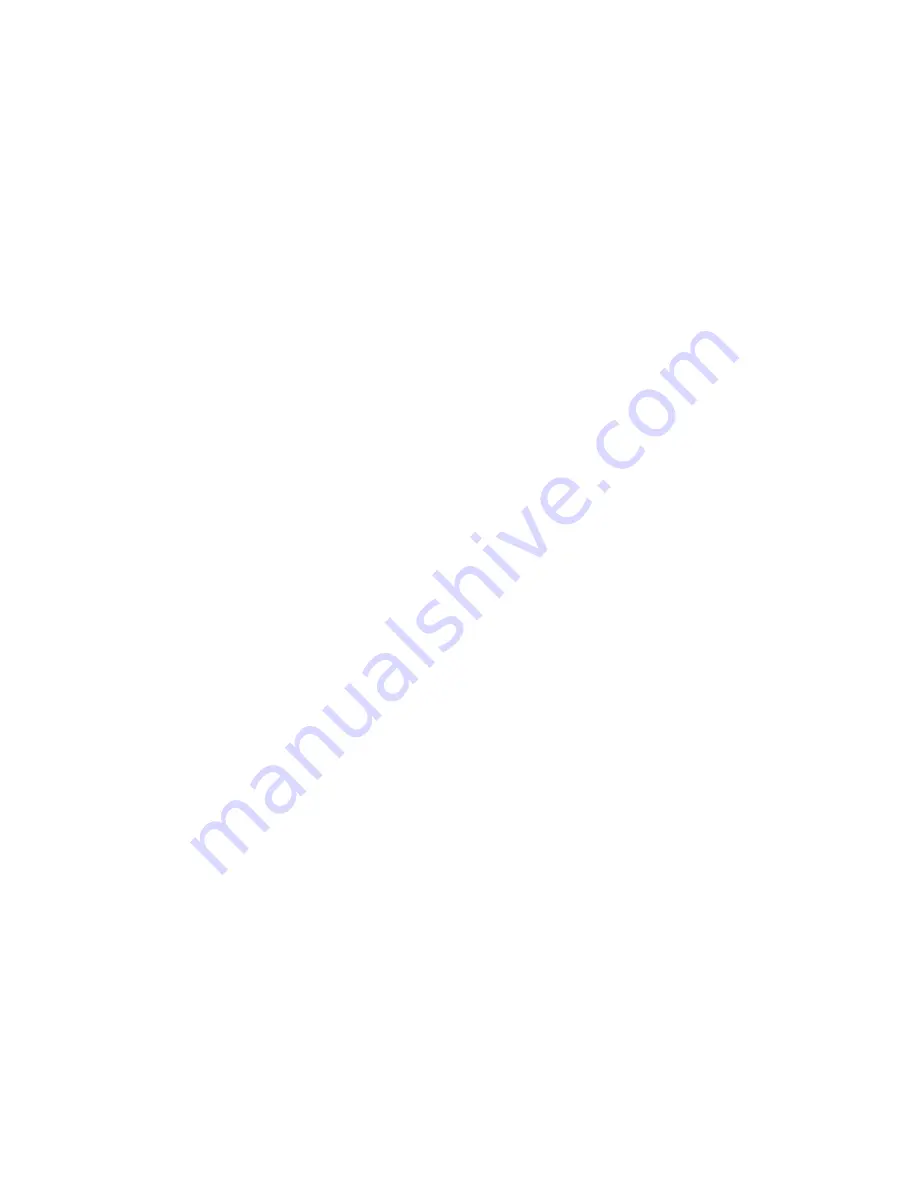
21
OPERATION
PURPOSE
The CES Stamping Press Controller is easy to operate.
We believe that some knowledge of how the controller is
supposed to function will help you obtain the best
performance with minimum down time. Knowing how it
works will also help you troubleshoot any problems that
may arise. Before applying power to the controller, we
suggest that you read this section.
CONSTANT ENERGY SYSTEM
The Constant Energy System (CES) is an advancement
in metal forming press drive systems employing an
eddy-current clutch and brake in place of friction devices
and utilizing the eddy-current clutch as an adjustable
stroking rate drive. The name, Constant Energy System,
is derived from the physical arrangement of the
components of the system; the flywheel of the eddy-
current drive is coupled to a constant speed motor.
Therefore, constant kinetic energy is maintained in the
flywheel. The CES press drive has proved itself capable
of speed controlling large stamping and draw presses
over wide speed ranges. It is also readily adaptable to
synchronizing or position controlling several presses.
The CES control system is infinitely variable throughout
its speed range of 10:1. It is capable of precise position
control; such as in very slow inching for die setup. Input
flywheel size and motor horsepower affect system
performance at low output speeds and maximum loads.
Thus, proper sizing of the press drive for the specific
operating speed range of your press application is an
important factor.
STAMPING PRESS OPERATION
Stamping presses generally employ either 5 to 8% or 8
to 13% high slip ac motors belted to a flywheel, a friction
clutch and brake, and press gearing that drives the press
crank shaft. DC motors have also been used for this
purpose. One critical part of a modern mechanical press
is the overworked clutch and brake units. The function
of the clutch is to deliver torque from the flywheel to the
crankshaft for the working of metal. If the press is single
stroked, the clutch must accelerate the gears and other
rotating members from zero to full operating speed, and
also transmit the required working torque. The brake
must decelerate the rotating parts in order to stop the
slide. The many types of clutch and brake units built by
various press builders and their suppliers can all be
classified in one of the following categories: 1) Positive
clutch and brake; 2) Friction clutch and brake; and 3)
Eddy-current clutch and brake.
EDDY-CURRENT CLUTCH AND BRAKE
The eddy-current clutch and brake unit is basically a
press drive utilizing the eddy-current principle to transmit
and control the required crank torque. The drive
consists of a flywheel, belt driven by a high slip ac
induction motor, an eddy-current clutch rotor and a brake
rotor assembly directly connected to the press drive
shaft.
Driving torque is developed through an electromagnetic
force between the flywheel and clutch rotor. Braking
torque is developed through a similar force between the
stationary brake field assembly and the brake rotor.
Electromagnetic coils in the flywheel or brake field
assembly are energized to establish a magnetic field that
cuts through the surface of the clutch and brake rotors.
Relative motion between the clutch rotor and the clutch
field poles, or between the brake rotor and brake field
poles, causes a cutting action of the magnetic flux at the
rotor surface, which in turn generates eddy-currents in
the drum. Torque transmitting magnetic action is then
induced between the clutch rotor and flywheel member,
or between the brake rotor and brake field member. The
degree of clutching or braking action is controlled by
varying the magnitude of the current fed to the coils.
Since the eddy-current brake does not develop any
torque at zero rpm, a friction brake is used as a holding
brake. This brake must be large enough to be capable
of stopping the press in an emergency, such as a power
failure.
VARIABLE SPEED PRESS DRIVES
The package press drive consists of an integral flywheel,
air-cooled, eddy-current clutch and brake in a
standardized, interchangeable package design. With the
advent of high-power capability electronic components, it
became possible to build a high-performance speed
control capable of maintaining set speed of the package
press drive anywhere within the mechanical press
drive's speed range. Since the flywheel is directly belted
to the main drive motor and run at a constant speed, it
has a fixed level of energy available for transmission to
the work through the eddy-current clutch.
The press drive can be geared to the highest press
running speed. Since the primary mass is the flywheel,
and the output member has relatively low inertia, the
press drive is capable of varying its running speed
during different portions of a single stroke. The press
can approach the work at high speed, slow down just
prior to hitting the work, go at optimum metal working
speed and complete the stroke at high speed. The end
result is more parts per hour.
The heart of the CES stamping press controller is the
CES Controller. Its purpose is to provide high response
velocity control. It is adaptable also to position the slide
where line synchronization is desirable. The basic CES
controller is a high field forcing speed device using
closed loop control.
In a closed loop controller, a portion of the output signal
is fed to the feedback network and then to a summing
junction in opposition to a reference signal. If there is a
difference between the feedback and reference signals,
the resultant error signal is used for controlling the
output speed. One closed loop system is used for
Содержание CES
Страница 7: ...7 ...
Страница 37: ...Page is intentionally blank ...