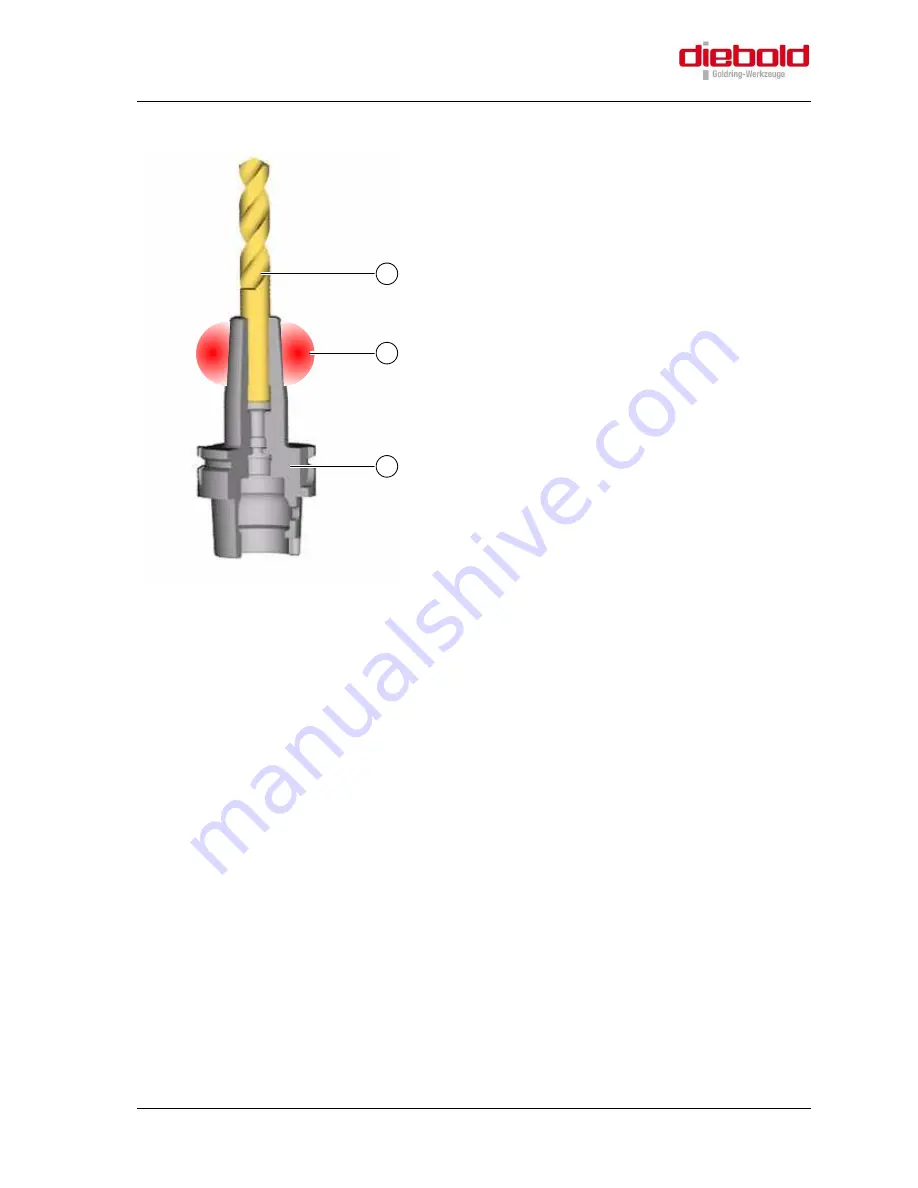
General information about ThermoGrip®
October 2014
ISG1000
9
3
General information about ThermoGrip®
Shrinking has been known as a technique for achieving
non-detachable connections, and offers remarkable
advantages for chucking tools. By the inductive heating
with high energy density, tools can be changed in a
matter of seconds.
A cylindrical tool (1) is pushed into a heated and
expanded bore of the chuck; after the chuck has cooled,
a high radial clamping force is applied. When handled
properly, the clamping operation is reversible and can be
repeated as often as required. The possible clamping
forces are higher than any conventional clamping
techniques.
Only shrink using clean tools in cleaned chucks!
Micro processor controlled
Induction generator ISG1000
With the help of special coils, only the specific clamping
area (2) of the chuck (3) is heated.
A special housing / shield surrounding the coil prevents
magnetic flux to a large extent. The control components
and the high frequency generator are integrated in the
housing.
Figure 2
Shrunk-in tool
All cables go through a protective hose. The coils have a high electric loading of up to 35A
induction current and up to 1000V voltage. The power has a short and partial impact on the
clamping area. Therefore little energy is induced into the clamping chuck.
Advantages of ThermoGrip
clamping technology at a glance:
Quick shrinking times in and out
High clamping forces
Higher tool and spindle life due to small run-out (< 3
µ
m)
Good surface finish due to high rigidity of the tool clamping system
High flexural yield strength and radial clamping strength and stability also with long body
lengths
Slim body of the chucks for high speeds
Only localized yet homogeneous heating of the chuck
Fastest possible cooling time of the tool and chuck
Specific heat-resistant steel give the chucks a high tool life and makes them dimensionally
stable
1
2
3