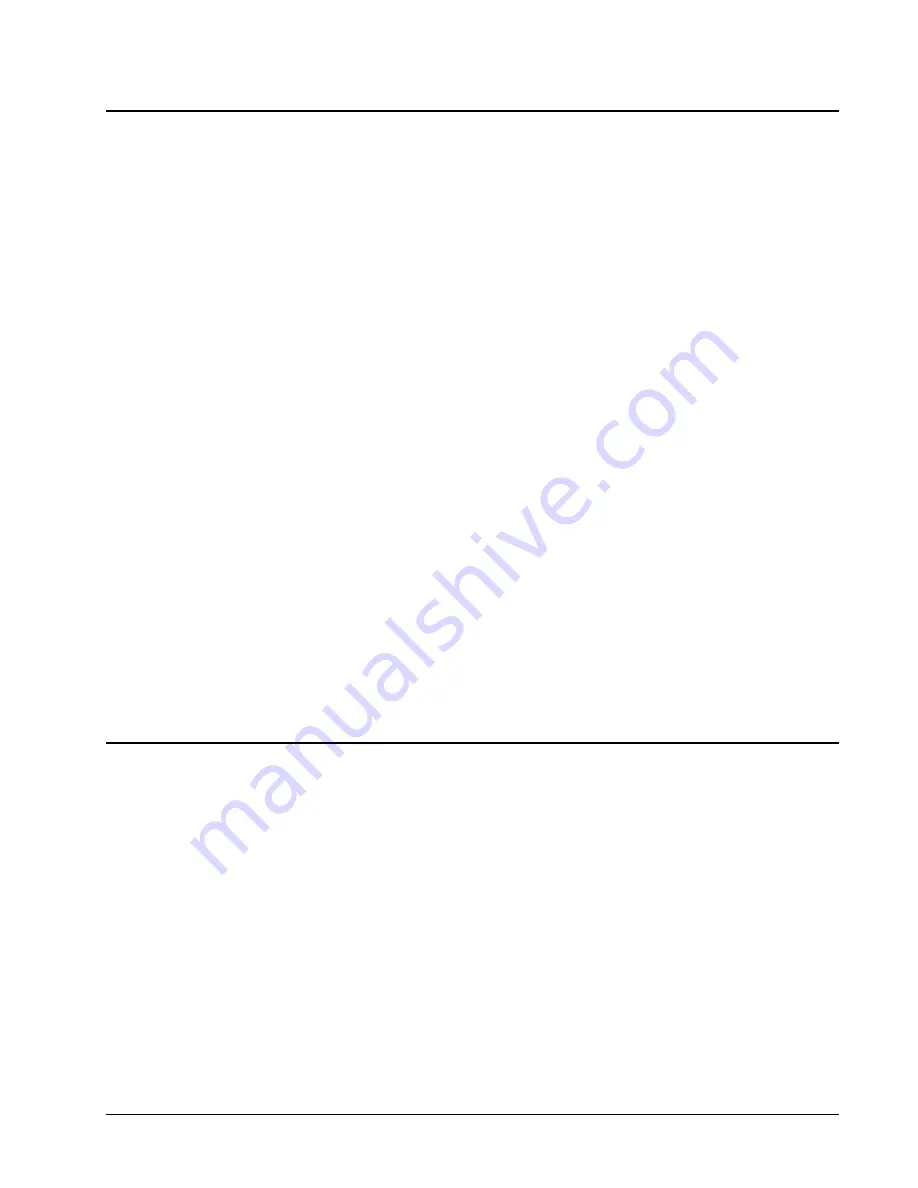
9
Overload Clutch
GENERAL
The CAMCO plunger-type output overload clutch is a reliable minimum service overload device
requiring very little attention (in a semi-clean environment) during its service life. The environment is
an important factor in the successful functioning of this device. A dusty or corrosive environment may
require special preparation or attention. (Contact DESTACO for special modifications). High humidity,
contaminants, or wash down applications may also require special protection. If rust forms within the
clutch, it may act as a solid coupling and will not release under overload conditions, (See lubrication
procedures).
NOTE
: For complete installation, operation and maintenance instructions, including
component identification drawing, contact DESTACO.
LUBRICATION
Under normal conditions the overload clutch will not require lubrication on a scheduled basis but the
overload clutch should be tested at least once every 6 months to be sure it is functioning properly. To
do this the output member (sprocket, dial, pulley, shaft etc.) should be locked by mechanical means,
then attempt to hand crank the reducer input shaft (or input shaft of the index drive if a reducer is not
used). By locking the output member the clutch should trip during index of the drive. If the clutch does
not function you could break a follower or cam during normal operation. Therefore, the clutch should
be taken apart, (as outlined in the "Clutch Installation, Operation and Maintenance Instruction Manual"
- Note all warnings and cautions) cleaned and a light coat of M
OBILGREASE
XHP222 grease applied
to the drive plate and mating surface of the clutch body. Also, lubricate the spring pockets with a light
film of grease.
CAUTION: Heavy lubrication in the spring pockets may lock the plunger, due to hydraulic pressure,
preventing the clutch from disengagement. In dusty, corrosive, high humidity, contaminants or wash
down environments, lubrication (as outlined above) should take place at least once every six (6)
months or sooner if required.
Long Term Reducer/Indexer Storage
1. Standard Shipping Procedure - Protection for Maximum Storage Duration of 30 Days.
Most Indexers are run-in tested using a rust inhibiting oil, drained, painted with one coat of
CAMCO metallic Blue, and all exposed shafting coated with a rust preventative prior to shipment.
This procedure is intended to protect the Indexers during shipment and short term inside storage
for a maximum period of thirty (30) days after shipment.
2. Long Term Storage (Indoors) for Periods up to One Year.
(a) Fill the Indexers completely full with one of the lubricants shown on our indexer list of
lubricants.
(b) Rotate the reducer worm shaft until you have completed one revolution of the output.
Rotate a least once per month to keep the seals from sticking to the wear rings and or
shafts.
(c) If it is not practical to rotate the input shafts periodically we recommend purchasing a set
of oil seals to have on hand in the event of seal leakage at start-up.
(d) Before putting the Indexers into service, lower the oil in the Indexers to the proper
operating oil level.