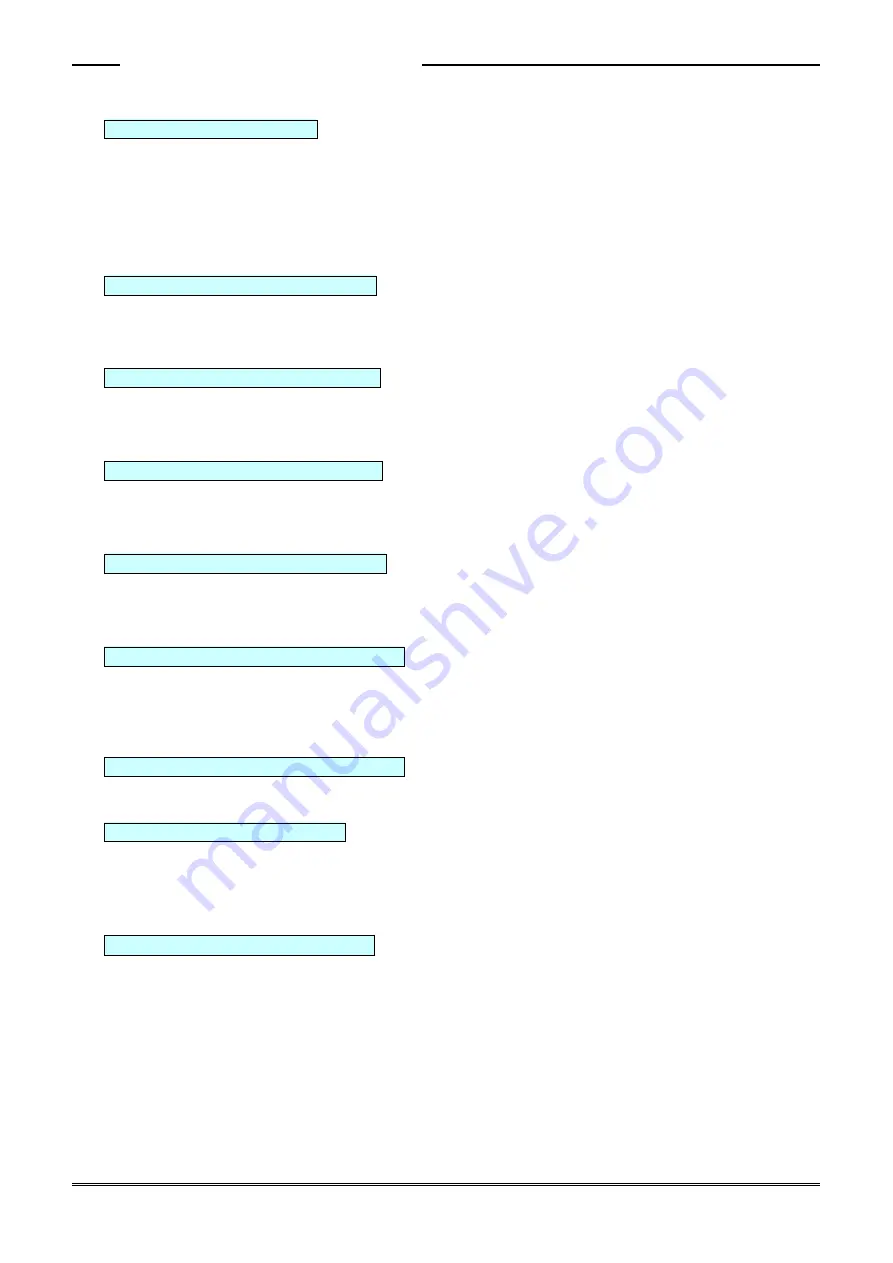
Chapter 6 Description of Operations
PAGE 6-70
(5)
Time
D-No. 310 Initial Time
[sec] Setting range: 0.0 ~ 999.9
The time for shock relaxation, fitting of the bolt and socket, etc., at the start of fastening is set.
Operation at D-No. 400 [Initial Speed] is executed during the initial time or during D-No. 500 [Freerun
Revolutions].
Although when “0.0” is set as the initial time, operation is started at D-No. 401 [Freerun Speed],
whe
n “0.0” is set as D-No.500 [Freerun Revolutions], operation at the initial speed is executed for the
initial time and thereafter, operation at the 1st speed is executed.
D-No. 311 1st Time Low Limit
[sec]
Setting range: 0.0 ~ 999.9
The value of the low limit of time until D-No. 105 [1st Torque] or D-No. 203 [1st Angle] is attained
from the start of fastening is set.If the time of attainment falls short of the 1st time low limit, the
REJECT Spindle judgment is made.
D-No. 312 1st Time High Limit
[sec]
Setting range: 0.0 ~ 999.9
The value of the high limit of time until D-No. 105 [1st Torque] or D-No. 203 [1st Angle] is attained
from the start of fastening is set.If the 1st time high limit is exceeded, the REJECT Spindle judgment
is made.
D-No. 313 2nd Time Low Limit
[sec]
Setting range: 0.0 ~ 999.9
The value of the low limit of time until D-No. 103 [Standard Torque] or D-No. 202 [Standard Angle]
is attained from the attainment of D-No. 105 [1st Torque] or D-No. 203 [1st Angle] is set.
If the time of attainment falls short of the 2nd time low limit, the REJECT Spindle judgment is made.
D-No. 314 2nd Time High Limit
[sec]
Setting range: 0.0 ~ 999.9
The value of the high limit of time until D-No. 103 [Standard Torque] or D-No. 202 [Standard Angle]
is attained from the attainment of D-No. 105 [1st Torque] or D-No. 203 [1st Angle] is set.
If the 2nd time high limit is exceeded, the REJECT Spindle judgment is made.
D-No. 315 Torque Recovery Time
[sec]
Setting range: 0.0 ~ 5.0
After the standard torque is attained, the standard torque is maintained for the torque recovery time.
Fastening equivalent to manual retightening is made possible.
* Normally, set this to 0. Otherwise, the abnormal state signal Abn.08-
10 “Overload Error” may be
generated.
D-No.316 1 Pulse Reverse Time
[sec]
Setting range: 0.0 ~ 9.99
This is the time used in D-
No. 006 [After Fastening Operation]: “1 Pulse Reverse.”
During the 1 Pulse Reverse Time, an operation for preventing the locking of the socket is performed.
D-No. 408 Ramp Up Time
[sec]
Setting range: 0.1 ~ 5.0, standard setting: 0.5
The time constant for acceleration from zero speed to attainment of the maximum rotation speed of
a tool in the fastening operation is set. The ramp up time is used in the following cases.
・
From the start of fastening by the raising (“OFF”
→
“ON”) of the PLC I/O input signal “START” to
attainment of D-
No. 400 “Initial Speed” or D-No. 401 “Freerun Speed.”
D-No.409 Ramp Down Time
[sec] Setting range: 0.0 ~ 5.0, standard setting: 0.5
The time constant for deceleration from the maximum rotation speed of a tool to attainment of zero
speed upon attainment of D-No. 500 [Freerun Revolutions] in the fastening operation is set.
Deceleration time (Freerun Revolutions) is used also for the downtime during manual reversing.
S0140185-H
Содержание HFC3000II
Страница 17: ...Chapter 1 Outline PAGE 1 1 Chapter 1 Outline 1 S0140185 H...
Страница 23: ...Chapter 2 Specifications PAGE 2 1 Chapter 2 Specifications 2 S0140185 H...
Страница 28: ...Chapter 2 Specifications PAGE 2 6 Memo S0140185 H...
Страница 29: ...Chapter 3 Part Names PAGE 3 1 Chapter 3 Part Names 3 S0140185 H...
Страница 36: ...Chapter 3 Part Names PAGE 3 8 Memo S0140185 H...
Страница 37: ...Chapter 4 Installation PAGE 4 1 Chapter 4 Installation 4 S0140185 H...
Страница 69: ...Chapter 6 Description of Operations PAGE 6 1 Chapter 6 Description of Operations 6 S0140185 H...
Страница 151: ...Chapter 7 Troubleshooting PAGE 7 1 Chapter 7 Troubleshooting 7 S0140185 H...
Страница 163: ...Chapter 8 Options PAGE 8 1 Chapter 8 Options 8 S0140185 H...
Страница 175: ...Chapter 9 External Interface PAGE 9 1 Chapter 9 External Interface 9 S0140185 H...
Страница 187: ...Chapter 9 External Interface PAGE 9 13 9 3 2 Description of the hardware RUN LED ERR LED CC Link Connector S0140185 H...
Страница 206: ...Chapter 9 External Interface PAGE 9 32 Memo S0140185 H...
Страница 207: ...Chapter 10 Warranty and Servicing PAGE 10 1 Chapter 10 Warranty and Servicing 10 S0140185 H...
Страница 210: ...Chapter 10 Warranty and Servicing PAGE 10 4 Memo S0140185 H...
Страница 211: ...Appendix List of Tool Models Appendix 1 Appendix List of Tool Models Appendix S0140185 H...
Страница 214: ...Appendix List of Tool Models Appendix 4 Memo S0140185 H...
Страница 215: ...Memo S0140185 H...