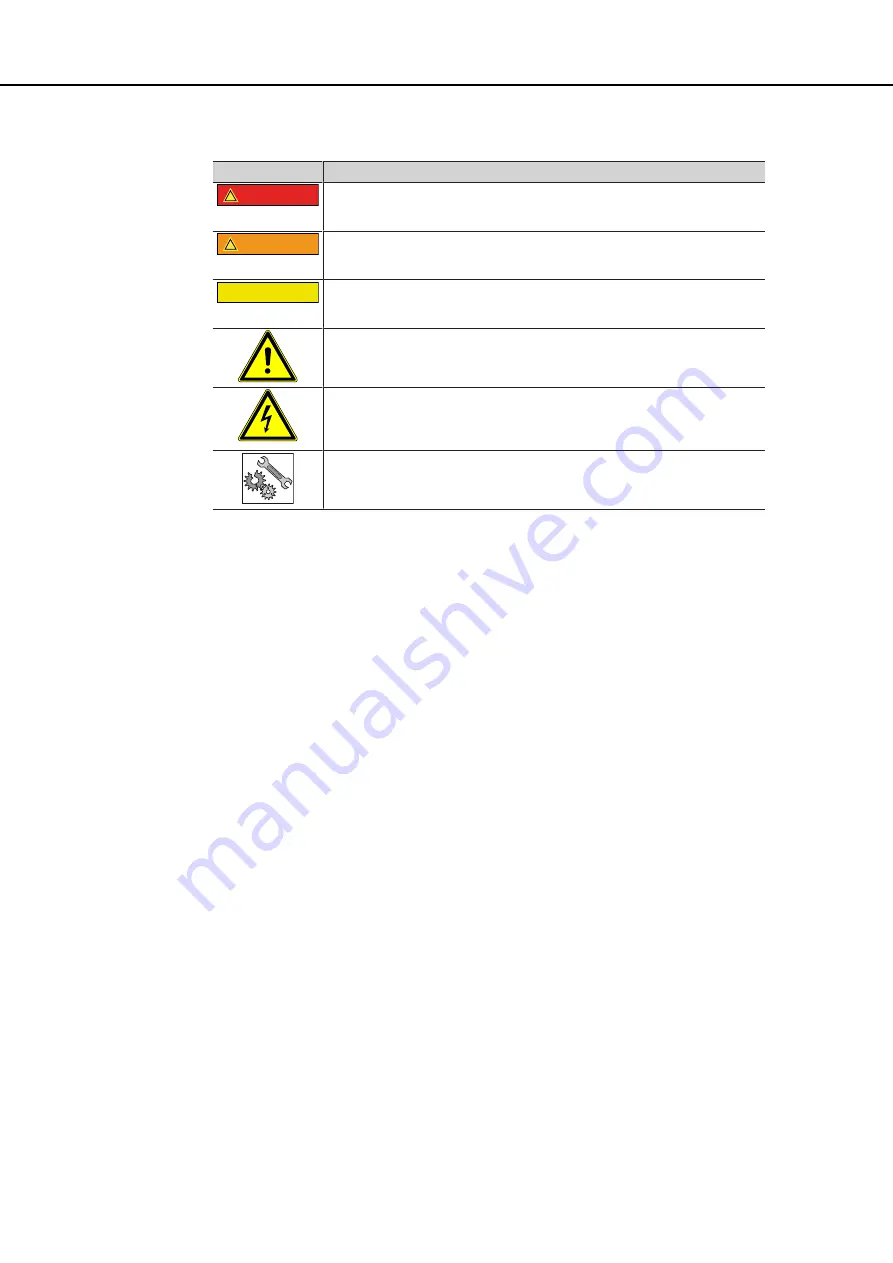
8 / 64
1.7 Key to safety symbols/markings
Table 3:
Definition of safety symbols/markings
Symbol
Description
!
DANGER
DANGER
This signal word indicates a high-risk hazard which, if not avoided, will result in
death or serious injury.
!
WARNING
WARNING
This signal word indicates a medium-risk hazard which, if not avoided, could
result in death or serious injury.
CAUTION
CAUTION
This signal word indicates a hazard which, if not avoided, could result in damage
to the machine and its functions.
General hazard
In conjunction with one of the signal words this symbol indicates a hazard which
will or could result in death or serious injury.
Electrical hazard
In conjunction with one of the signal words this symbol indicates a hazard
involving electrical voltage and identifies information about protection against
electrical voltage.
Machine damage
In conjunction with the signal word CAUTION this symbol indicates a hazard for
the machine and its functions.
Содержание Hydro-Unit Premium Line F
Страница 63: ......