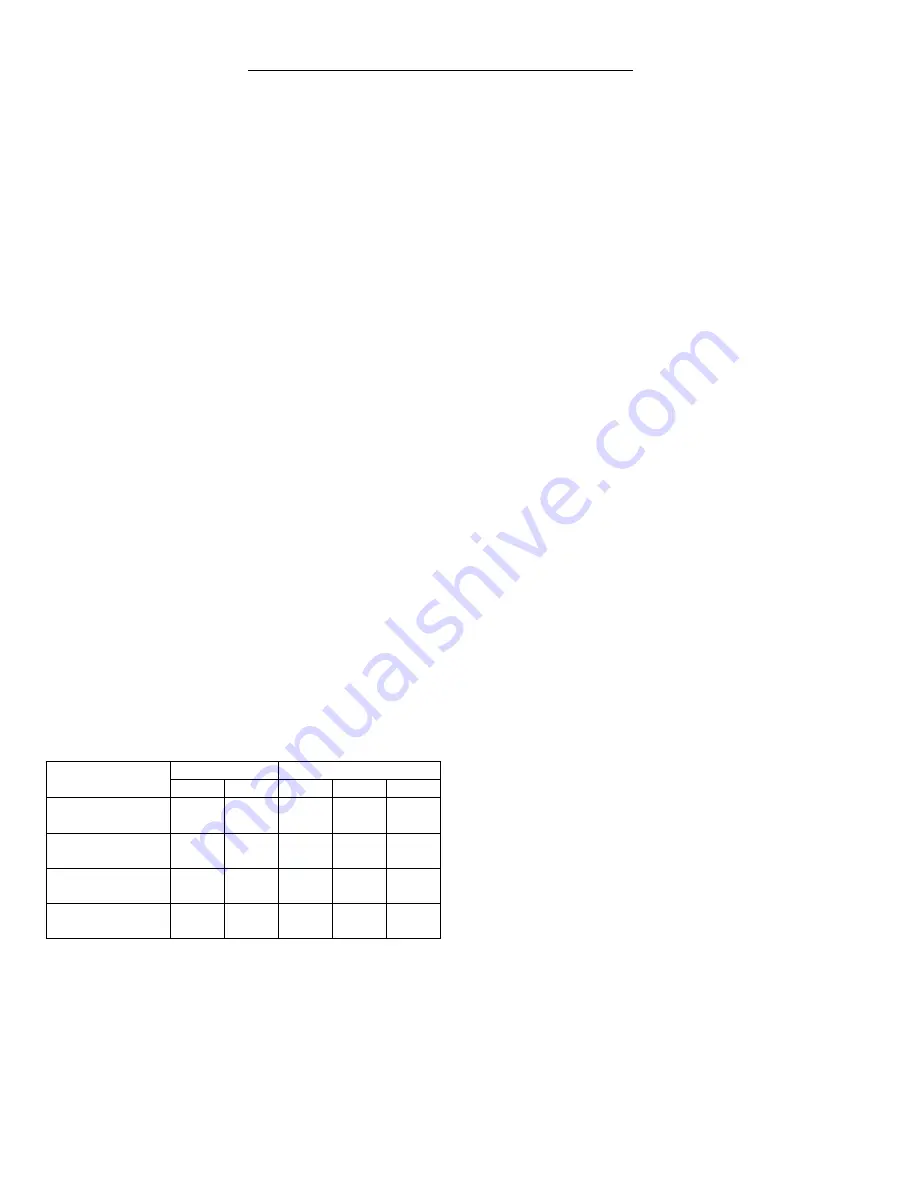
8
CES STAMPING PRESS CONTROLLER DESCRIPTION
CONSTRUCTION
The CES Stamping Press Controller is a solid state,
closed loop velocity controller designed specifically for
use with Dynamatic® eddy-current press drives. The
controller is built with analog, digital and microprocessor
circuitry. All components of the CES Controller are
contained on a sub-panel, except for an autotransformer
that is mounted separately. The panel measures 74" by
31.25". Special sizes are made to order upon request.
CES CONTROLLER
The basic CES press drive controller has proven to be
readily adaptable to synchronization (position) control.
This system utilizes a position transducer (digital shaft
encoder) to measure press position (crank angle) and
compares this feedback information against a digital
position reference. All information is handled in parallel
digital form and has a minimum sample rate compatible
with the system.
The difference between the reference and the feedback
signal (position error) is translated to an analog signal in
a D-A converter. The analog signal is sent to the press
velocity control for final processing and power
amplification for press drive control.
The CES controller is easily applied to single or multiple
action presses where speed control is desirable. The
system offers many unique features not available with
other press drive designs for use on draw presses,
banking presses, transfer presses and on synchronized
presses with automated handling equipment. The
combination of the eddy-current package press drive
and the CES controller offers a simple, safe, low
maintenance and reliable drive system to do a wide
variety of the jobs required of modern production press
equipment.
Specifications
Mechanical
49 -
37 -
Unit
63
42
42
32
21
Input Current
Aac Max
137
91
72
54
35
Input Current
Aac Average
98
65
53
40
26
Clutch Current
ADC
180
120
96
72
48
Brake Current
ADC
90
60
48
48
24
Retrofit control for existing presses have different
specifications from those listed here. Check your
specific unit or contact the factory.
Input Voltage: 480 VAC, +10%, -15%, 60Hz
Output Voltage: 850 VDC Field Forcing
Clutch Duty Cycle: 70%
Brake Duty Cycle: 30%
POWER CIRCUITRY
The incoming three phase 480 VAC connects directly to
the circuit breaker or terminal block at the top of the
panel. 120 VAC power for control circuitry, I/O modules
and the power supply board is provided by transformer
T1. Fuses FU5 and FU6 protect T1 against short circuits
and internal grounds. Capacitors C3, C4 and C5, along
with the impedance of the autotransformer, serve to filter
the incoming power to prevent line noise from affecting
the controller and to reduce line disturbances by the
controller. The autotransformer steps up the line voltage
from 480 VAC to 600 VAC. FU1, FU2 and FU3 are fast
acting semiconductor fuses sized to prevent damage to
the SCR’s in the event of an output short circuit. All
three incoming lines are sensed at the clutch gate driver
board and fed back to the logic board for proper gate
signal synchronization, and ultimately to the DMR
(Digital Master Regulator) for the purpose of ensuring
safe limits. The line voltage may be read on the DMR
display to be discussed later.
Separate contactors for the brake and clutch sections
provide positive mechanical disconnects from the input
power. Each section consists of a full converter
composed of six SCR’s capable of forcing the 300 VDC
rated coils to a peak value of 850 VDC, as well as
causing current flow to cease by inverting or by applying
a negative 850 VDC to the coils. Separate brake and
clutch gate driver boards supply the gate signals to the
appropriate SCR’s; they are located on the left side
bracket. Each SCR has di/dt protection from a series
choke and dv/dt protection from snubber networks
located on the circuit boards, which consist of series
resistors, capacitors and diodes connected in parallel
with the SCR. Also, across each SCR is a Metal Oxide
Varistor (MOV) for transient voltage protection.
A minimum resistive, or latching, load is provided with a
power resistor across each dc bus, identified as C1-C2
and B1-B2. Each bus also has an MOV suppressor to
clamp any high voltages arising due to the inductance of
the coil loads and to provide a current path for the short
period of time between interruption of current (such as a
contactor opening), and the establishment of current flow
in the C phase SCR's by the free wheel gates. Clutch
and brake voltages are fed back to the logic board
through the brake gate driver board. The output leads
are routed through L1 and L2, which are isolated current
feedback sensors with the current signals going directly
to the logic board. The output leads terminate inside
and near the bottom of the logic door.
The CES stamping press controller provides control for
the full range of Dynamatic® eddy-current press drives.
The power conversion circuitry operates from 480 VAC
input and provides a maximum of 850 VDC coil
excitation voltage.
Содержание CES
Страница 7: ...7 ...
Страница 37: ...Page is intentionally blank ...