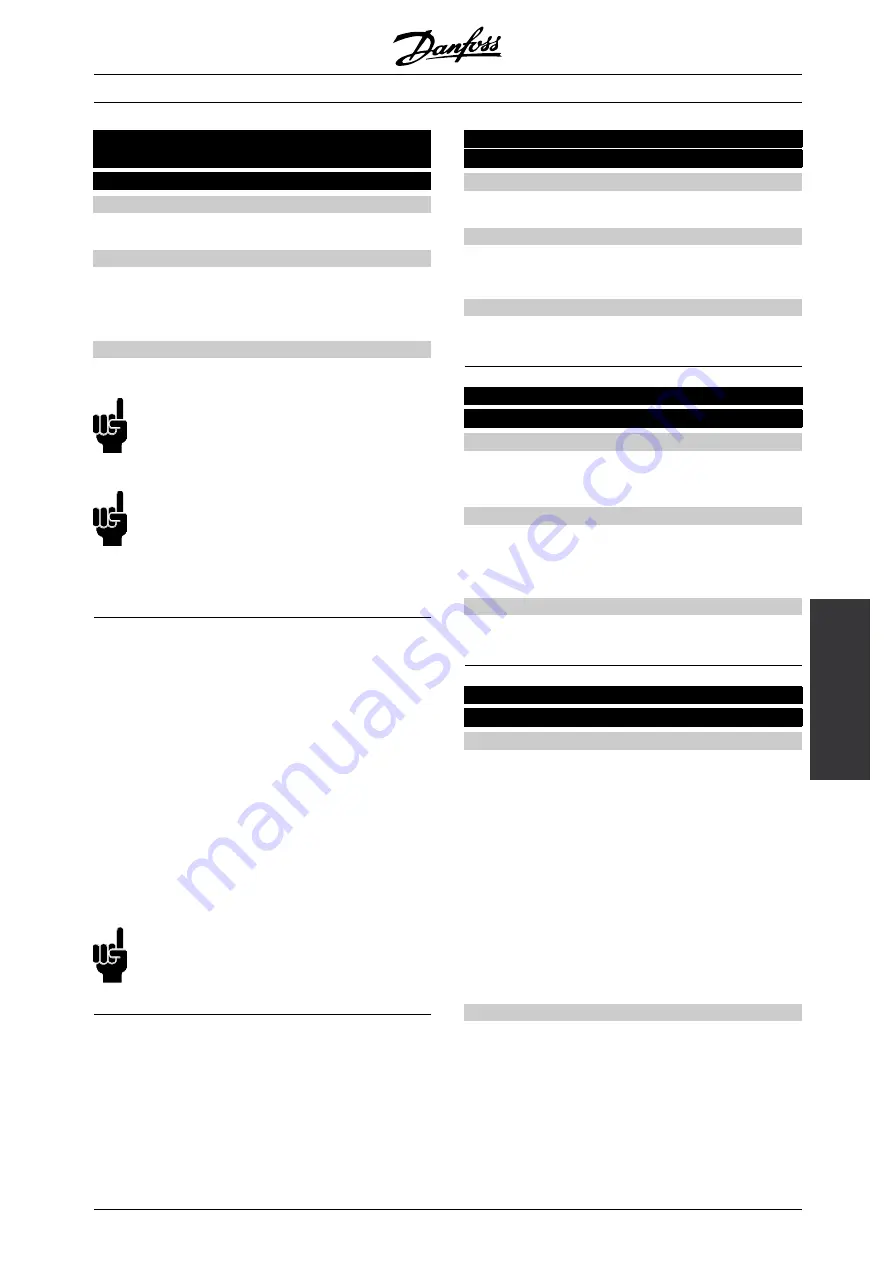
VLT
®
2800 Series
Programming
123 Min. frequency for activation of
function at stop
(MIN.F.FUNC.STOP)
Value:
0,1 - 10 Hz
✭
0,1 Hz
Function:
In this parameter, the output frequency is set at
which the function selected in parameter 122
Function at stop
is to be activated.
Description of choice:
Set the required output frequency.
NB!:
If parameter 123 is set higher than parameter
130, then the start delay function (parameter
120 and 121) will be skipped.
NB!:
If parameter 123 is set too high, and DC
hold has been chosen in parameter 122,
the output frequency will jump to the value
in parameter 123 without ramping up. This may
cause an overcurrent warning / alarm.
■
DC Braking
During DC braking DC voltage is supplied to the
motor, and this will cause the shaft to be brought to
a standstill. In parameter 132
DC brake voltage
DC
brake voltage can be preset from 0-100%. Max. DC
brake voltage depends on the motor data selected.
In parameter 126
DC braking time
DC braking time
is determined and in parameter 127
DC brake cut-in
frequency
the frequency at which DC braking becomes
active is selected. If a digital input is programmed to
DC
braking inverse
[5] and shifts from logic
’
1
’
to logic
’
0
’
,
DC braking will be activated. When a stop command
becomes active, DC braking is activated when the
output frequency is less than the brake cut-in frequency.
NB!:
DC braking may not be used if the inertia in
the motor shaft is more than 20 times greater
than the motor
’
s internal inertia.
126 DC brake time
(DC BRAKING TIME)
Value:
0 - 60 sec.
✭
10 sec
Function:
In this parameter, the DC brake time is set at which
parameter 132
DC brake voltage
is to be active.
Description of choice:
Set the required time.
127 DC brake cut-in frequency
(DC BRAKE CUT-IN)
Value:
0.0 (OFF) - par. 202
Output frequency high limit, f
MAX
✭
OFF
Function:
In this parameter, the DC brake cut-in frequency
is set at which the DC brake is to be activated
in connection with a stop command.
Description of choice:
Set the required frequency.
128 Thermal motor protection
(MOT.THERM PROTEC)
Value:
✭
No protection (NO PROTECTION)
[0]
Thermistor warning
(THERMISTOR WARN)
[1]
Thermistor trip (THERMISTOR TRIP)
[2]
ETR warning 1 (ETR WARNING 1)
[3]
ETR trip 1 (ETR TRIP 1)
[4]
ETR warning 2 (ETR WARNING 2)
[5]
ETR trip 2 (ETR TRIP 2)
[6]
ETR warning 3 (ETR WARNING 3)
[7]
ETR trip 3 (ETR TRIP 3)
[8]
ETR warning 4 (ETR WARNING 4)
[9]
ETR trip 4 (ETR TRIP 4)
[10]
Function:
The frequency converter can monitor the motor
temperature in two different ways:
-
Via a PTC thermistor that is mounted on the motor.
The thermistor is connected between terminal 50
(+10V) and one of the digital input terminals 18, 19,
27 or 29. See parameter 300
Digital inputs.
✭
= factory setting. () = display text [] = value for use in communication via serial communication port
MG.28.E9.02 - VLT is a registered Danfoss trademark
73