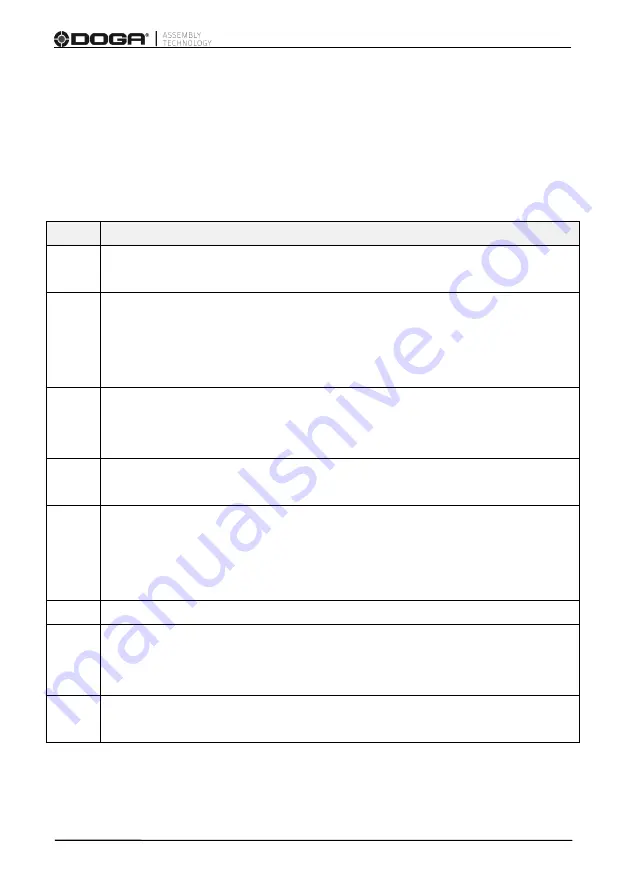
User manual DPC Touch V2
DOC.60352-11/20
50
4.4.4 Automatic programming of fastening step (GX/GY)
For automatic programming, make sure that the tool is connected to the
controller and signals are correctly assigned. In order to register tightening
time, Motor run and Fastening OK signals have to be connected.
Order Description
1
Position the arm on the first screw.
The arm's current encoder positions are displayed.
2
Default tolerance values for the approaching Area and for the OK
zone will be applied. To change default values refer to the encoder
settings. Tolerance values can be adjusted manually for each
individual position or by using Smart tolerance detection feature.
3
If necessary, define Tightening and Retightening programs to be used
for the current position, feeding point (see Pick Up position in
encoders’ settings) and the tool being used.
4
Perform a tightening operation as it has to be performed during
production
.
5
Tightening time will be registered automatically. Min and Max
tightening time limits are calculated automatically by using default
values in operating settings. Tightening time control is not used if
limits are equal to 0.
6
Repeat 1-5 for each position.
7
Activate Non-sequential mode if there is no need to keep strict
tightening sequence.
NOTE: in non-sequential mode, retightenings can’t be managed.
8
Press
SAVE
button to save the step or
CANCEL
button to quit
programming without saving changes
.