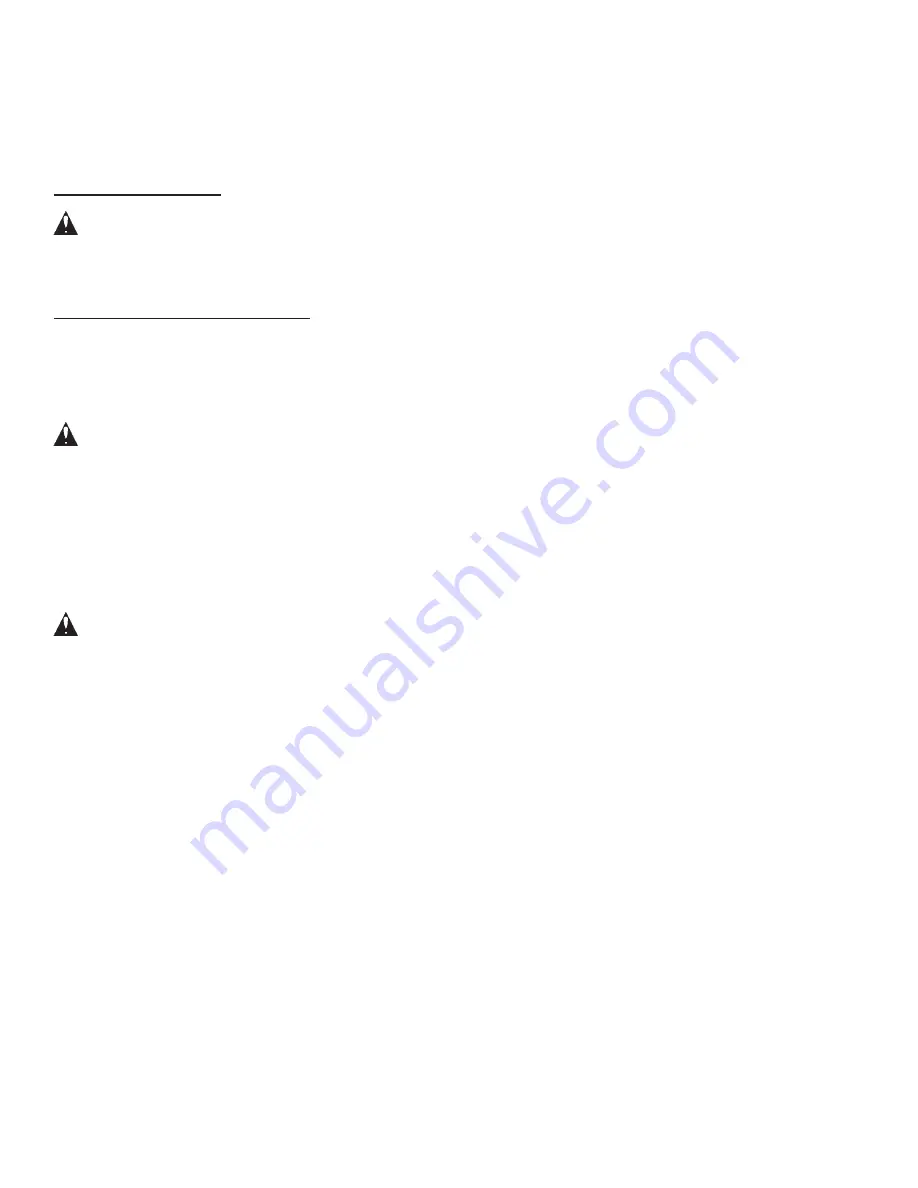
Page 10
3. The pilot is ignited, the electronic flame sensing proves the ignition source and turns on the second
valve allowing main gas to flow. (If pilot ignition does not occur within 60 seconds, the system will lock-
out and turn off power to gas circuit.)
4. The proved pilot ignites the main burner. (Pilot operation continues until Burner is shut off.)
5. The spark continues several seconds after the burner is lit to provide stable ignition.
Test for Gas Leaks:
WARNING: DO NOT OMIT THIS TEST.
With the main burner in operation, paint the pipe joints, pilot gas tubing
connections, and valve gasket lines with rich soap and water solution. Bubbles indicate gas leakage. To
stop leak, tighten the joints and screws or replace the gasket. Failure to do this test procedure could
cause serious injury.
Manual Shut Down Of Burner:
Complete shutdown can be accompished by turning the cock knob to the "Off" position.
INSTALLATION & SERVICING INSTRUCTIONS
WARNING: To avoid possible injury, fire, and explosion, please read and follow these precautions and all instruc-
tions on this machine. Maintenance and repairs performed by unauthorized personnel could result in
damage or injury. Servicing of this unit must always be referred to an authorized Delco distributor.
Repairs, adjustments, and servicing should be limited to the operations listed below.
1. Installation and servicing of gas appliances and ignition systems must only be performed by qualified personnel.
2. Turn off gas and electricity before starting installation or service. Turn back on after completion.
3. Caution must be taken to ensure that no raw gas is present in the surrounding area before attempting to put the
machine into operation.
WARNING: For your safety, if you smell gas: (A) turn off gas at line valve or meter, (B) open windows, (C) do not
touch electrical switches, (D) extinguish all open flames, (E) immediately call your gas supplier.
4. When using L.P.gas, the Control must be equipped with a regulator. Make sure that no gas is present in the area
before putting machine in operation. L.P. gas is heavier than air. Sniff at floor level for presence of gas. If
present do not attempt to start the machine. (See Warning on page 8.) When changing from natural gas to L.P.,
or L.P. to Natural Gas using a convertible control, the burner orifice and pilot orifice must also be changed.
5. Make certain that the pilot orifice being used is the correct size for the gas used.
6. To install or remove control, use a special body wrench on inlet boss. Do not grip body with pipe wrench
or vise.
7. Insert only correct size pipe or tubing into inlet or outlets of control. Insertion of any other objects can cause
internal damage resulting in a hazardous condition.
8. Make sure gas piping is pressure tested before control is connected. High pressure can damage control causing
a hazardous condition. Do not subject control to more than 1/2 P.S.I., (14" W.C.) inlet pressure.
9. Use only new, unused, and correct model controls as replacements. Do not re-use old controls.
10. Make sure piping is clean and free from burrs. Apply a small amount of good quality pipe thread compound
suitable for the gas being used. Thread compound should be used sparingly on male threads only, leaving the
first two threads clean.
NOTE
: Blow lines out with compressed air to remove all dirt or debris.
11. A drip leg (dirt trap) must be installed, after the shut-off valve, in the gas supply line to the control to prevent dirt
from entering control. See figure #1. All piping must conform to local codes and ordinances and with National
Gas code (ANSI Z223.1 and NFPA No. 54).
12. After installation has been completed, leak test all gas connections with soap solution with the main burner on.
Bubbles indicate leaks that must be corrected.
Содержание Avenger 1000-3 LP
Страница 19: ...Page 19 Delco Avengers 1000 3 NG LP Single Phase Assembly Drawing No 1 Machine Layout...
Страница 20: ...Page 20 Delco Avengers 1000 3 NG LP Single Phase Assembly Drawing No 2...
Страница 22: ...Page 22 Delco Avengers 1000 3 NG LP Single Phase Assembly Drawing No 3...
Страница 24: ...Delco Avengers 1000 3 NG LP Single Phase Assembly Drawing No 4...
Страница 26: ...DELCO Avenger 1000 3 NG LP Single Phase Pump Drawing...
Страница 28: ...DELCO Avengers 1000 3 NG LP Single Phase Electrical Schematic...
Страница 30: ...1111 E Lake Francis Dr Siloam Springs AR 72761 1 800 BUY DELCO...