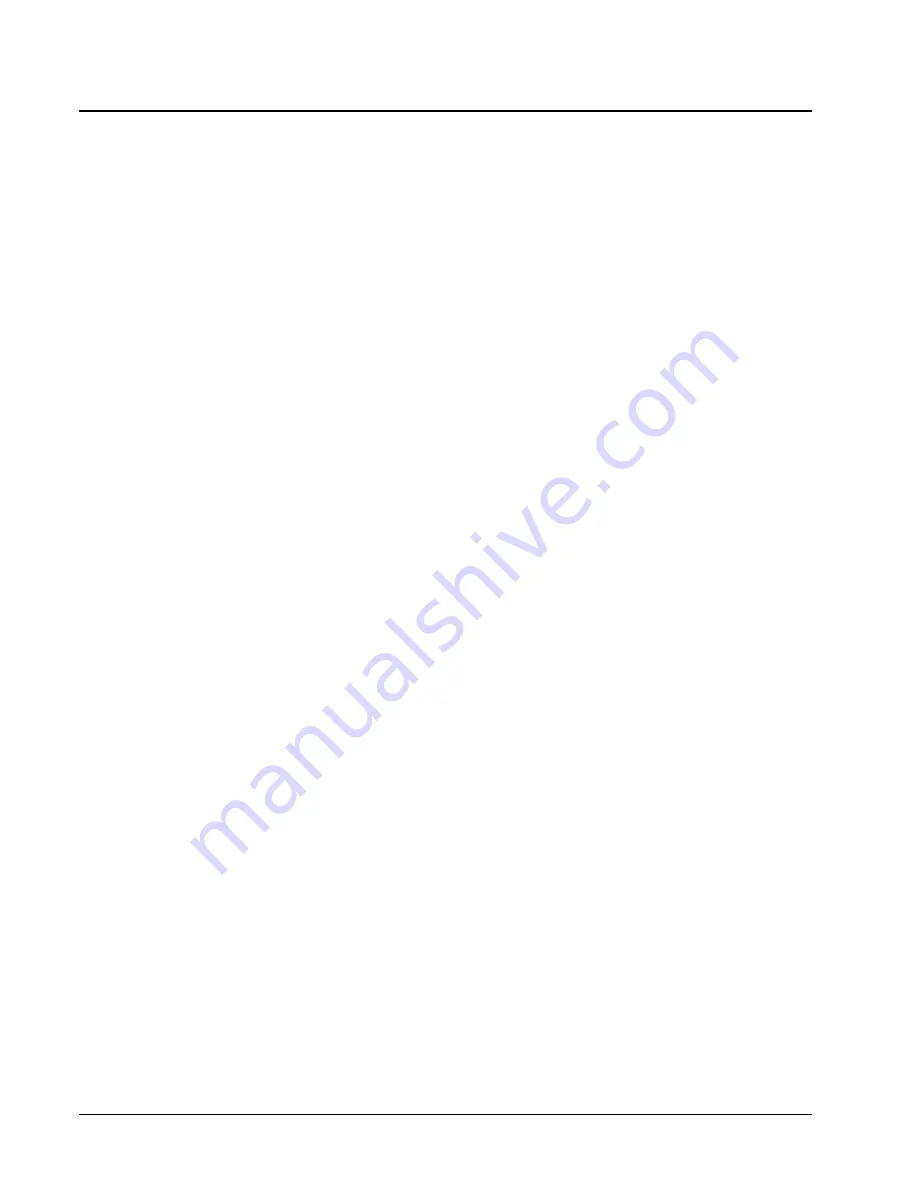
12
Recommended Input Configuration
The prime objective of a good input connection to an Index Drive is to maintain a constant shock-free
velocity.
Both the type of motor driving the indexer and the type of connection is of equal importance. Here we
explain some of the advantages and disadvantages of these factors.
1.
Worm gear
reducers with a high reduction provide two features. First, the flywheel energy due to
the high speed of the input. Secondly, the low efficiency of a worm gear reduces the effects of
back-driving and thus prevents input speed fluctuations.
2.
Timing belts
may be used if a worm gear drive is not suitable because of low gear reduction or
shaft arrangement requirements. Timing belts are desirable due to zero backlash and if properly
sized they have a long life. Timing belts also provide a flywheel effect of the pulleys and are
service free. (Note: Use tapered bushings in all pulleys and use a high service factor). The pulleys
selected should be as large as possible and the belts as short as possible to maximize the
flywheel effect, and minimize belt flexing.
3.
Zero backlash or rigid couplings
are suitable, especially with tapered bushings. During
installation, special care is required to assure alignment of the couplings. When selecting a
coupling a high service factor must be used. Brands available are Thomas Coupling, Rexnord,
Zurn Industries, etc. Some customers have been successful with rigid couplings, but alignment of
shaft becomes critical. Shaft failures are common in these situations.
4.
Gears and chains
are not very desirable and should be used only if no other method is possible.
Gears should be set to minimum backlash and maximized in size. Unless enclosed and oil
lubricated, only slow speeds are acceptable. Chains stretch and have backlash. A larger sprocket
size helps and some customers have been successful with self-adjusting idler arrangements.
5.
Line shafting
- Torsional windup is just as undesirable as backlash.
CAUTION: Long slender line shafts, rubber insert couplings, long belts and spongy mountings will
drastically increase actual torque demand which in turn raises torsional windup. Breakage or severe
vibration can result.
6. Permanent magnet motors fulfill two objectives, low cost and low inertia, but are at a disadvantage
for flywheel energy. This is especially serious for large dial and reciprocating applications.
DESTACO does not recommend operating permanent magnet motors below 1000RPM, and for
very heavy loads the minimum speed is 1500RPM or more. Failure to maintain these minimum
speeds will result in erratic input speeds and unpredictable torque levels.
7. Air and hydraulic motors can cause considerable problems. The inherent low inertia of these
motors and the resulting lack of adequate stored flywheel energy do not provide a reliable
constant input velocity.