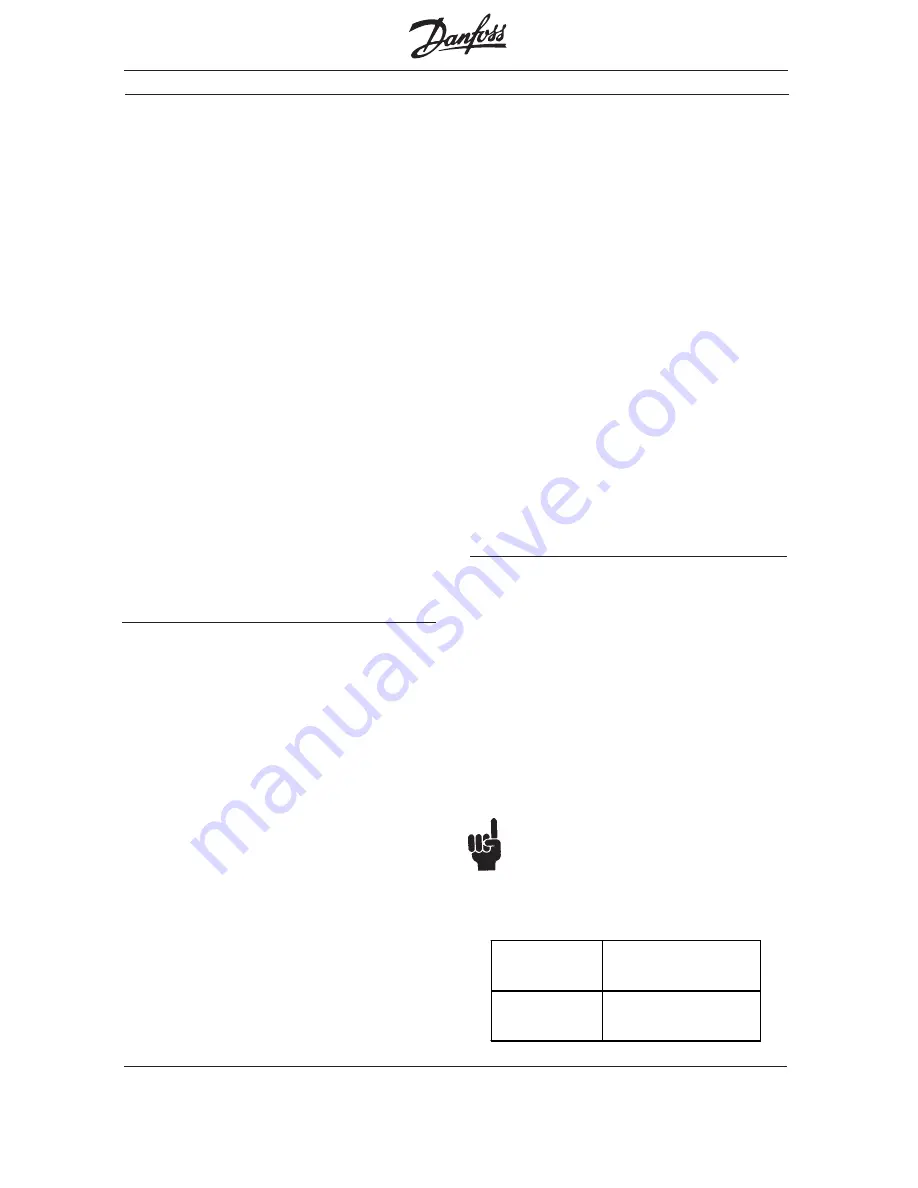
VLT
®
6000 HVAC
15
MG.60.G2.02 - VLT is a registered Danfoss Trademark
6 4
6 4
6 4
6 4
6 4
PI I TIME
PI I TIME
PI I TIME
PI I TIME
PI I TIME (parameter 424) - This sets the
integral time for the VLT 6000 PID controller.
It can have a value between 0.01 seconds
and 9999 (OFF). In order for the controller to
function properly, this should not be rned off.
6 5
6 5
6 5
6 5
6 5
PI GAIN LIMIT
PI GAIN LIMIT
PI GAIN LIMIT
PI GAIN LIMIT
PI GAIN LIMIT (parameter 426) - This sets
the maximum derivative gain for the
VLT 6000 PID controller. It can have a value
between 5 and 50.
6 6
6 6
6 6
6 6
6 6
LOWP
LOWP
LOWP
LOWP
LOWPASS FL
ASS FL
ASS FL
ASS FL
ASS FLTR
TR
TR
TR
TR (parameter 427) - This sets
the time constant for the noise filter in the
VLT 6000 PID controller feedback loop. It
can have values between 0.01 and 10
seconds.
6 8
6 8
6 8
6 8
6 8
FB FUNCTION
FB FUNCTION
FB FUNCTION
FB FUNCTION
FB FUNCTION (parameter 417) - This sets
how the VLT 6000 PID controller responds to
the drive’s two feedback signals. Its value is
an integer between 0 and 6. Refer to the
V
LT 6000 Operating Instructions
for the list of
choices and an explanation of each.
Network Outputs fr
Network Outputs fr
Network Outputs fr
Network Outputs fr
Network Outputs from the VL
om the VL
om the VL
om the VL
om the VLT 6000:
T 6000:
T 6000:
T 6000:
T 6000: The points
listed in Strategy One are commonly used.
■
■
■
■
■
Network Connection
Table 3 Tightening Torque and Wire Gage
Analog Input Monitoring:
Points 87, 88 and 89 can be used to monitor the
value of the analog control signals applied to
terminals 53, 54 and 60. These points are active
even when NO FUNCTION is programmed for the
analog input of the drive. As a result, it is possible to
use the VLT 6000 analog inputs as analog input for
the FLN.
Drive Relay Control:
While relay 1 and 2 in the VLT 6000 usually provide
drive status indications, these indications are
generally not needed when the drive is connected to
an FLN. In some applications, it can be useful to
have the FLN control these relays. For example, by
controlling one of the relays, the FLN could select
the active pump in a pump sequencing system. For
the FLN to control a drive relay, the appropriate
VLT 6000 parameter (323 or 326) must be set to
CONTROL WORD 11/12. Setting point 40 or 41 to
ON will then activate the corresponding relay.
■
■
■
■
■
VLT
6000 Special Functions
Safety Interlock:
The VLT 6000 can accept a safety interlock stop
command that is hard-wired to the drive control
terminals and another from the FLN. When
VLT 6000 parameter 304,
Digital Inputs
, is set to
SAFETY INTERLOCK, an open hard-wired safety
interlock will cause the drive to display ALARM 60
EXTERNAL FAULT. Setting point 28 to COAST will
display UN. READY in the lower right corner of the
drive’s display. The individual displays for each
allow the operator to determine which device
caused the trip. VLT 6000 parameter 503,
Coasting
Stop
, determines the interaction of these two
safety interlocks. See the
VLT 6000 Operating
Instructions
for details.
Connect the VLT 6000 to the FLN in accordance
with the following procedure (see Figure 2).
1.
Connect signal wires to terminal 68 (P+) and
terminal 69 (N-) on main control board of drive.
(See tightening torque and wire size in Table 3.)
2.
If shielded cabling is used, connect one end of
shield to terminal 61. This terminal is connected
to ground via an internal RC link.
NOTE:
NOTE:
NOTE:
NOTE:
NOTE:
It is recommended to use shielded, twisted-
pair cables to reduce noise between
conductors.
In addition to the control strategies described
above, the VLT 6000 provides additional control
flexibility to allow it to integrate into special control
systemrequirements. The following are just a few
examples.
Torque Specs
4.5 in Ib/0.5 Nm
Control wire
18 24
AWG,
shielded,
twisted pair/1.5 mm,
shielded twisted pair