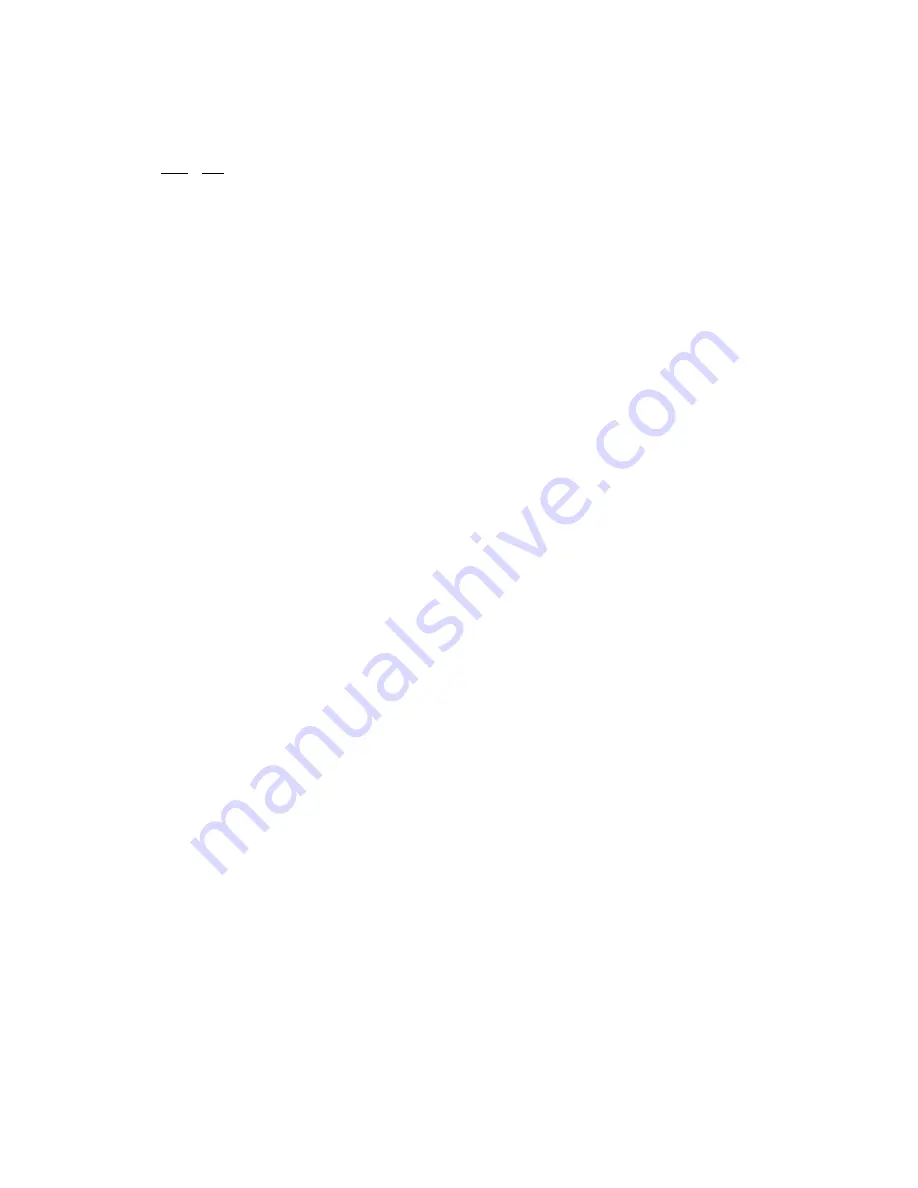
32
the size of the mechanical unit, +/-1 amp. Adjust
the Brake Current Limit potentiometer only if
necessary for the proper Amps.
d. To return the brake current to zero:
1) Press the down arrow (↓).
2) "62 br OFF" will appear in the bottom
row of the display.
WARNING: Note that if the brake current is left
ON for more than the setting of the Brake
Current on Too Long Fault, a brake current fault
will result, and it will take ten minutes before the
fault can be reset
7. Note the following test mode faults:
a. Receiving an enable in the test mode will result
in an enable in the test mode fault.
b. Sensing press movement in the test mode will
initiate a press movement in the test mode fault.
8. Turn the CES circuit breaker OFF.
a. Remove all of the jumpers added during this set-
up. The main motor should remain OFF.
9. Turn the CES circuit breaker ON.
a. The DMR will be in the test mode.
b. To exit the test mode:
1) Press the Top key. This will activate the top
row of the display.
2) "60 ON" will appear in the top row of the
display.
3) Press the down arrow.
4) "60 OFF" will appear in the top row of the
display.
c. Send the following signals from the press control
to the CES controller. Remove the signal after
making the prescribed check. When faults are
simulated, send the fault reset signal from the
press control to reset the CES controller.
1) Inch - Check for presence of LED on I/O
board and on the keypad and display board.
2) Micro Inch - Check for presence of LED on
I/O board and on the keypad and display
board.
3) Reverse – Check for presence of LED on
I/O board and on the keypad and display
board.
4) Stop-On-Top - Check for presence of LED
on the I/O board
5) Clutch Contactor ON and Enable - Check for
presence of comparable LEDs on the I/O
board. Since the motor is not running, an
under-speed fault will result, and a stop-on-
top fault will be generated. Check this LED
on the I/O board. Since the press is not
rotating, it will not get to the creep angle or
the stop angle; therefore, a stop now fault
will be generated. Check this LED on the
1/0 board.
6) Send the clutch contactor ON signal without
the enable signal. A stop now fault will be
generated.
7) Send the enable signal without the clutch
contactor ON signal. A stop now fault will be
generated.
10. Run the Press in the Inch Mode.
a. Set the DMR parameter to the inch mode.
b. Enter five strokes per minutes
c. Set the DMR parameter to inch accel rate,
parameter No. 47. Enter the proper rate.
d. Jog the press through one or more strokes,
checking clearances, mechanical interference,
etc.
e. Use the Inch pushbutton for the jog function.
11. Resolver Adjustment
a. Select the top display area and select parameter
No. 04.
b. Select the bottom display area and select
parameter No. 77. Using the Down arrow set to
zero degrees (0º).
c. In the bottom area, select parameter No. 76 and
set for forward direction. Inch the press. If a
206 fault results, change parameter to REV. If
no fault, proceed to the next step.
d. Position the press to some known angle,
typically Bottom Dead Center (180º).
e. Select parameter No. 77 in the bottom area.
Using up or down arrows, adjust this parameter
until parameter No. 04 reads the position of the
press. This completes the setup of the resolver.
12. Operate the Press in the Run Mode.
a. Set the DMR to the run parameter.
b. Enter a profile of run speeds:
1) Enter degrees for six angles, parameters 30,
32, 34, 36, 38 and 40. If an angle is not
used, set it to the "skip angle" this is 360
degrees.
2) Enter strokes-per-minute for six speeds,
parameters 31, 33, 35, 37, 39 and 41.
3) Enter Operating Accel Rates, Nos. 1, 2 and
3, parameters 50, 51 and 52.
4) Enter Accel Rate Delta SPM, Nos. 1 and 2,
parameters 53 and 54.
5) Enter Operating Decel Rates, Nos. 1, 2 and
3, parameters 55, 56 and 57.
6) Enter Decel Rate Delta SPM, Nos. 1 and 2,
parameters 58 and 59.
7) Enter Initial Value of Linear Accel Ramp,
parameter 48.
Содержание CES
Страница 7: ...7 ...
Страница 37: ...Page is intentionally blank ...