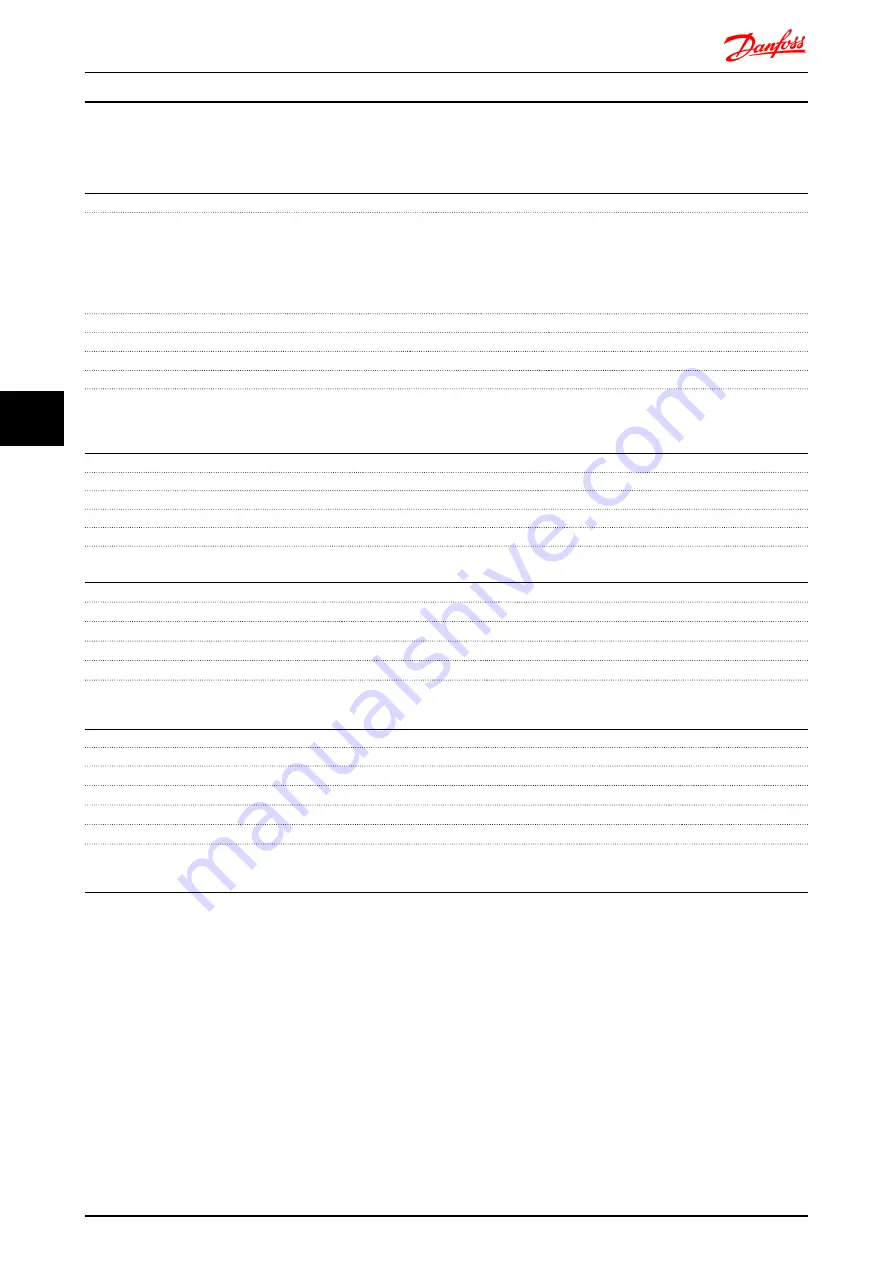
6.3 General Specifications
Mains supply (L1, L2, L3)
Supply voltage
380-480 V
±
10%
Mains voltage low / mains drop-out:
During low mains voltage or a mains drop-out, the frequency converter continues until the intermediate circuit voltage drops
below the minimum stop level, which corresponds typically to 15% below the FC's lowest rated supply voltage. Power-up and full
torque cannot be expected at mains voltage lower than 10% below the frequency converter's lowest rated supply voltage.
Supply frequency
50/60 Hz
±
5%
Max. imbalance temporary between mains phases
3.0% of rated supply voltage
True Power Factor (
λ
)
≥
0.9 nominal at rated load
Displacement Power Factor (cos
ϕ
)
near unity (> 0.98)
Switching on input supply L1, L2, L3 (power-ups)
maximum 2 times/min.
The unit is suitable for use on a circuit capable of delivering not more than 100,000 RMS symmetrical Amperes, 480 V maximum.
Motor output (U, V, W)
Output voltage
0-100% of supply voltage
Output frequency
0-1000 Hz
Output frequency in Flux Mode
0-300 Hz
Switching on output
Unlimited
Ramp times
0.01-3600 s
Torque Characteristics
Starting torque (Constant torque)
maximum 160% for 60 s
1)
Starting torque
maximum 180% up to 0.5 s
1)
Overload torque (Constant torque)
maximum 160% for 60 s
1)
Starting torque (Variable torque)
maximum 110% for 60 s
1)
Overload torque (Variable torque)
maximum 110% for 60 s
1)
1)
Percentage relates to the nominal torque.
Cable lengths and cross sections for control cables
1)
Max. motor cable length, screened
10 m
Max. motor cable length, unscreened, without fulfilling emission specification.
10 m
Maximum cross section to control terminals, flexible/ rigid wire without cable end sleeves
1.5 mm
2
/16 AWG
Maximum cross section to control terminals, flexible wire with cable end sleeves
1.5 mm
2
/16 AWG
Maximum cross section to control terminals, flexible wire with cable end sleeves with collar
1.5 mm
2
/16 AWG
Minimum cross section to control terminals
0.25 mm
2
/ 24 AWG
1)
Power cables, see tables in 6.2 Electrical Data and Wire Sizes of the FCD 302 Design Guide, MG04H
Protection and Features
•
Electronic thermal motor protection against overload.
•
Temperature monitoring of the heatsink ensures that the frequency converter trips if the temperature reaches a
predefined level.
•
The frequency converter is protected against short-circuits on motor terminals U, V, W.
•
If a mains phase is missing, the frequency converter trips or issues a warning (depending on the load).
•
Monitoring of the intermediate circuit voltage ensures that the frequency converter trips if the intermediate circuit
voltage is too low or too high.
•
The frequency converter constantly checks for critical levels of internal temperature, load current, high voltage on
the intermediate circuit and low motor speeds. As a response to a critical level, the frequency converter can adjust
the switching frequency and/ or change the switching pattern in order to ensure the performance of the drive.
Specifications
VLT
®
Decentral Drive FCD 302
84
MG04H102 - VLT
®
is a registered Danfoss trademark
6
6
Содержание vlt fcd 302
Страница 1: ...MAKING MODERN LIVING POSSIBLE Design Guide VLT Decentral Drive FCD 302 ...
Страница 92: ...www danfoss com drives MG04H102 130R0320 MG04H102 Rev 2012 05 08 ...
Страница 93: ......