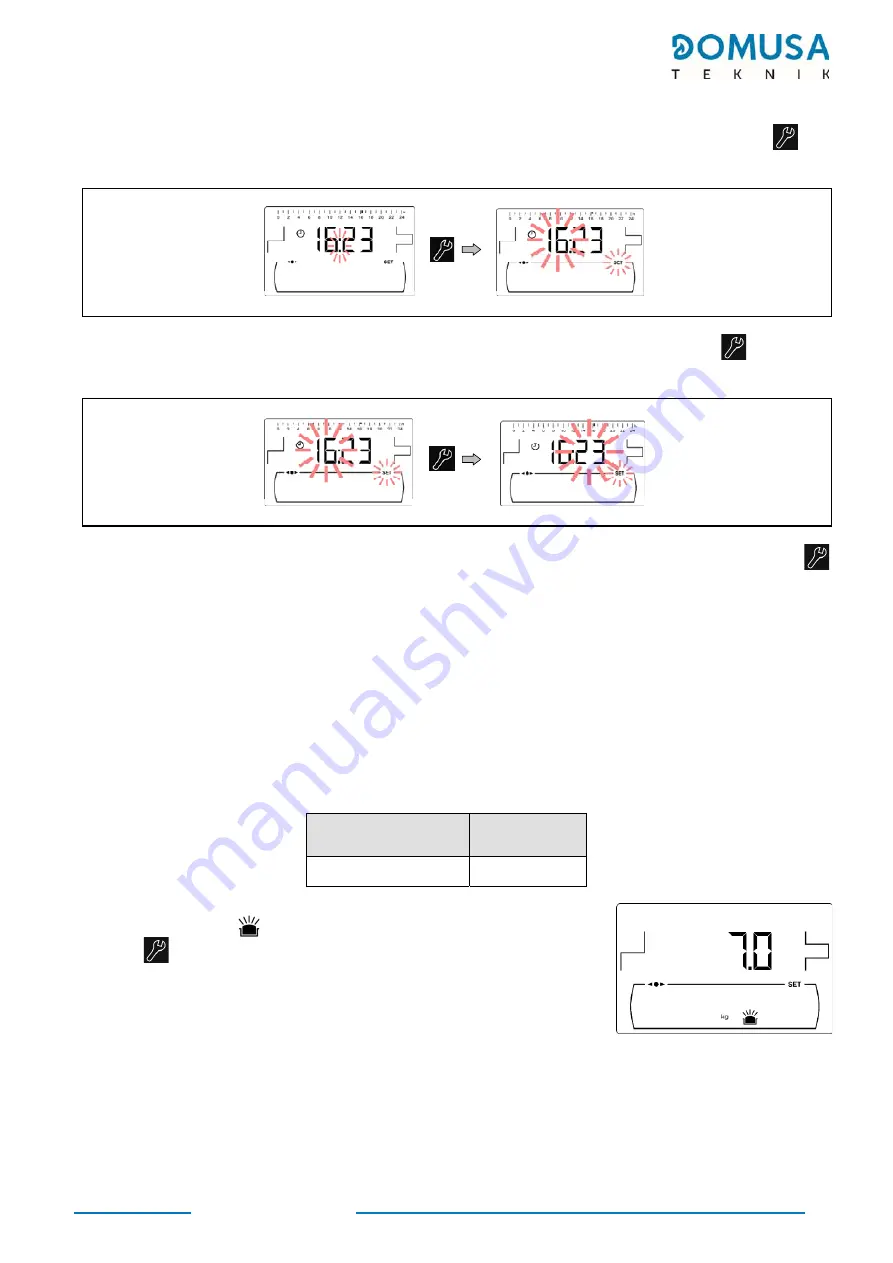
33
BIOCLASS iC 150
10.3
Adjusting the time
Once you have selected the time adjustment process from the
"Settings Menu"
by pressing
you
can access it, with
SET
and the two --'hour' digits will be flashing, beginning the adjustment process.
Using the symbols "
+
" or "
-
" of DHW
(21)
you can set the hour value and by pressing
the hour is
saved, before setting the minute digits.
Using the symbols "
+
" o "
-
" of DHW
(21)
you can adjust the minutes value and finally, pressing
will save it and return you to the
Settings Menu
.
10.4
Empty ash box notice
With this function activated, the boiler lets us know when the boiler ash box is full, so that we
proceed with its emptying. In the parameter
“Ash box status”
of the
“User Menu”
we can see its
status. When it is full, an "empty the ash box" notice is activated.
By default, the ash box reminder function is supplied activated and is set to indicative fuel
consumption values which, depending on the quality and type of fuel, will have to be adjusted for
each system. Shown below are the default number of pellet tonnes at which the boiler notifies you
to empty the ash drawer:
Model
Tn
BIOCLASS iC 150
7.0 Tn
To set the value of this function, once the display "Empty the ash box
notice" is selected (
) from the
"Settings Menu"
, by pressing the
symbol
we can access it;
SET
will begin flashing, and using the
symbols "
+
" or "
-
" of DHW
(21)
we can set the desired value.
NOTE: Every time a new value in this parameter is adjusted,
the ash box should be emptied.
Содержание BIOCLASS iC 150
Страница 1: ...BIOCLASS iC 150 Biomass boiler EN INSTALLATION AND OPERATING INSTRUCTIONS ...
Страница 2: ......
Страница 15: ...15 BIOCLASS iC 150 ...
Страница 64: ...EN 64 BIOCLASS iC 150 23 CONNECTIONS DIAGRAM 23 1 Boiler ...
Страница 68: ...EN 68 BIOCLASS iC 150 ...
Страница 77: ...77 BIOCLASS iC 150 NOTES ...
Страница 78: ...EN 78 BIOCLASS iC 150 NOTES ...
Страница 79: ...79 BIOCLASS iC 150 NOTES ...