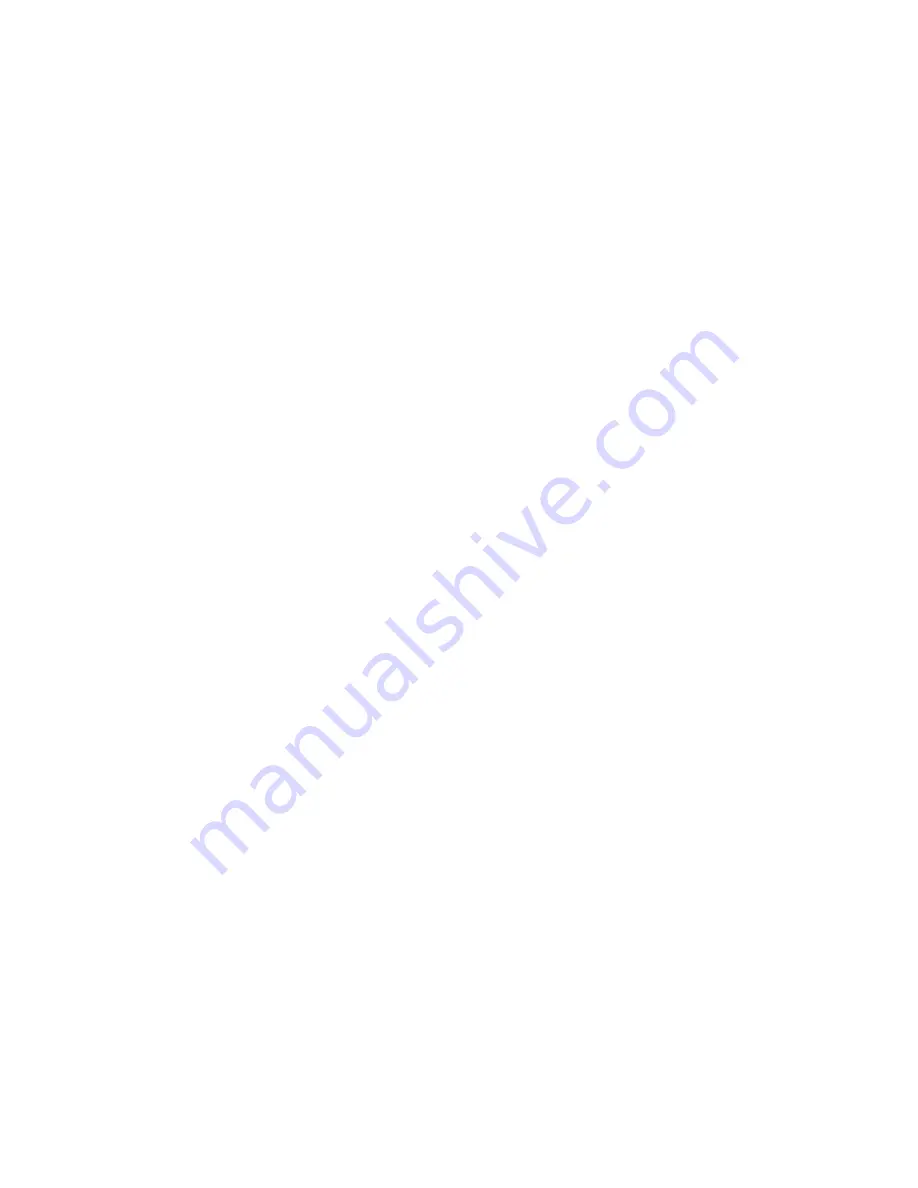
30
START-UP AND ADJUSTMENT
This controller replaces the present Dynamatic Analog
CES Press Control in all aspects and adds numerous
diagnostic features. This design replaces discrete
analog and digital control circuitry with microprocessor-
based operation where advantageous.
POWER CONVERSION
The CES Press Control provides control for the full
range of Dynamatic press drives the power conversion
circuitry operates from 480 volts (+10%, -15 %) input
and provides a maximum of 850 volts dc coil excitation
voltage. The following maximum current levels are
available:
1. Clutch Excitation - provides 180 amps at 70% duty
cycle.
2. Brake Excitation - provides 90amps at 30% duty
cycle.
Refer to the power schematic for your press drive for the
following discussion. Both the clutch and the brake
power-sections consist of rectifier circuits to convert the
ac line power to dc power. Each circuit employs a full
wave bridge rectifier consisting of six SCRs and resistor-
capacitor networks for suppression. There is a clutch
contactor and a brake contactor for electromechanically
disconnecting the clutch and brake respectively. There
are three-line fuses and a circuit breaker for over-current
protection. An autotransformer steps the 480-volt line
voltage up to 600 volts for the required forcing voltage.
The clutch gate driver and brake gate driver printed
circuit boards provide isolation and amplification of the
SCR firing pulses.
PRESS SPEED CONTROL
The press control provides closed loop speed control
operation with inner current loops on both the clutch and
brake. It provides adjustable acceleration and
deceleration. The reference data is modified by a press
angle measuring and control circuit function that will
change the reference at adjustable angles.
The logic circuitry is located on printed circuit board
assembly number 15-822-1, through 15-822-10,
depending on the size of the mechanical unit. This
board has circuitry that performs the following functions:
1. Compares the reference voltage to the speed
velocity voltage. The difference is used to fire the
SCRs that provide the power required to maintain
the set speed.
2. Limits the clutch current to a value equal to the
rating of the mechanical unit.
3. Limits the brake current to a value equal to the rating
of the mechanical unit.
4. Provides adjustable velocity damping to the clutch
circuitry.
5. Provides adjustable velocity damping to the brake
circuitry.
6. Provides clutch "free wheel" command signals to
prevent damage to the clutch SCRs.
7. Provides brake "free wheel" command signals to
prevent damage to the brake SCRs
8. Control amplifiers that compare the clutch and brake
current reference signals to current feedback
signals.
9. Phase shifter microprocessors in the clutch and
brake circuit, which control the firing angles of the
clutch and brake amplifier SCRs.
ANGLE MEASURING AND CONTROL CIRCUITRY
The CES press control provides a means of measuring
press angles by utilizing a position resolver mounted on
the output press gearing (the crank shaft of the slide).
The position information is used to set a reference profile
based on stored data of up to 6 angles and 6
predetermined speeds.
The control digital board is a microprocessor-based
solid-state control system capable of receiving data from
the press control, storing it, and then using it to provide
reference speed signals to the CES control.
START-UP PROCEDURE
Use a digital multimeter (such as a Fluke 8010A) with
1% or better accuracy for all measurements required
during start-up.
1. Turn the circuit breaker to the OFF position. Turn all
incoming signals OFF.
a. Check all terminal screws for tightness.
b. Make certain that All plugs are properly seated.
c. Check for loose connections.
d. Set potentiometers as follows.
1) Clutch Velocity Damping 50%.
2) Clutch Current Damping 50%.
3) Brake Velocity Damping 50%.
4) Brake Current Damping 50%.
e. Install a jumper from 300 to 302. This will allow
115 volts to be present in the CES press control
when the circuit breaker is placed in the ON
position.
2. Turn the circuit breaker to the ON position.
a. Check for the presence of 115 volts on the
secondary of the control transformer.
b. Check the power supplies for their voltages (+/-
0.5%) of -12 VDC, +24 VDC, +12 VDC
α
+5
VDC.
c. Check the line voltages LA-LB-LC for the
presence of 600 volts, +/- 10%.
Содержание CES
Страница 7: ...7 ...
Страница 37: ...Page is intentionally blank ...