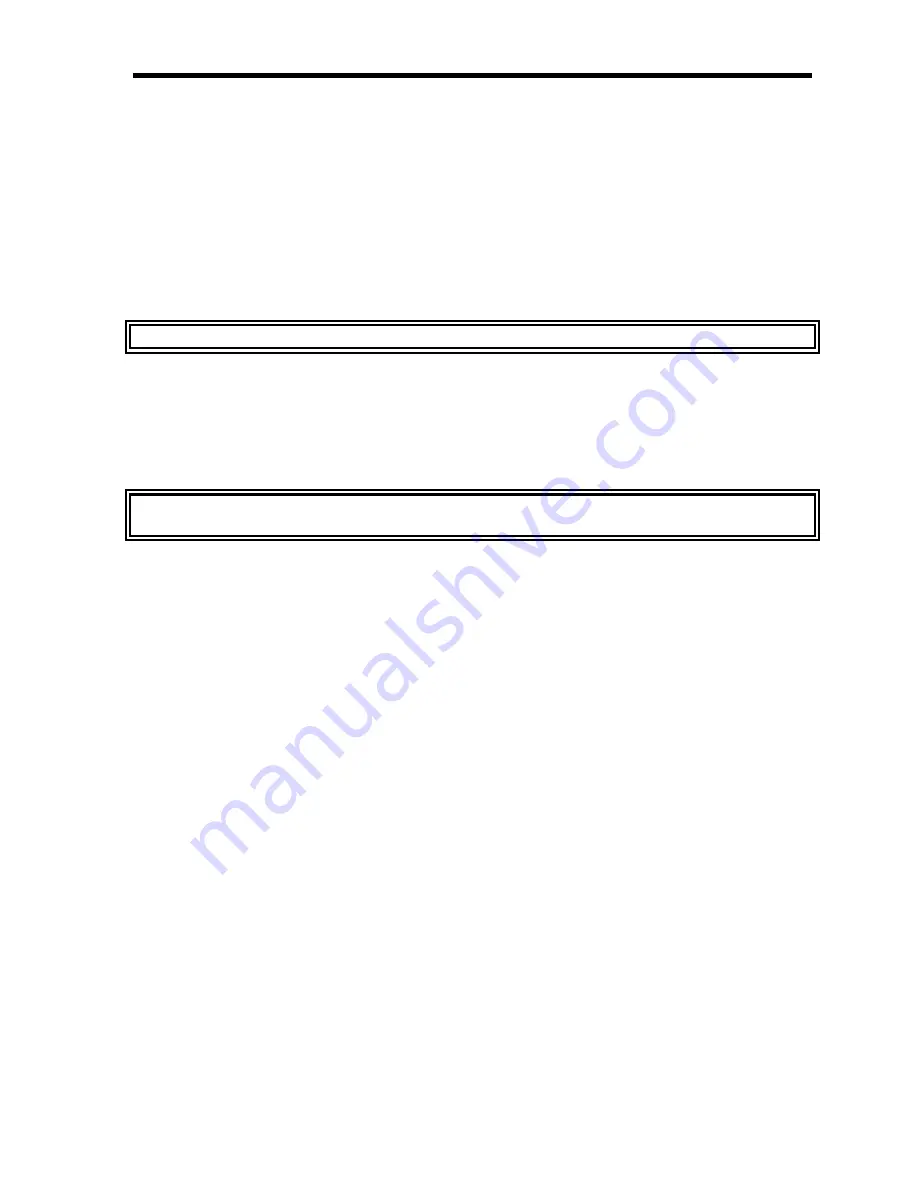
VMC 186/40 Motion Control Module Control Parameters
15
Dither (Default: 0)
The
Dither
value is the amplitude, in percent of full drive, of a 500 Hz square wave that is superimposed on the
normal drive output. A value of 10 will cause a square wave of 10% of the drive to be applied on top of the
normal output. This keeps the valve free and improves valve response. Leave this parameter at zero unless the
valve manufacturer recommends that dither be used.
Dither
is applied only when the axis is at rest.
Hysteresis (Default: 0)
Hysteresis
is used to compensate for drive dead band. Some valves and drives will not react to small changes
in output around the null drive value. The
Hysteresis
value is added or subtracted from the drive output,
depending on the direction of travel. The drive output should then be outside of the dead band.
CAUTION: Do not make this value too big or the drive will oscillate.
Static Gain (Default: 50)
Static Gain
specifies the amount of drive added to the drive output for a given amount of position error while
the axis is at rest.
Static Gain
is given in number of counts of drive per 100 units of error. The
Static Gain
should be set as high as possible without causing the axis to oscillate. See
Maximum Position Error
parameter
on page 19.
CAUTION: Increase the
Static Gain
slowly. Excessive gain can cause oscillations that could damage both man
and machine.
Extend Gain (Default: 50)
Extend Gain
is similar to the
Static Gain
, except it applies when the axis is extending. The gain while moving
can usually be a little higher than at rest. This will allow tighter control of the axis while moving. (Extending
is the direction that returns increasing transducer counts.)
Retract Gain (Default: 50)
The
Retract Gain
is similar to the
Extend Gain
except it is used for retracting only.
Integral Gain (Default: 0)
The
Integral Gain
is used to adjust the drive provided by the integrator while the axis is moving. The
Integral
Gain
field should be adjusted after the feed forwards have been set to optimal values. Using the integrator
before the feed forward's have been set properly will cause the system to overshoot at the set point.
When a 'G' command is issued, the integrator starts adding the position error (actual position - target position)
to an accumulator every millisecond. As long as the error is not approaching zero or has not changed sign, it is
added to the accumulator. When the axis starts ramping down, the accumulator is decremented at a rate
calculated to bring the value to zero when the axis stops. The drive provided by the integrator is given by:
Integral Gain
* Accumulator
Integral Drive =
20,000