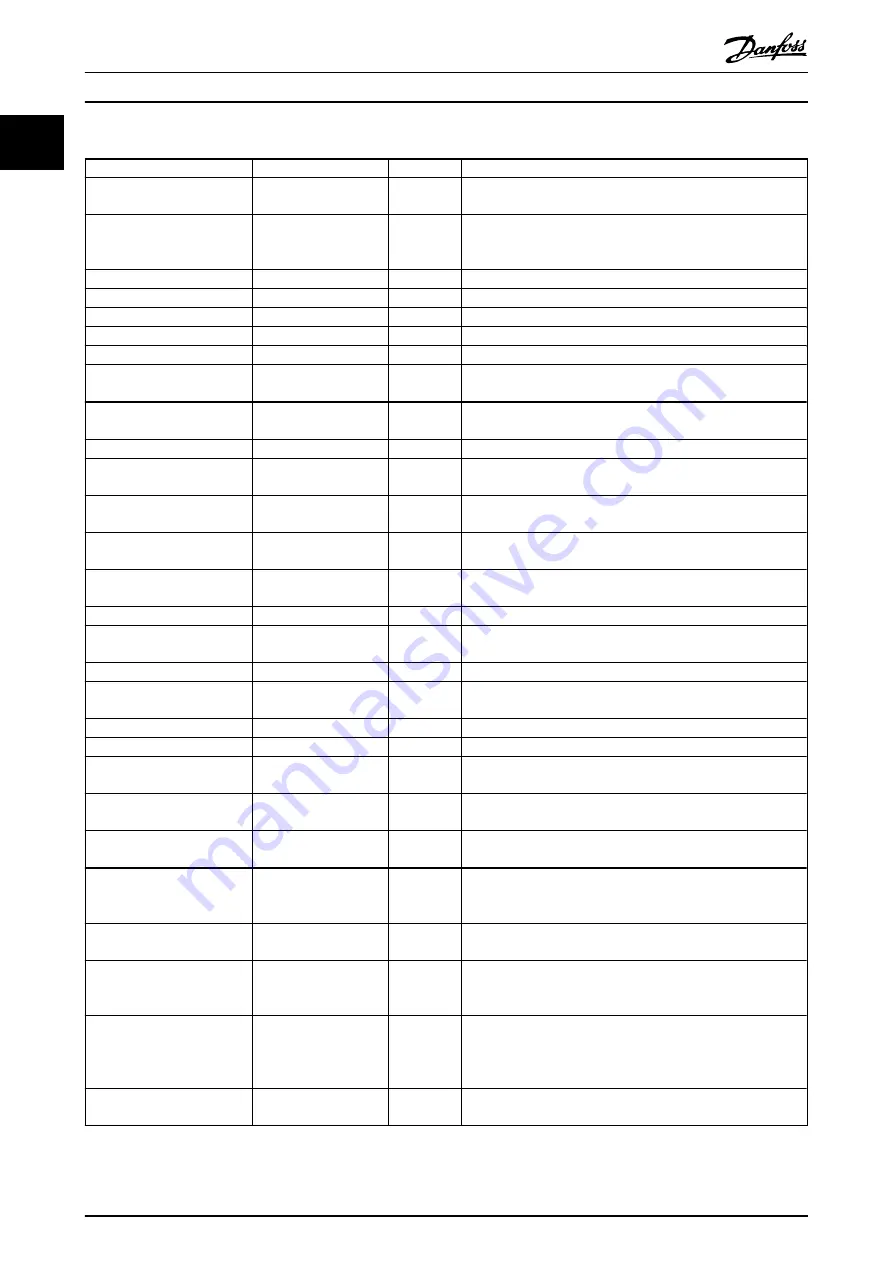
Closed Loop Set-up Wizard
No & Name
Range
Default
Function
0-03 Regional Settings
[0] International
[1] US
0
0-06 Grid Type
[0]-[[132] please see
start-up wizard for open
loop application
Size selected Select operating mode for restart upon reconnection of the
frequency converter to mains voltage after power down
1-20 Motor power
0.09-110 kW
Size related Enter motor power from nameplate data
1-22 Motor Voltage
50.0 - 1000.0 V
Size related Enter motor voltage from nameplate data
1-23 Motor Frequency
20.0 - 400.0 Hz
Size related Enter motor frequency from nameplate data
1-24 Motor Current
0.01 - 10000.00 A
Size related Enter motor current from nameplate data
1-25 Motor Nominal Speed
100.0 - 9999.0 RPM
Size related Enter motor nominal speed from nameplate data
4-12 Motor Speed Low Limit
[Hz]
0.0 - 400 Hz
0.0 Hz
Enter the minimum limit for low speed
4-14 Motor Speed High Limit
[Hz]
0.1 - 400 Hz
65Hz
Enter the maximum limit for high speed
3-41 Ramp 1 Ramp up Time
0.05 - 3600.0 s
Size related Ramp up time from 0 to rated motor frequency parameter 1-23
3-42 Ramp 1 Ramp Down
Time
0.05 - 3600.0 s
Size related Ramp down time from rated motor frequency parameter 1-23 to
0
1-73 Flying Start
[0] Disabled
[1] Enabled
0
Select Enable to enable the drive to catch a spinning motor
3-02 Minimum Reference
-4999-4999
0
The minimum reference is the lowest value obtainable by
summing all references
3-03 Maximum Reference
-4999-4999
50
The maximum reference is the highest value obtainable by
summing all references
3-10 Preset Reference
-100-100%
0
Enter the set point
6-29 Terminal 54 mode
[0] Current
[1] Voltage
1
Select if terminal 54 is used for current- or voltage input
6-20 Terminal 54 Low Voltage 0-10 V
0.07V
Enter the voltage that corresponds to the low reference value
6-21 Terminal 54 High Voltage 0-10 V
10V
Enter the voltage that corresponds to the low high reference
value
6-22 Terminal 54 Low Current 0-20 mA
4
Enter the current that corresponds to the high reference value
6-23 Terminal 54 High Current 0-20 mA
20
Enter the current that corresponds to the high reference value
6-24 Terminal 54 Low Ref./
Feedb. Value
-4999-4999
0
Enter the feedback value that corresponds to the voltage or
current set in parameter 6-20/6-22
6-25 Terminal 54 High Ref./
Feedb. Value
-4999-4999
50
Enter the feedback value that corresponds to the voltage or
current set in parameter 6-21/6-23
6-26 Terminal 54 Filter Time
Constant
0-10 s
0.01
Enter the filter time comstant
20-81 PI Normal/Inverse
control
[0] Normal
[1] Inverse
0
Select
Normal
[0] to set the process control to increase the
output speed when the process error is positive. Select
Inverse
[1] to reduce the output speed.
20-83 PI Start Speed
0-200 Hz
0
Enter the motor speed to be attained as a start signal for
commencement of PI control
20-93 PI Proportional Gain
0-10
0.01
Enter the process controller proportional gain. Quick control is
obtained at high amplification. However if amplification os too
great, the process may become unstable
20-94 PI Integral Time
0.1-999.0 s
999.0 s
Enter the process controller integral time. Obtain quick control
through a short integral time, though if the integral time is too
short, the process becomes unstable. An excessively long integral
time disables the integral action.
1-29 Automatic Motor
Adaption (AMA)
Off
Performing an AMA optimizes motor performance
Quick Guide
VLT HVAC Basic Drive Quick Guide
26
MG18A302 - VLT
®
is a registered Danfoss trademark
1
1