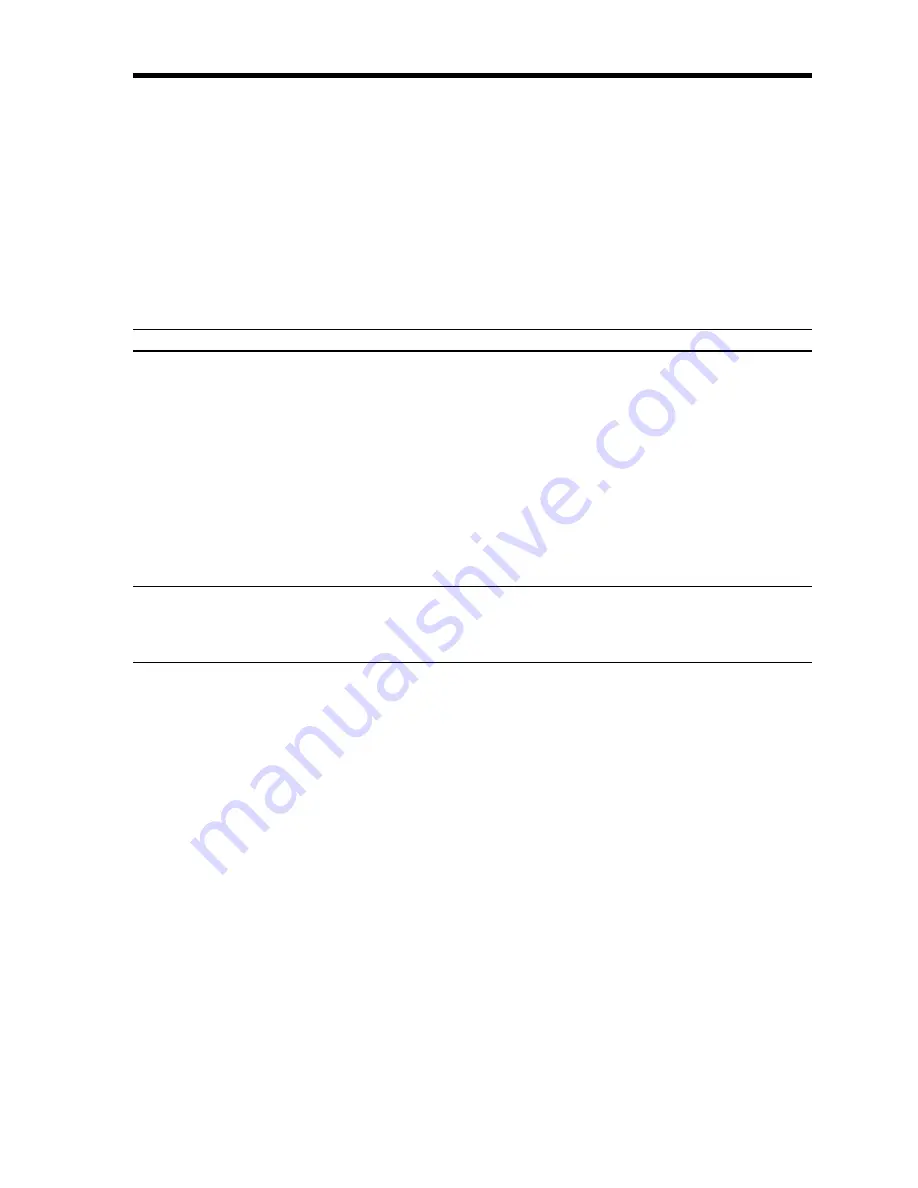
VMC 186/40 Motion Control Module Control Parameters
14
Feed Forward Advance (Default: 0)
If an axis will not respond to a change in the drive output until some time has passed, a large position error will
be generated. This can happen in applications that are moving large masses or have slow valves. By using
Feed Forward Advance
, the motion controller can time shift the feed forward portion of its drive output by the
number of milliseconds specified.
Feed forward advance is implemented by delaying the target position and target speed of the axis with respect
to the feed forward portion of the drive output by the
Feed Forward Advance
time. This can compensate for an
axis with a slow response time so the target and actual positions track more closely. Always use the minimum
amount to get the desired results. Both the target position and target speed will appear to be delayed with
respect to the drive output by the
Feed Forward Advance
time. One could also call this a target delay time.
Note: If the motion on two or more axes is being coordinated,
Feed Forward Advance
should be set the same.
Null Update (Default: 500) Range: 10 - 65535, 0 = disabled
Null Update
is the time in milliseconds that the drive null is checked and the value for
Null Drive
is updated.
Null Drive
on an ideal system should be zero milliamps (0 volts) or 2048 output to the digital to analog
converter. In a real system, a zero milliamp output may cause the axis to drift slowly so the real value of null
drive is something other than 2048.
When the axis is at the requested position, (had not been halted), the actual position is compared with the target
position at the interval specified by
Null Update
. If the actual position is greater than the target position, the
value of null drive is decreased by one. If the actual position is less than the target position, the value of null
drive is increased by one. This minimum value depends on the response of the system. For slow valves, use a
larger value in the range of 500-1000.
Note: The system will start to oscillate if the interval is too small, so decrease this number with caution. This
value is only meant to correct for the imperfections in the axis' null, not to aid the position error gain to quickly
get the actual position to the command position.
Fast response systems may work better with
Null Update
set to 0 (disabled).
Minimum Update Time (Default: 1000)
Minimum Update Time
is used to specify the minimum interval between position updates for the transducer. It
is possible for the transducer to generate position update interrupts in less then a hundred microseconds. The
default value allows each axis to be read every millisecond. The range of acceptable values is 0 to 2000
If the value is 0, the transducer position update interrupts will occur synchronously with the PID loop
calculations every millisecond. Using synchronous readings provides a means to determine exactly when the
position data is read. This reduces the variance between the measured position and actual position. Any
variance may create control errors when the VMC 186/40 is used with a high speed target.
If a value other than 0 is used, its range should be between 250 to 2000. The transducer position measurement
will not be synchronized to the system clock, but will be free running. This means the transducer position is
updated as often as possible. When the rod is retracted (position at a minimum), the updates can be so frequent
that all of the processing time of the VMC 186/40 can be used.
Minimum Update Time
is specified using axis one. There is only one setting for all four axes. The other axes
parameters are unused.