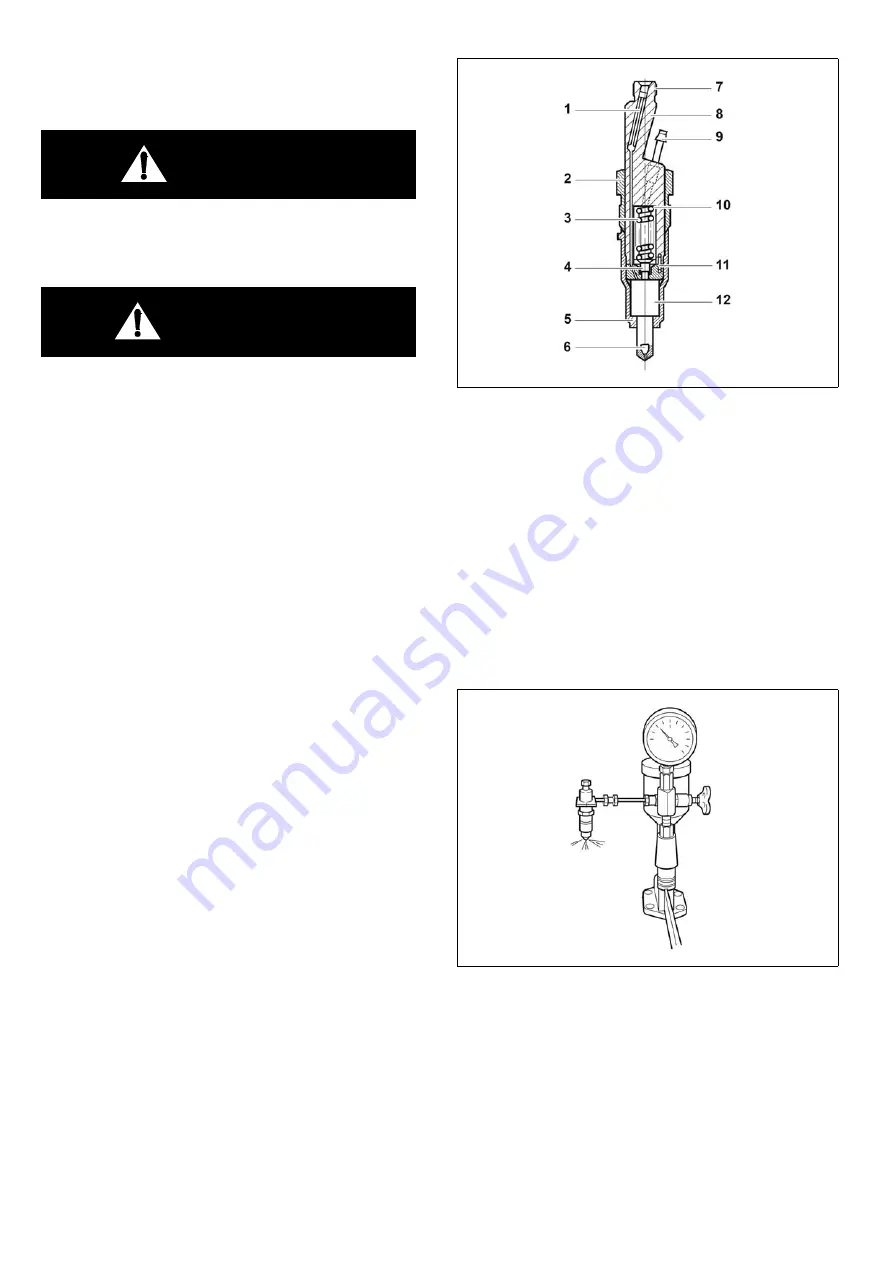
50 Hz: G625 - G690 - G750XW/XF
OPERATION & MAINTENANCE MANUAL
50
60 Hz: G655 - G750 - G800 - G850XW/XF
3.
Operate the priming pump until the air is discharged
completely.
DANGER
Fuel is highly inflammable. Fire may occur if there
are naked flames or sparks near the engine when air
bleeding in the fuel circuit from the priming pump.
CAUTION
If any parts that contain a seal ring (copper seal ring,
rubber coating seal ring, etc.) are disassembled, then
replace the seal ring with a new one. Failure to do so
may cause leakage in the fuel filter connections
preventing normal functioning.
INJECTOR MAINTENANCE
•
The injectors are designed to spray the fuel delivered
by the injection pump directly into the spherical
combustion chamber in the piston crown.
•
The injector consists of the nozzle and the nozzle
holder.
•
A copper gasket fitted to the injector ensures gas-tight
seating and good heat dissipation.
•
The opening pressure of the nozzle is adjusted by
means of shims at the compression spring.
FUEL INJECTION NOZZLE
1.
Install a nozzle to the nozzle tester.
2.
Check the fuel injection pressure. If the pressure does
not satisfy the reference value, adjust the injection
pressure of the nozzle using an adjustment shim.
3.
Check the nozzle spray status. If it is defective,
replace the nozzle.
1. Rod type filter
7. Connect hole for fuel
delivery
2. Cap nut
8. Nozzle holder
3. Compression spring
9. Connect tube for
overflow
4. Compression pin
10. Shim
5. Cap nut for fixed nozzle
11. Pin
6. Nozzle
12. Nozzle bush
DV2213022A
DV2213023A
Содержание G625XF
Страница 2: ......
Страница 4: ...50 Hz G625 G690 G750XW XF OPERATION MAINTENANCE MANUAL 4 60 Hz G655 G750 G800 G850XW XF ...
Страница 6: ...50 Hz G625 G690 G750XW XF OPERATION MAINTENANCE MANUAL 6 60 Hz G655 G750 G800 G850XW XF ...
Страница 104: ...50 Hz G625 G690 G750XW XF OPERATION MAINTENANCE MANUAL 104 60 Hz G655 G750 G800 G850XW XF WIRING DIAGRAMS ...
Страница 106: ......