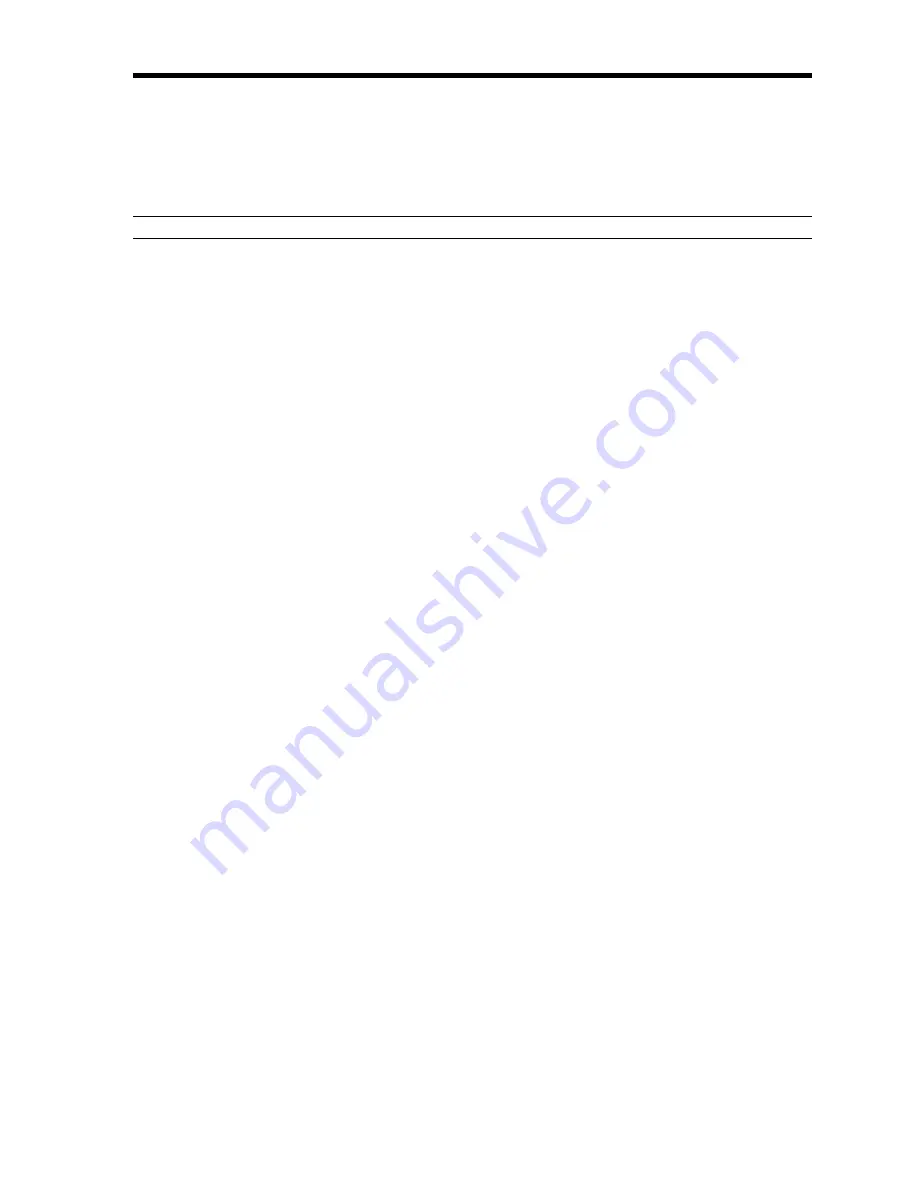
VMC 186/40 Motion Control Module How It Works
25
when extending and retracting. Thus the difference between the actual and target positions can be reduced by
increasing one of the three error gains. However, if a little bit of error gain is good, a lot is not always better.
The point at which the axis will oscillate depends on the response time of the system. The slower the response
time, the lower the error gains required to cause the system to oscillate. In general, use the largest error gain
possible that doesn't cause oscillations.
Note: The axis will oscillate if the proportional gain is too high.
Integral and Differential Gains
In addition to the three proportional error gains, there are two other gains: integral and differential. The
majority of applications do not require the use of either the integrator or differentiator. If used, start with a
value of 2 for the
Differential Gain
and 50 for the
Integral Gain
.
The integrator is only active when the axis is in motion. When a 'G' command is issued, the integrator starts
adding the position error (actual position - target position) to an accumulator every millisecond. As long as the
error is not approaching zero or has not changed sign, it is added to the accumulator. When the axis starts
ramping down, the accumulator is decremented at a rate calculated to bring the value to zero when the axis
stops. The drive provided by the integrator is given by:
Integral Gain
* Accumulator
Integral Drive =
20,000
The differentiator looks at the change in error between the target and actual positions over the last 20
milliseconds. The change in error is multiplied by the
Differential Gain
value to get the differential drive.
Differentiator Drive = (Error(t) - Error(t-20)) *
Differential Gain
Feed Forward
When the axis is moving, the difference between the target and the actual position may become large, even
when the error gain is as high as it can be without causing oscillations. There are two more parameters called
Extend Feed Forward
and
Retract Feed Forward
to help reduce the difference between the actual and target
position. The two feed forwards compensate for the system's physical differences between extending and
retracting. Feed forward is an open loop drive output that is proportional to the target speed of the axis. The
actual speed of the axis should be proportional to the drive output. The difference between the target speed and
the actual speed will be small if the feed forward is adjusted correctly. Therefore, the difference between the
target and actual position should be small while the axis is moving. If the feed forward is too low, the actual
position will lag the target position; if it is too high, the actual position will lead the target position and the axis
will overshoot the desired position.