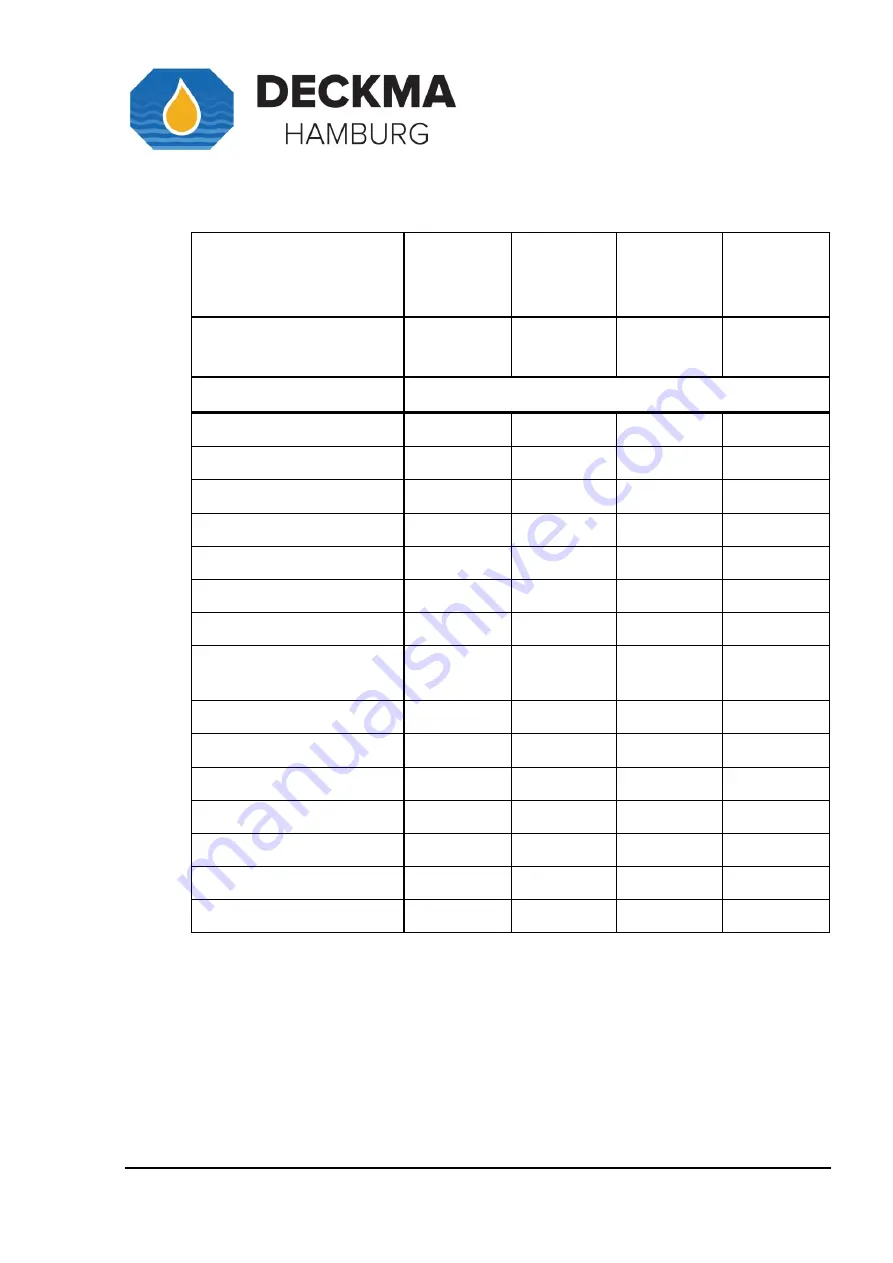
Page: 68 of 102
19.1 Recommended on Board Spares
OMD-2008 Series
OMD-2008
OMD-2008
EV
OMD-2008
EVA
OMD-2008
EVFC-MCU
ART-Number/
Alarm Set Point Limitation
10820/15ppm
10822/ 5 ppm
10821/15 ppm
10823/ 5 ppm
10825/15 ppm
10827/ 5 ppm
10830/ 15 ppm
10833/ 5 ppm
DESCRIPTION
ART-NUMBER
2 off Desiccator
79550
79550
79550
79550
1 off Cell Cleaning Brush
77555
77555
77555
77555
O-Ring Set
77775
77775
77773
77773
T2A Fuse
40107
40107
40107
40107
Electric Valve
13218
13218
13218
2 off Wiper Seal
77606
77606
1 off Service Kit
18570
18570
18570
18570
1 off Set of push in
connectors and hoses
78770
1 off Pneumatic Cylinder
78785
Optional Item
1 off Manual Cleaning Unit
77780
77780
Содержание OMD-2008
Страница 28: ...Page 27 of 102 5 5 Cabling OMD 2008 EV Figure 9 Bottom View OMD 2008 EV ...
Страница 84: ...Page 83 of 102 ...
Страница 85: ...Page 84 of 102 ...
Страница 86: ...Page 85 of 102 ...
Страница 87: ...Page 86 of 102 ...
Страница 88: ...Page 87 of 102 ...
Страница 89: ...Page 88 of 102 ...
Страница 90: ...Page 89 of 102 ...
Страница 91: ...Page 90 of 102 ...
Страница 92: ...Page 91 of 102 ...
Страница 93: ...Page 92 of 102 ...
Страница 94: ...Page 93 of 102 ...
Страница 95: ...Page 94 of 102 ...
Страница 99: ...Page 98 of 102 Type Approved by ...