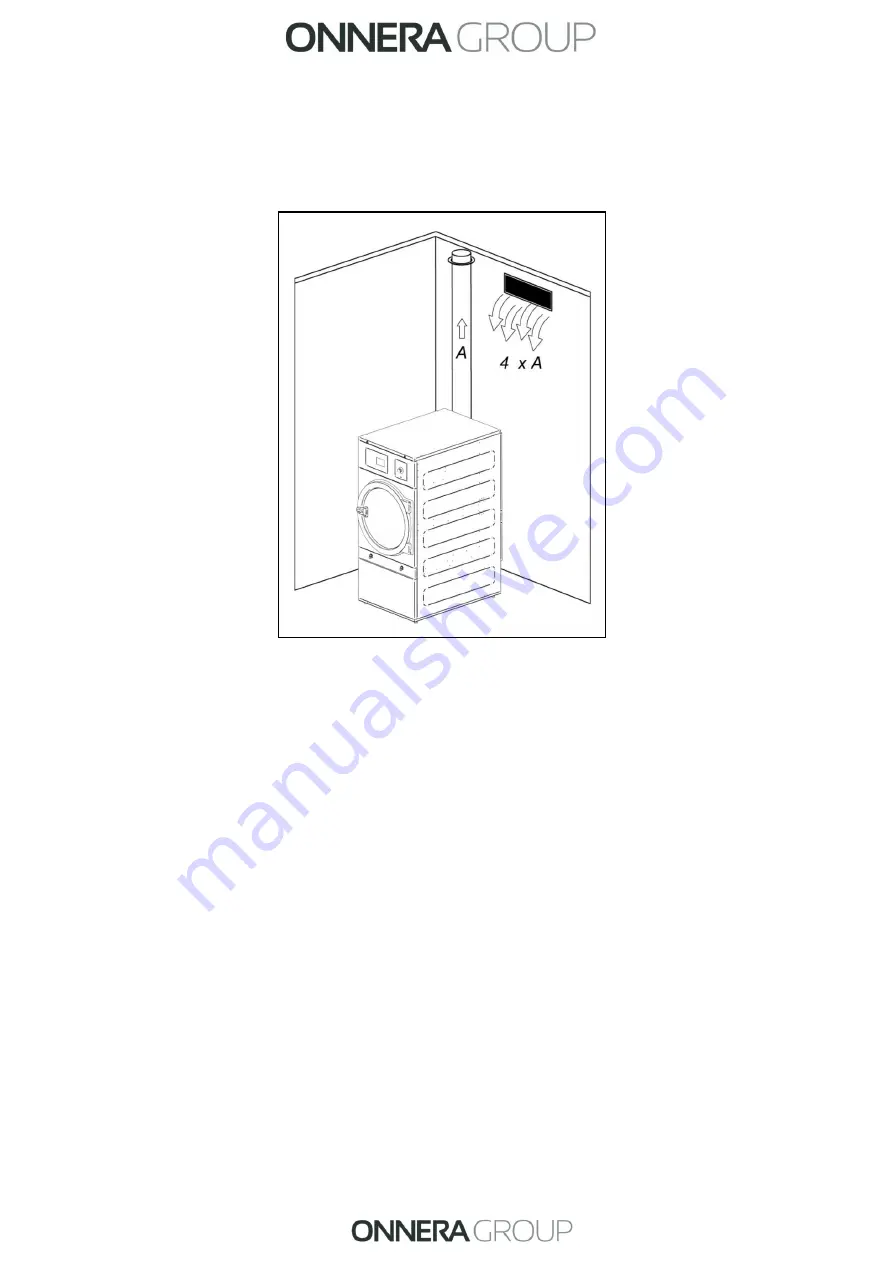
3.3. Vapour extraction
3.3.1. Entrance of fresh air
To ensure optimum performance and to minimise the length of the drying cycles, an input of
fresh air is required from outside the room. The fresh air inlet should be behind the dryer.
The area of the fresh air inlet should be at least 4 times more than area of the air output pipe.
Note:
The area of the fresh air inlet is equal to the area through the air is able to flow freely without
resistance from the bars or grille fitted across the entrance. Remember that the bars or vanes of the
grille often occupy a large portion of the area of the entrance.
3.3.2. Output pipe
Damp air should be channelled to the outside by connecting a pipe with a net diameter equal to the
exterior diameter of the steam output pipe. The extraction air should be taken outside the premises and
must never be connected to other fluepipes already in use for removing vapours from other fuels.
The location of these pipes must be within the limits established in the environmental heat legislation. A
pipe made of heat-resistant material should be used (302º F (150ºC)). Never leave the tube very near
inflammable materials or materials that are susceptible to deformation from excessive temperatures.
The tube must be smooth inside. It is important that there are no obstructions blocking the air flow or
that may result in a build-up of fluff (bolts, rivets, etc.) Systems for the regular inspection and cleaning
of the pipes should be set in place.
Each machine should preferably have an independent steam outlet. If this is not possible:
14